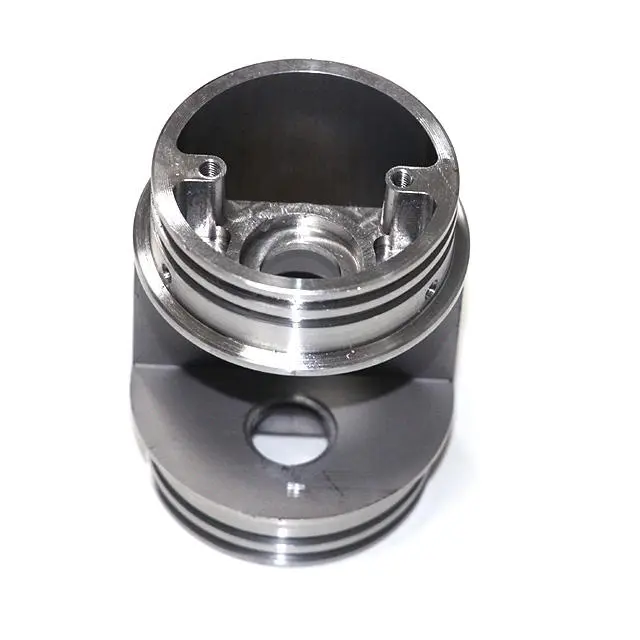
- +8615586668226
- [email protected]
- No. 30, Hongbang Industrial Park, Shenzhen
A bevel refers to an angled edge or surface created on a material. It is a cut that is not perpendicular to the main surfaces of the object, typically forming an angle other than 90 degrees. In engineering and manufacturing, the bevel is often employed to prepare edges for welding, improve assembly, and even enhance the aesthetic appearance of the final product. The bevel angle is crucial in achieving the desired outcome, and the choice of the correct type of bevel can significantly impact the performance and longevity of the product. A bevel is essential for ensuring strong, reliable joints, particularly in applications where structural integrity is paramount.
Beveling is more than just a cosmetic step. It plays a crucial role in distributing forces and reducing stress concentrations in the material, especially around joints and edges. The beveled edge helps to smoothly transition between two surfaces, which reduces the chances of failure due to excessive stress. In many manufacturing processes, a well-executed bevel can enhance the overall quality and durability of the final product, ensuring that it meets the required performance standards.
A chamfer is similar to a bevel but typically refers to a smaller angled edge. While a bevel often extends across the entire thickness of a material, a chamfer is usually much smaller and is often cut at a 45 degrees angle. The primary purpose of a chamfer is to remove a sharp edge or corner, making a part safer to handle and often more aesthetic. For example, on consumer products, a chamfer might be used to soften the edges of a plastic part, whereas on machine components, it helps prevent chipping and makes assembly easier. The chamfer also plays a role in reduce stress concentrations, even if it is on a smaller scale than a bevel.
The key difference between a bevel and chamfer is the size and extent of the angled cut. A bevel is more significant and often part of a structural or mechanical preparation, while a chamfer is generally a smaller, finishing touch to improve safety and handling. The chamfer is an angled edge, usually at 45 degrees. While both are angled cuts, a bevel is usually larger, and a chamfer is smaller and more common on edges. Both are commonly used in design and manufacturing. The decision between using a bevel and chamfer depends on the specific requirements of the application.
There are several different types of bevels used in manufacturing, each designed for specific applications and requirements. A plain bevel is a simple angled cut on the edge of a material, which is often used for welding preparation. The v bevel is formed by making two plain bevel cuts on two pieces of material that are to be joined, creating a V-shaped groove for welding. Another common type is the j-prep bevel, which provides a greater surface area for welding. J-prep with a back bevel, this is a more specialized cut where the material is prepared with a J-shaped curve, in addition with the back cut for more secure connections. The compound bevel, which combines several bevel angles to achieve more complex bevel designs. This is also referred to as a double bevel, which is used for situations where there is a need to access both sides of the structure or to create very secure welding. Understanding the type of bevel required is essential for successful and efficient manufacturing process.
The selection of the appropriate bevel is often determined by factors like the material being used, the type of weld required, and the structural demands of the application. For example, a j-prep bevel provides a larger surface area for welding, which can be beneficial for stronger welds in thicker materials. On the other hand, a plain bevel may suffice for thinner materials where less weld penetration is needed. The various bevel designs also allow for flexibility in weld preparation, making it possible to customize the joint to specific needs and improving the overall efficiency of the manufacturing process.
Bevels in engineering design are not merely added for aesthetic purposes but are an integral part of the functionality and structural integrity of a product. The choice of bevel angle and type of bevel directly affects how well the materials will join and how the structure will handle stress and loads. Engineers must consider the stress concentration around the joints, particularly in critical applications such as aerospace, automotive, and heavy machinery, and how the use of bevels can reduce stress. A properly designed bevel can improve the longevity and reliability of a product by preventing failures at vulnerable points.
