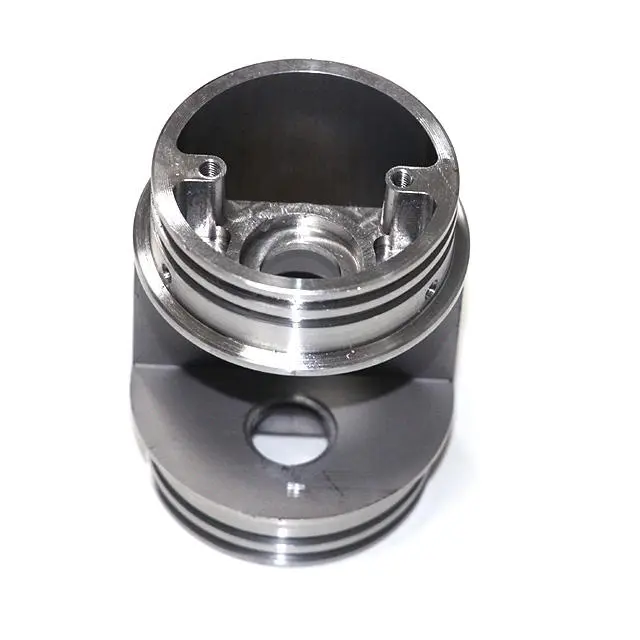
- +8615586668226
- [email protected]
- No. 30, Hongbang Industrial Park, Shenzhen
A CNC punch press is a type of punching machine that uses computer numerical control (CNC) to automate the punching process. It is used to create holes and shapes in sheet metal by applying force with a punch tool. The process involves placing a sheet metal workpiece between a punch and a die. The punch then moves towards the die, removing material from the workpiece to create the desired shape.
I have always been fascinated by the precision and efficiency of CNC punch presses. A CNC punch press operates by using a punch and die set to create holes or shapes in a sheet metal workpiece. The process that uses a CNC program controls the movement of the punch and the positioning of the sheet metal. The machine’s turret holds multiple tools, allowing for a variety of shapes and sizes to be created without manual tool changes. This automation not only speeds up the fabrication process but also ensures high precision and repeatability. In my experience, the use of a CNC punch press significantly reduces setup times and manual labor, making it a cost-effective solution for producing metal parts.
CNC punching machines come in various configurations, including single-station and turret styles. The turret style is particularly versatile as it can hold numerous tools, enabling complex punching operations in a single setup. Punching is a fabrication process where a punching machine applies force to remove material from a sheet metal workpiece to form the desired shape. The punch passes through the sheet metal and into a die, creating a hole or cutout. This method is incredibly efficient for producing parts with multiple holes or intricate patterns.
CNC punching offers numerous advantages in metal fabrication. One of the primary benefits of CNC punching is its precision. CNC machines can create highly accurate holes and shapes, ensuring that the final product meets exact specifications. Another advantage is the speed of the punching process. CNC punch presses can operate much faster than manual methods, increasing productivity and reducing lead times.
In my experience, the versatility of CNC punching is unmatched. These machines can handle a wide range of materials and thicknesses, making them suitable for various fabrication projects. Additionally, CNC punching minimizes material waste compared to other methods, as the process that uses the material more efficiently. The automation of CNC machines also reduces the need for manual labor, lowering labor costs and improving safety in the workplace. In our facility, we’ve found that CNC punching not only enhances the quality of our products but also significantly improves our overall efficiency.
The ability to produce complex shapes and patterns is another significant benefit. CNC punching can create intricate designs that would be difficult or impossible to achieve with manual methods. This capability is particularly valuable in industries like aerospace and electronics, where precision and complexity are paramount. The repeatability of CNC punching ensures consistency across large production runs, which is crucial for maintaining quality standards. Moreover, the flexibility to quickly switch between different tools and programs allows for rapid prototyping and customization, making it a versatile solution for diverse fabrication needs.
