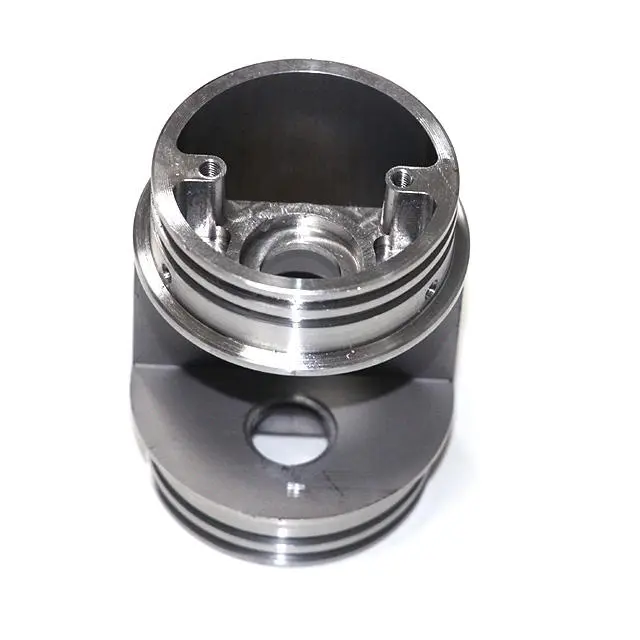
- +8615586668226
- [email protected]
- No. 30, Hongbang Industrial Park, Shenzhen
A bevel refers to an angled surface that meets two other surfaces at an angle other than 90 degrees. It’s essentially a sloping edge, created by removing material from the edge of a workpiece. Think of the angled edge of a picture frame or the slanted edge of a countertop – these are everyday examples of bevels. Beveling is the process of creating this angled surface.
Bevels are ubiquitous in various industries, from construction and furniture making to aerospace and automotive manufacturing. They serve both functional and aesthetic purposes, enhancing strength, improving weldability, and adding visual appeal. The angle of a bevel is crucial and is determined by the specific application.
Several types of bevels exist, each designed for a particular purpose. Some common types include:
Plain Bevel: A single angled surface.
Double Bevel: Two angled surfaces meeting at a point.
Compound Bevel: A combination of two or more angles on a single edge.
J-Prep Bevel: A curved bevel often used for welding.
J-Prep with Back Bevel: A J-prep with an additional angle at the root.
Back Bevel: An angled surface on the back side of a weld joint.
V Bevel: Two angled surfaces forming a V shape.
Understanding the different types of bevels is crucial for selecting the appropriate one for a specific application. The choice depends on factors such as the material being worked with, the desired strength of the joint, and the welding process used.
Bevels offer numerous advantages in engineering design, contributing to both structural integrity and aesthetic appeal:
Stress Reduction: Bevels reduce stress concentration at sharp corners, preventing cracks and fractures. This is particularly important in load-bearing applications.
Improved Weldability: Beveling the edges of metal before welding creates a larger surface area for the weld, allowing for better weld penetration and a stronger weld joint.
Enhanced Appearance: Bevels can soften sharp edges, adding a touch of elegance and improving the visual appeal of a product.
In applications like CNC Machining, beveling is crucial for part functionality and aesthetics.
Bevels are used across a wide range of engineering applications, including:
Welding Applications: Bevels are essential for preparing metal parts for welding, ensuring strong and reliable joints. The bevel angle and type of bevel are carefully selected to maximize weld strength and quality of the weld.
Machining: Bevels are often incorporated into machined parts to reduce stress concentrations, improve fit, and enhance aesthetics. Precision Machining often utilizes bevels for complex parts.
Construction: Bevels are used in structural elements, such as beams and columns, to distribute loads and prevent stress buildup.
Bevels can be created using various machines, including:
CNC Machines: CNC Milling and CNC Turning can create precise and complex bevels.
Grinders: Angle grinders and specialized beveling machines can be used to create bevels on metal parts.
Dedicated Beveling Machines: These machines are designed specifically for creating bevels, offering high speed and precision.