Bevels in engineering design also address the functional and aesthetic aspects of a product. In many cases, they are designed to create seamless joints and provide visual appeal, which can be essential for consumer acceptance. Engineering design must consider how the various parts will fit together during assembly. Using a proper bevel can facilitate assembly by providing clearance and alignment guidance during the assembly.
Several types of machines can be used for beveling, depending on the material, size, and complexity of the part. One of the most common types is a beveling machine, which is designed specifically to produce accurate and consistent bevels. A cutting tool is used to create the angled cut. In the case of metalwork, this might include various types of milling, grinding and cutting machinery. For pipe beveling, dedicated machines are available that can prepare the ends of pipes for welding with great precision. These machines often use rotary or planetary cutters to achieve the desired bevel angle. The choice of machine will significantly impact the bevel quality, speed, and overall efficiency of the beveling process.
In modern manufacturing industry, CNC machines play a vital role in beveling. These machines can be programmed to create complex bevel designs with high precision and repeatability, making them suitable for both mass production and custom projects. CNC milling machines, laser cutting machines and lathes can all be used to create a bevel. The use of cnc machines in beveling not only increases accuracy but also reduces material waste, enhancing the overall efficiency of the manufacturing process. CNC allows for the creation of a wide range of bevels, including the more complex compound bevel and j-prep with a back bevel, achieving the highest bevel quality.
The core difference between a bevel and chamfer lies in their purpose and extent. A bevel is typically a larger, angled cut used to prepare edges for welding or other joining methods. The bevel aims to maximize the connection area and provide better weld penetration, ensuring the structural integrity of the joint. In contrast, a chamfer is a smaller angled cut, most often at 45 degrees. The chamfer’s primary purpose is to soften sharp corners and edges, making parts safer to handle and aesthetically pleasing.
While both bevel and chamfer are angled edges, the bevel is focused on structural needs, particularly for welding, and the chamfer is more focused on safety and appearance. It’s also worth noting that a bevel is generally larger than a chamfer and the angle of the bevel will vary greatly based on use case. The decision on using either a bevel or chamfer is driven by the specific goals of the design. So, while a bevel would provide additional surface area for welding, a chamfer would soften sharp edge for ease of use or handling. So while both are angled bevel surfaces, the extent and the reasoning behind them is different.
Bevels are found in numerous engineering applications across various industries. One of the most commonly used applications is in welding, where bevel edge preparation allows for better weld penetration and a stronger joint. Bevels are vital in the construction of pipelines and industrial structures, especially in pipe beveling, where the pipes need to be joined with strong, reliable weld joints. Also, for metal bevel gears, bevels are necessary to ensure proper engagement and efficient power transfer. These are just some of many engineering applications for beveling.
In mechanical engineering, bevels are often used to provide clearance between mating parts, facilitating assembly and reducing stress concentrations. They are also used in the creation of certain types of gears, where the bevel angle directly affects the gear’s performance. The use of a bevel helps in reducing stress and also improves the overall durability and reliability of the parts. Also the ability to reduce stress concentrations through the use of a bevel makes them an essential component in complex and high-performance components.
Bevels in engineering design are essential for a number of reasons. They not only improve the strength of welded joints but also enhance the overall functionality and aesthetic appeal of a product. Bevels facilitate the assembly of complex parts by aligning them correctly, saving time and effort. By reducing stress concentrations at edges and corners, bevels help to prevent fatigue and failure, extending the lifespan of the components. The proper use of bevels contributes to more efficient designs that perform better over longer periods.
The strategic application of bevels can often be used to save on material costs and manufacturing time. A well-planned bevel design can allow for tighter and stronger joints. They can also provide an enhanced aesthetic appeal. The ability of bevels to improve structural integrity and ease of manufacture makes them a cornerstone of effective engineering design. In short, without proper bevel design, many engineering projects would be much harder to achieve. The use of the appropriate bevel helps greatly in the engineering process.
The advantages of using bevels and chamfers are numerous. Bevels increase the surface area for welding, which results in stronger and more reliable weld joints, improving the structural integrity of the finished item. Bevels also assist in the alignment of parts. In addition, bevels can help to distribute the forces and loads, therefore, reducing stress concentrations. Meanwhile, chamfers provide a safer way of handling components. They soften sharp corners and edges, reducing the risk of injury. Chamfers also enhance the aesthetic look of a part, providing a more refined and professional finish.
Both bevels and chamfers contribute to more efficient and robust product design. A well-placed bevel can significantly enhance the reliability of a welded structure. A chamfer improves the handling of any part with sharp edges. Both techniques offer significant benefits across a wide range of applications. Ultimately, the strategic use of bevels and chamfers leads to better-performing, safer, and more visually appealing products.
CNC machines play a pivotal role in ensuring precision beveling in modern engineering and manufacturing. These computer-controlled machines can execute complex bevel designs with high accuracy and repeatability. The use of cnc machines in beveling allows for very specific bevel angles and shapes to be created, which is vital for applications that require tight tolerances. The cutting tool on a CNC machine can be precisely controlled, resulting in consistent bevel quality across all parts.
