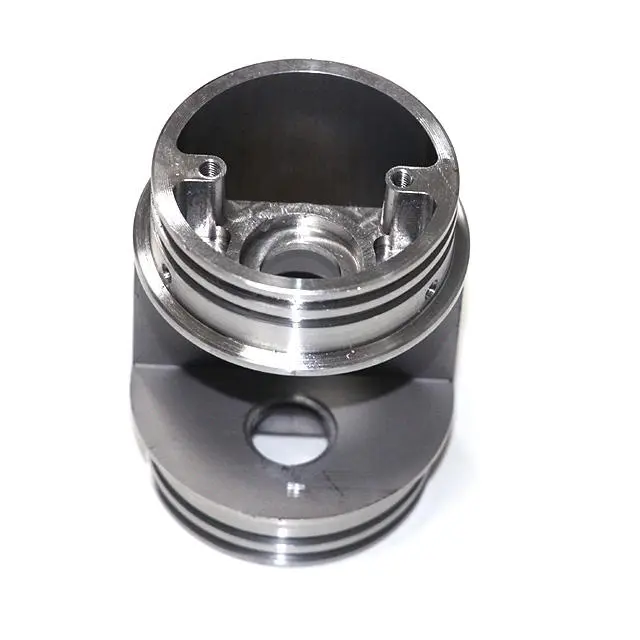
- +8615586668226
- [email protected]
- No. 30, Hongbang Industrial Park, Shenzhen
Plastic extrusion is a high-volume manufacturing process where plastic material is melted and formed into a continuous profile. Think of it like squeezing toothpaste out of a tube – the toothpaste is the molten plastic, the tube is the extruder, and the opening is the die that shapes the final product. This process is essential for creating everything from plastic pipes and tubing to window frames and packaging materials.
Plastic extrusion is a continuous process, meaning it can produce long lengths of product without interruption. This makes it highly efficient and cost-effective for large-scale production. The continuous nature of plastic extrusion allows for consistent product dimensions and quality.
The plastic extrusion process begins with raw plastic, often in the form of pellets or beads, being fed into a hopper. From the hopper, the raw plastic enters the extruder barrel, which contains a rotating screw. This screw conveys the plastic forward while simultaneously heating and melting it. The molten plastic is then pushed through a die, which shapes the plastic into the desired cross-section.
As the extruded plastic emerges from the die, it passes through a cooling system, often a water bath or a series of cooling rolls. This cooling process solidifies the extruded plastic evenly, maintaining its shape. Finally, the solidified plastic is cut or coiled, depending on the final product.
Several types of plastic extrusion cater to diverse manufacturing needs. These include:
Sheet/Film Extrusion: Used to create thin, flat plastic sheets and films for products like packaging, agricultural films, and stationery. The thickness of these films can be precisely controlled, ranging from thinner plastic films to thicker sheets.
Tubing Extrusion: Creates hollow plastic tubes for applications like plumbing, medical tubing, and wire insulation.
Blow Film Extrusion: A specialized process used to produce plastic films for bags and other flexible packaging. This involves extruding a tube of molten plastic and then inflating it like a balloon to create a thin film.
Over Jacketing Extrusion: This technique coats cables or wires with a protective layer of plastic. This insulation protects the inner wire and is common in electronics.
Broadly, plastic extrusion is categorized into four main types:
Hot Extrusion: The most common type, using heat to melt the plastic before forcing it through the die. Think of standard plastic tubing.
Cold Extrusion: Occurs at room temperature and is suitable for materials that are ductile enough to be deformed without heating. Cold extrusion occurs at room temperature, often involving metals rather than plastics.
Warm Extrusion: Falls between hot and cold extrusion, using moderate heat to improve material flow and reduce forces required.
Micro Extrusion: Creates extremely small and intricate plastic parts, often used in medical devices or microelectronics.
Plastic extrusion boasts numerous advantages:
High Volume Production: The continuous nature of plastic extrusion allows for efficient, high-volume production of plastic products.
Versatility: A wide range of plastic materials can be extruded, creating a diverse array of products. Extrusion technologies can create complex shapes, and custom plastic extrusion allows for highly tailored solutions.
Cost-Effective: The automation potential and continuous production lower the per-unit cost, making it an economical choice.
Design Flexibility: Dies can be customized to produce complex cross-sections, offering significant design freedom.