CNC punch presses can process a wide variety of metals. Some of the most common types of metal include aluminum, stainless steel, cold-rolled steel, and copper. The ability to handle a wide range of materials is one of the key strengths of CNC punching. Each type of metal has its own unique properties, and CNC punching machines can be adjusted to accommodate these differences.
In my work, I’ve seen firsthand how CNC punching can be used to process various metals with precision and efficiency. For instance, aluminum is a popular choice due to its lightweight and corrosion-resistant properties. Stainless steel, on the other hand, is often used in applications that require high strength and durability. Cold-rolled steel is known for its smooth surface finish, making it ideal for parts that need to be painted or coated. We have successfully used CNC punch presses to fabricate parts from all these materials, demonstrating the versatility of this technology.
Copper is another material that can be effectively processed with a CNC punch press. Its excellent electrical conductivity makes it a common choice for electrical components. CNC punching can create precise holes and shapes in copper sheets, ensuring that the parts meet the required specifications for electrical conductivity and connectivity. The ability to process different types of metal makes CNC punching a valuable tool in various industries, from automotive to electronics. The flexibility to work with different materials allows us to meet the diverse needs of our clients, whether they require parts made from aluminum, stainless steel, copper, or other metals.
When comparing CNC punching to other fabrication techniques such as laser cutting, it’s essential to consider the specific requirements of the project. Laser cutting uses a focused laser beam to cut through the sheet metal. While laser cutting is excellent for creating intricate designs and smooth edges, it can be slower and more expensive than CNC punching for simpler shapes and holes.
In my experience, CNC punching is often the preferred method for projects that require a large number of holes or repetitive shapes. The speed and efficiency of CNC punch presses make them ideal for high-volume production runs. Laser cutting, on the other hand, may be more suitable for projects that require complex geometries and fine details. CNC punching is more efficient for projects requiring numerous holes or shapes in sheet metal. It is also more economical for thicker materials, as laser cutting can be slower and more costly in such cases. Laser cutting, however, excels in creating complex shapes and fine details with high precision.
Another fabrication technique to consider is press brake forming. Press brakes are used to bend sheet metal into various shapes. While press brakes are excellent for forming, they do not have the same capability as CNC punching when it comes to creating holes and complex shapes. CNC punching can perform both punching and basic forming operations, making it a more versatile option in many cases. Each method has its strengths, and the choice depends on the specific needs of the project. For tasks that require both forming and punching, a combination of CNC punching and press brake operations often provides the best results.
There are several types of CNC machines used in sheet metal punching. The most common type is the turret punch press, which features a turret that holds multiple tools. This allows for quick tool changes and enables the machine to perform a variety of punching operations without manual intervention.
Another type of CNC machine used in sheet metal punching is the single-station punch press. This type of machine has a single punch and die set and is typically used for simpler operations. While single-station machines may not offer the same versatility as turret punch presses, they can be more cost-effective for specific applications. The choice between a turret and a single-station machine often depends on the complexity and volume of the work.
In addition to punch presses, other CNC machines like CNC plasma cutters and CNC waterjet machines are used in metal fabrication. CNC plasma cutters use a plasma torch to cut through sheet metal, while CNC waterjet machines use a high-pressure stream of water mixed with an abrasive substance. These machines are often used for cutting thicker materials or creating complex shapes that may not be feasible with punching. Plasma cutting is effective for thick metals but leaves a wider kerf and heat-affected zone, while waterjet cutting provides a cold cutting process with no heat-affected zone, suitable for materials sensitive to heat. At our fabrication facilities, we utilize a range of CNC machines, including turret punch presses, laser cutters, and press brakes, to offer comprehensive solutions for our clients.
Automation plays a crucial role in CNC punch press operations. By using computer numerical control (CNC), the punching process can be fully automated, reducing the need for manual labor and increasing efficiency. CNC programs control the movement of the punch and the positioning of the sheet metal, ensuring precision and repeatability.