CNC technology also makes the creation of complex compound bevels much easier and faster. The ability to program the CNC machine to create the required bevel greatly reduces manual effort and the potential for human error. Using CNC makes the beveling process more efficient and cost-effective, especially for large-scale production. The use of cnc machines allows the beveling techniques to be precise and reliable every single time.
Pipe beveling is a critical step in preparing pipes for welding. The bevel on the pipe’s edge ensures a proper fit between the two faces and provides adequate space for the weld material to penetrate. This step is vital for the integrity of the pipeline. A well-executed bevel promotes a strong weld joint, which is vital for the prevention of leaks and structural failures. Correct pipe beveling is a cornerstone of high-quality pipe fabrication, whether they are for water distribution, oil and gas, or structural applications.
Beveling also helps in ensuring consistency and reliability in pipe joints. By preparing the edges of the pipe correctly, it allows for uniform weld penetration and reduces the risk of defects. In many cases, automated pipe beveling systems are used for the highest consistency and efficiency. The use of automated beveling also allows for a faster production time and better resource allocation. Without beveling, pipe connections are much more likely to fail.
The most effective beveling method varies depending on the material being worked on. For metals, machining processes like milling and grinding are commonly used. Cutting tool can be chosen to suit the material, with high-speed steel or carbide often used for metals. For plastics, beveling might involve using rotary cutters or heated blades to prevent cracking and melting. The selection of the appropriate beveling method for each material is critical for ensuring bevel quality and accuracy. It is also important to consider how the material will react to heat and pressure.
For harder materials, like hardened steel, beveling may require specialized machines and techniques. This might include using abrasive water jets, which can cut through the material without generating excessive heat. The choice of the right beveling method is also influenced by the complexity of the desired bevel designs. For simple plain bevels, manual methods might suffice. But for more complex compound bevels or j-prep bevels, more sophisticated equipment is needed. Understanding the properties of the material and the requirements of the final product is the key for choosing the right method.
There are many different bevel designs used in practice. Plain bevels, the simplest type, are characterized by a single angled cut and are often used for thinner materials or basic weld joints. V bevels, are a more complex design that creates a V-shaped gap. The v bevel provides greater depth for welding, which ensures more secure connection. J-prep bevels are used where more space for weld material is required. In some cases a j-prep with a back bevel are needed. The compound bevel, also known as a double bevel, involves a more complex set of angles.
The choice of bevel designs depends on the materials being joined and the structural integrity needed for the final product. For example, the use of a j-prep with a back bevel is typically used in very high structural integrity welding. The versatility of bevel designs makes it possible to adapt to different welding applications. The ability to choose from many different types of bevels allows for optimizing the joints to the specific needs of the project.
Determining the right beveling method for your project involves careful consideration of several factors. Firstly, the material being worked with is a key consideration. Different materials require different cutting techniques to get a proper bevel cut. Secondly, the complexity of the required bevel designs is important. Simple plain bevels might be easily achieved with less sophisticated equipment. But for more complex compound bevel or j-prep bevels, a CNC is essential. Also, the overall scale of the production also affects method choice. For smaller runs, manual beveling may suffice, but for larger runs, automated beveling machines are recommended.
Furthermore, the required bevel angle, quality of the finish, and tolerance are other major considerations. The choice of the appropriate bevel should ensure the highest quality and reliability of the weld joint. In some cases, the universal vernier bevel protractor may be needed for measuring bevel angles. Selecting the correct beveling technique requires not just knowledge but also a clear understanding of the goals for the project. Understanding all factors will help ensure that the selected method achieves the desired outcome effectively and efficiently.
What is the angle of a bevel?
The angle of a bevel can vary depending on its purpose, but it is typically between 15 and 75 degrees.
How does beveling help improve weld quality?
Beveling increases the surface area for welding, allowing for deeper weld penetration, which results in a stronger and more reliable joint.
Is a bevel used only in welding?
No, bevels are also used to reduce stress concentrations at sharp edges, and for aesthetic purposes as well as to prepare edges for joining of any kind.
Can bevels be achieved on a CNC machine?
Yes, CNC machines are capable of producing accurate and complex bevel designs on multiple materials.
What is the main purpose of a chamfer in engineering applications?
The primary purpose of a chamfer is to soften sharp corners and edges, enhancing safety and providing a more refined finish.
When should I use a j-prep bevel instead of a plain bevel?
You should use a j-prep bevel when a larger surface area for welding is required, particularly in thicker materials or high-stress applications.
For all your CNC machining needs, including precision beveling and chamfering, consider reaching out to us at CNC Fabrication. We offer a wide range of services including, CNC Machining, Fabrication Services, Rapid Prototyping, Laser Cutting, Precision Machining and Surface Finishing. Let us help you bring your designs to life with quality and precision.
Get the latest trends and facts about CNC fabrication from our blog.
Shenzhen Runkey Precision Technology Co. Ltd, a subsidiary of the Tensun Group, is your trusted one-stop solution for custom manufacturing from prototyping to production.Transforming your idea into reality with digital manufacturing resources,streamlined processes, expert guidance,accelerated timelines, and uncompromising quality.
©2024. CNC Fabrication All Rights Reserved.