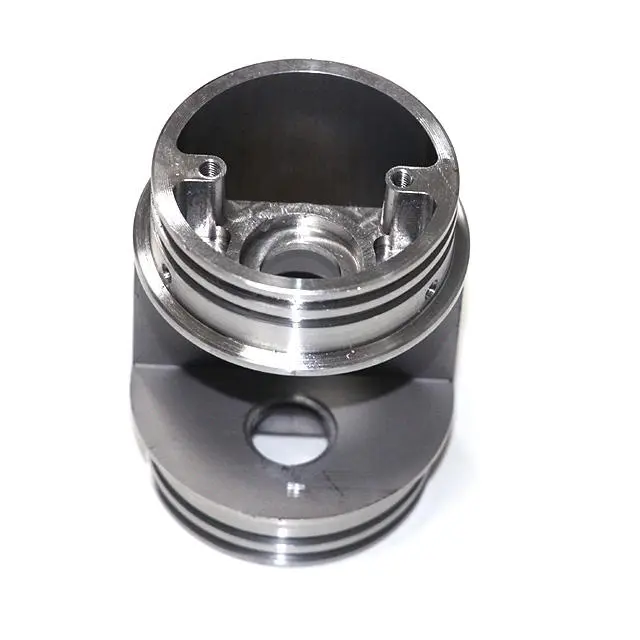
- +8615586668226
- [email protected]
- No. 30, Hongbang Industrial Park, Shenzhen
Anodizing is an electrochemical process that increases the thickness of the natural oxide layer on the surface of the aluminum. This coating, primarily aluminum oxide, enhances the metal’s properties, making it more resistant to corrosion, wear, and abrasion. Why anodize aluminum specifically? Because untreated aluminum, while lightweight and versatile, is susceptible to these damaging factors. Anodizing transforms it into a more robust material suitable for demanding applications.
Anodizing isn’t just about protection. It also improves the aluminum part’s aesthetic qualities. The anodized coating can be dyed in a wide range of colors, opening up design possibilities for various products. This combination of enhanced durability and aesthetic versatility is why anodizing is such a popular metal finishing process.
The anodizing process involves submerging the aluminum part in an electrolytic solution, typically sulfuric acid. A current is then passed through the solution, using the aluminum part as the anode. This process converts the aluminum surface into a layer of aluminum oxide. This oxide layer is integral to the aluminum substrate and is much harder and more durable than the original aluminum surface.
The thickness of the anodized layer can be controlled by adjusting the current and time of the anodizing process. A thicker anodized layer provides greater corrosion resistance and wear resistance. The process is precisely controlled to achieve the desired properties in the finished anodized part. This level of control is a key advantage of the anodizing process.
Anodizing offers a multitude of benefits, making it a preferred choice for various applications. It significantly enhances corrosion resistance, protecting the aluminum from environmental factors. The hardness of the anodized coating improves wear and abrasion resistance, increasing the lifespan of the aluminum component.
Furthermore, anodizing improves the adhesion of paints and other coatings to the aluminum surface. This is because the porous nature of the anodized layer provides a better mechanical bond. The process also enhances the aesthetic appeal of aluminum, allowing for a wide range of color options through the use of dyes. This is particularly useful in applications like Consumer Products, where visual appeal is critical.
There are different types of anodizing, each suited for specific needs:
Type I Anodizing (Chromic Acid Anodizing): Produces a thin, decorative coating ideal for parts that require a good base for paint or adhesive.
Type II Anodizing (Sulfuric Acid Anodizing): The most common type, offering a good balance of corrosion resistance, wear resistance, and the ability to accept dyes. This is frequently used in Industrial Equipment.
Type III Hard Anodizing (Hard Coat Anodizing): Creates an extremely hard, wear-resistant coating, suitable for applications requiring exceptional durability, such as in the Aerospace industry.
While technically possible, anodizing aluminum at home comes with challenges. It requires specific chemicals like sulfuric acid, proper safety precautions, and careful control of the process. For optimal results and safety, it’s recommended to work with professional CNC Solutions providers experienced in Metal Bending and other fabrication services who offer anodizing services.
Choosing the right type of anodizing depends on the specific application. Factors to consider include the desired level of corrosion resistance, wear resistance, thickness of the coating, and whether dyeing is required. Consulting with experts in Machining Services can help you determine the most appropriate anodizing process for your needs.
Before anodizing aluminum parts, consider the alloy being used, as different alloys react differently to the process. The surface finish of the aluminum prior to anodizing also affects the final result. Proper cleaning and pretreatment are crucial for achieving a uniform and high-quality anodized coating.
Anodized aluminum is critical across numerous industries, including:
Aerospace and Aviation: For lightweight, corrosion-resistant components.
Automotive: For wheels, trim, and other parts.
Electronics: For enclosures and heat sinks.
Medical Devices: For instruments and implants.
Is anodized aluminum conductive? No, the anodized coating is an insulator.
Can anodized aluminum be scratched? While very durable, the coating can be scratched with sufficient force.
How thick is the anodized layer? Thickness varies depending on the type of anodizing, typically ranging from a few micrometers to several tens of micrometers.
Anodizing is an essential process for enhancing the properties and performance of aluminum. Its versatility and wide range of benefits make it a valuable asset across diverse industries, from aerospace to consumer products. By understanding the process and its various applications, you can leverage the power of anodizing to improve the durability, aesthetics, and overall quality of your aluminum products.
Key Takeaways:
Anodizing enhances aluminum’s corrosion and wear resistance.
Different types of anodizing cater to specific application needs.
Choosing the right type of anodizing involves considering factors like corrosion resistance, wear resistance, and desired coating thickness.
Professional anodizing services ensure optimal results and safety.
Anodized aluminum is crucial in industries such as aerospace, automotive, electronics, and medical devices.
Get the latest trends and facts about CNC fabrication from our blog.
Shenzhen Runkey Precision Technology Co. Ltd, a subsidiary of the Tensun Group, is your trusted one-stop solution for custom manufacturing from prototyping to production.Transforming your idea into reality with digital manufacturing resources,streamlined processes, expert guidance,accelerated timelines, and uncompromising quality.
©2024. CNC Fabrication All Rights Reserved.