In my experience, automation not only speeds up the fabrication process but also improves the quality of the final product. CNC machines can operate 24/7 with minimal supervision, significantly increasing productivity. The use of automation also reduces the risk of human error, ensuring that each part is produced to the exact specifications. The integration of automated loading and unloading systems further enhances efficiency by streamlining material handling.
Moreover, automation allows for greater flexibility in production. CNC programs can be easily modified to accommodate different designs and materials, making it possible to switch between tasks quickly. This flexibility is particularly valuable in today’s fast-paced manufacturing environment, where quick turnaround times are often essential. By leveraging automation, we can meet the demands of our clients more effectively and maintain a competitive edge in the market. Automation also allows for remote monitoring and control, enabling real-time adjustments and reducing downtime.
Precision is crucial in CNC sheet metal punching because it directly impacts the quality and functionality of the final product. In many industries, such as aerospace, automotive, and medical devices, components must meet strict tolerances to ensure proper fit and performance. Precision punching ensures that holes and shapes are created to the exact dimensions specified in the design.
CNC technology enables high precision by using computer-controlled movements. The CNC program guides the punch tool with extreme accuracy, resulting in consistent and precise results. Additionally, the use of high-quality tools and dies further enhances precision. Regular maintenance and calibration of the punching machine are also essential to maintain accuracy over time. Our commitment to precision has allowed us to deliver high-quality components that meet the stringent requirements of our clients in various industries.
In my experience, achieving precision in CNC punching also involves careful planning and attention to detail. Factors such as material thickness, tool selection, and punching speed can all impact the accuracy of the results. By optimizing these parameters and using advanced CNC technology, we can achieve the highest levels of precision in our fabrication processes. The use of sensors and feedback systems in modern CNC machines further enhances accuracy by providing real-time monitoring and adjustments during the punching process.
CNC punching is used in a wide range of industries to create various components and products. In the automotive industry, CNC punching is used to produce parts such as brackets, panels, and enclosures. The precision and efficiency of CNC punching make it an ideal choice for manufacturing high-quality automotive components.
The aerospace industry also relies heavily on CNC punching. Components for aircraft, such as fuselage panels and structural parts, require high precision and durability. CNC punching can create complex shapes and precise holes in materials like aluminum and titanium, which are commonly used in aerospace applications. The ability to produce lightweight yet strong components is crucial in this industry.
In the electronics industry, CNC punching is used to manufacture enclosures, panels, and other components for electronic devices. The precision of CNC punching ensures that parts fit together perfectly, which is essential for the proper functioning of electronic equipment. Additionally, CNC punching can create ventilation holes and other features that help dissipate heat and improve the performance of electronic devices. Our expertise in CNC punching has enabled us to support clients in these and many other industries, delivering customized solutions that meet their specific needs.
Determining whether CNC punching is the right choice for a business’s fabrication needs involves evaluating several factors. One of the primary considerations is the type of material being used. CNC punching is ideal for sheet metal, including aluminum, stainless steel, and copper. If the project involves these materials, CNC punching is likely a suitable option.
Another factor to consider is the complexity of the design. CNC punching excels at creating precise holes and shapes, making it ideal for parts with intricate patterns or multiple holes. If the design requires high precision and repeatability, CNC punching is an excellent choice. In my experience, businesses that require large quantities of parts with consistent quality find CNC punching to be the most cost-effective solution. The volume of production is also an important consideration. CNC punching is highly efficient for high-volume production runs, thanks to its speed and automation capabilities.
Additionally, businesses should evaluate their budget and timeline. CNC punching can reduce labor costs and shorten lead times, making it a cost-effective option for many projects. By carefully assessing these factors, businesses can determine whether CNC punching aligns with their fabrication needs and goals. Our team is always available to consult with clients and help them make informed decisions about their fabrication processes. We also need to consider factors such as the required tolerances, the need for secondary operations, and the overall cost of production.