The choice of machine depends on the material, the required accuracy, and the volume of production. Understanding the capabilities of different machines is crucial for achieving optimal bevel quality.
Choosing the right beveling method depends on several factors, including the material thickness, the desired bevel angle, and the available equipment. A bevel protractor is essential for measuring bevel angles accurately.
Material Thickness: Thicker materials may require specialized equipment like a 5 Axis CNC Machining center for complex bevel cuts.
Bevel Angle: The desired angle will influence the tooling and techniques used.
Accessibility: The location of the bevel on the workpiece can limit the available methods.
Consulting with experienced machinists or welders can help determine the most appropriate beveling techniques for a specific application.
Beveling is crucial in welding applications. It allows for proper weld penetration and ensures a strong, durable joint. The beveling process must be carefully controlled to achieve optimal results.
Filler Material: The type and amount of filler material used in welding are influenced by the bevel geometry.
Welding Process: Different welding processes, such as MIG, TIG, and stick welding, may require specific bevel preparations.
Joint Design: The design of the weld joint, including the type of bevel, plays a critical role in the overall strength and structural integrity of the weld.
Pipe beveling presents unique challenges and requires specialized equipment and techniques. Accuracy is paramount to ensure proper alignment and a strong weld.
Beveling Machines: Dedicated pipe beveling machines are often used to create precise bevels on pipes of various diameters.
Internal and External Bevels: Pipe beveling can involve creating bevels on both the internal and external surfaces of the pipe.
Accurate measurement of bevel angles is essential for achieving the desired results. A universal vernier bevel protractor is a common tool used for this purpose.
Bevel Protractor: This tool allows for precise measurement of angles on various surfaces.
Digital Bevel Gauges: Digital gauges provide quick and accurate readings, especially for complex bevel geometries.
Understanding how to use these tools correctly is crucial for maintaining bevel quality and ensuring proper bevel edge preparation.

alt: Example of a beveled edge
Various bevel designs are employed in engineering and manufacturing, each serving a specific function:
Single Bevel: Used for creating a sloped edge on a single surface. Commonly used in welding.
Double Bevel: Used for creating a pointed edge by beveling two surfaces. Provides greater strength in welding applications.
What is the purpose of beveling?
Beveling primarily enhances weld penetration and reduces stress concentrations in materials.
What are the common bevel angles used in welding?
Common bevel angles vary, but 30, 37.5, and 45 degrees are frequently used.
What tools are used for beveling?
Various tools are employed, ranging from hand grinders and specialized beveling machines to CNC machines.
How do I measure a bevel angle?
A bevel protractor or a digital bevel gauge are commonly used to measure bevel angles.
What is the difference between a bevel and a chamfer?
While both modify edges, a bevel is an angled surface, whereas a chamfer typically removes a small 45-degree edge. You can learn more about CNC machining and fabrication at our Fabrication Services page.
How important is beveling in CNC machining?
Beveling in CNC Solutions is crucial for part functionality, safety, and aesthetics, especially when dealing with metals and intricate designs.
Beveling is a fundamental process in engineering and manufacturing, impacting both functionality and aesthetics.
Understanding the different types of bevels is crucial for choosing the right one for a specific application.
Proper bevel edge preparation is essential for achieving strong and reliable welds.
Accurate measurement of bevel angles is critical for maintaining quality and precision.
Choosing the right beveling machine and technique depends on various factors, including the material, bevel angle, and accessibility.
Consider exploring more information on specific industries like Aerospace or Automotive to see how beveling plays a role in their manufacturing processes.
Get the latest trends and facts about CNC fabrication from our blog.
Shenzhen Runkey Precision Technology Co. Ltd, a subsidiary of the Tensun Group, is your trusted one-stop solution for custom manufacturing from prototyping to production.Transforming your idea into reality with digital manufacturing resources,streamlined processes, expert guidance,accelerated timelines, and uncompromising quality.
©2024. CNC Fabrication All Rights Reserved.