Different types of extruders exist, each designed for specific applications:
Single Screw Extruder: The most common type, uses a single rotating screw to convey and melt the plastic. This plastic extruder is versatile and widely used.
Twin Screw Extruder: Utilizes two intermeshing screws, offering superior mixing and higher output. Twin screw extruders offer advantages in mixing and output.
Ram Extruder: Uses a hydraulic ram to push the plastic through the die, suitable for processing high-viscosity materials.
The applications of plastic extrusion are vast and span numerous industries, including:
Packaging: Plastic films, bottles, containers, and closures are often produced via extrusion. Think about all the plastic packaging you encounter daily – much of it is made through extrusion.
Construction: Window frames, pipes, siding, and decking often utilize extruded PVC. PVC is a common plastic extruded for construction applications.
Automotive: Plastic trim, bumpers, and interior components frequently rely on extrusion. The automotive industry makes extensive use of extruded plastic components.
Medical Devices: Catheters, tubing, and other medical components are often made through extrusion. Medical Devices utilize the precision offered by extrusion.
Electronics: Wire insulation, cable jacketing, and other electronic components benefit from extrusion. Electronics heavily rely on extruded plastics.
Many industries rely on dedicated extrusion services to fulfill their specific needs. These can range from customized designs to large-scale production runs. Sectors such as aerospace, automotive, and medical devices often outsource extrusion due to the specialized expertise required. Using CNC Solutions can further enhance the precision and complexity of the final products. The aerospace industry frequently utilizes these specialized services.
Modern plastic extrusion is constantly evolving, incorporating new technologies and materials. Advancements in extrusion technologies and the use of recycled plastic are shaping the future of this field. From improvements in screw design to the integration of computer control systems, extrusion lines can be highly automated and optimized for maximum efficiency. Rapid Prototyping using extrusion allows for quick development and testing of new designs.
Sustainability is a key driver in modern plastic extrusion. Using recycled plastic and developing biodegradable polymers are becoming increasingly important. The drive to reduce plastic waste is leading to innovative solutions in material science and extrusion processes.
The future of plastic extrusion lies in further automation, increased use of recycled materials, and development of new, high-performance polymers. The industry continues to adapt to changing environmental concerns and consumer demands. The development of bio-based plastics and the advancement of additive manufacturing technologies are also expected to play a significant role in shaping the future of plastic extrusion.
What is the difference between plastic injection molding and extrusion? Injection molding creates discrete parts by injecting molten plastic into a mold, while extrusion creates continuous profiles.
What types of plastics can be extruded? A wide range of thermoplastics, including polyethylene (PE), polypropylene (PP), polyvinyl chloride (PVC), and polystyrene (PS), can be extruded.
How precise is the plastic extrusion process? Extrusion can achieve high precision, with tolerances often within thousandths of an inch. The precision depends on the specific equipment and process parameters.
Is plastic extrusion environmentally friendly? The environmental impact of plastic extrusion is a concern, but advancements in recycled materials and biodegradable plastics are helping to mitigate this.
How do I choose the right extrusion process for my needs? The choice of process depends on factors such as the desired product shape, material properties, production volume, and budget. Consulting with experienced extrusion specialists is often recommended.
What is the cost of plastic extrusion services? The cost varies based on factors such as material, product complexity, and production volume. Requesting quotes from multiple extrusion providers is advisable.
Plastic extrusion is a versatile and cost-effective method for producing a wide array of plastic products.
The process involves melting plastic and forcing it through a die to create a continuous profile.
Different types of extrusion exist, including sheet/film extrusion, tubing extrusion, and blow film extrusion.
Advantages of plastic extrusion include high volume production, versatility, cost-effectiveness, and design flexibility.
Applications of plastic extrusion span numerous industries, from packaging and construction to automotive and medical devices.
Modern plastic extrusion is increasingly focused on sustainability, incorporating recycled materials and biodegradable polymers.
Remember to consult with experts in Fabrication Services and Machining Services to find the perfect plastic extrusion solution for your specific needs.
Get the latest trends and facts about CNC fabrication from our blog.
Shenzhen Runkey Precision Technology Co. Ltd, a subsidiary of the Tensun Group, is your trusted one-stop solution for custom manufacturing from prototyping to production.Transforming your idea into reality with digital manufacturing resources,streamlined processes, expert guidance,accelerated timelines, and uncompromising quality.
©2024. CNC Fabrication All Rights Reserved.