The future of CNC punching in the metal fabrication industry looks promising. Advances in CNC technology are continually pushing the boundaries of what is possible, leading to even greater precision, efficiency, and versatility. One trend that I believe will shape the future of CNC punching is the integration of artificial intelligence (AI) and machine learning.
AI-powered CNC machines can optimize punching operations in real time, adjusting parameters such as punching speed and tool selection to achieve the best results. Machine learning algorithms can analyze data from past projects to identify patterns and improve future performance. This level of intelligence will enable CNC punching to become even more efficient and adaptable. I am particularly excited about the potential of AI to revolutionize CNC punching. By leveraging AI, we can achieve levels of precision and efficiency that were previously unimaginable.
Another trend is the increasing use of advanced materials in metal fabrication. As industries demand lighter, stronger, and more durable components, fabricators are turning to materials like high-strength steel, titanium, and composites. CNC punching technology is evolving to meet these challenges, with new tools and techniques being developed to process these advanced materials effectively. The continued development of CNC technology will ensure that punching remains a vital part of the metal fabrication industry for years to come. The use of robotics for material handling and automation of the entire fabrication process is also expected to grow, further enhancing productivity and reducing costs.
FAQs
What is a CNC punch press?
A CNC punch press is a machine that uses computer numerical control (CNC) to automate the punching process, creating holes and shapes in sheet metal with high precision.
What are the advantages of using CNC punching in metal fabrication?
The advantages of CNC punching include high precision, speed, versatility in handling various materials, reduced material waste, and lower labor costs due to automation.
How does CNC punching compare to laser cutting?
CNC punching is generally faster and more efficient for creating numerous holes and simple shapes, while laser cutting is better suited for intricate designs and smooth edges, albeit at a higher cost.
What types of metals can be processed with a CNC punch press?
CNC punch presses can process a wide range of metals, including aluminum, stainless steel, cold-rolled steel, and copper.
What industries commonly use CNC punching?
CNC punching is used in various industries, including automotive, aerospace, electronics, and medical devices, to produce a wide range of components and products.
How can I determine if CNC punching is right for my fabrication needs?
Consider factors such as the type of material, design complexity, production volume, budget, and timeline to determine if CNC punching is the right choice for your fabrication needs.
Here are the most important things to remember about CNC punching in metal fabrication:
CNC punching offers unparalleled precision and efficiency in creating holes and shapes in sheet metal.
The technology is highly versatile, capable of processing a wide range of materials and accommodating complex designs.
Automation plays a crucial role in CNC punching, reducing labor costs, increasing productivity, and improving safety.
CNC punching is used across various industries, including automotive, aerospace, electronics, and medical devices.
Advances in technology, such as AI and machine learning, are set to revolutionize CNC punching further, pushing the boundaries of what is possible in metal fabrication.
Determining the right fabrication method involves evaluating factors such as material type, design complexity, production volume, budget, and timeline.
By understanding and leveraging the capabilities of CNC punching, businesses can enhance their fabrication processes, improve product quality, and maintain a competitive edge in the market. If you have any questions or would like to discuss your specific fabrication needs, please do not hesitate to contact us. Our expertise in CNC punching and commitment to innovation make us a trusted partner for clients across various industries. We look forward to helping you achieve your fabrication goals with our advanced CNC solutions. Whether you need precision machining, sheet metal fabrication, or rapid prototyping, our team is here to support you every step of the way.
Get the latest trends and facts about CNC fabrication from our blog.
Shenzhen Runkey Precision Technology Co. Ltd, a subsidiary of the Tensun Group, is your trusted one-stop solution for custom manufacturing from prototyping to production.Transforming your idea into reality with digital manufacturing resources,streamlined processes, expert guidance,accelerated timelines, and uncompromising quality.
©2024. CNC Fabrication All Rights Reserved.