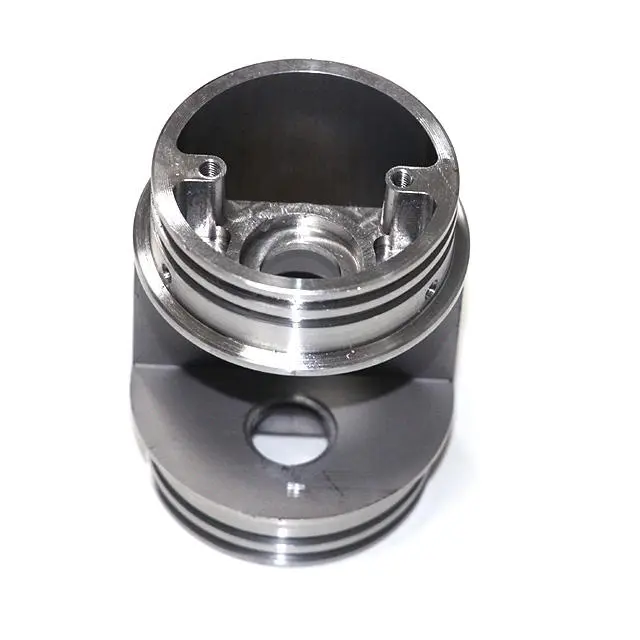
- +8615586668226
- [email protected]
- No. 30, Hongbang Industrial Park, Shenzhen
A bevel is an angled edge created between two faces of a material. This angled cut, often used in mechanical engineering, isn’t just for aesthetic purposes; it serves several functional roles. Imagine the corner of a table—if that corner were sliced off at an angle, that would be a simple bevel. A bevel edge is different from a sharp edge which is often fragile and dangerous. The term bevel refers to an angled edge, typically created on a part or material to create a more functional or aesthetic transition.
Think of it this way: when we are talking about a bevel we are describing a deliberate bevel cut made during the manufacturing process, often to prepare edges for welding or to reduce stress on a component. Unlike a sharp corner, a beveled edge is less prone to chipping, and in some cases, it provides a better surface for painting or adhesion. Bevels are often used when connecting two or more parts together.
While the terms bevel and chamfer are often used interchangeably, there are subtle but important differences. A chamfer is an angled cut, much like a bevel, but it typically refers to an edge that has been angled at 45 degrees. It is a transitional edge between two faces that is more often used for finishing or removing sharp corners. On the other hand, a bevel is an angled edge that can be any angle, not just 45 degrees and serves more functional and structural purposes.
To understand the difference between bevel and chamfer, think of it this way: both aim to reduce the sharp edge on a part. A chamfer is an angled cut or a simple angled edge, generally smaller and used for finishing. However, a bevel is often a larger bevel edge and designed for functional purposes such as weld preparation or reducing stress. While a chamfer is an angled cut, a bevel is often designed with a specific bevel angle to accomplish a specific purpose. The difference between the two is mostly in purpose. Both serve a valuable purpose in design and manufacturing.
There are several different types of bevels, each with its unique characteristics and applications. Here are a few common types:
These various types illustrate the versatility and importance of bevels in engineering design and welding applications. At CNC Fabrication, we understand that the proper type of bevel needs careful consideration of its intended purpose, material, and application.
While not a type of bevel, a fillet is a related feature often used in engineering design. A fillet is a curved internal corner, designed to reduce stress concentrations in parts. Unlike a bevel, which is an angled cut, a fillet is a curve. But, both these elements are designed to improve the strength and longevity of a part.
Fillets are essential in areas prone to stress, they help distribute forces evenly, thereby enhancing the structural integrity of a component. Just as a bevel modifies an edge, a fillet strengthens a corner, providing both functional and aesthetic benefits. Often you find fillets next to bevels, for instance a j-prep can also use a fillet to add even more strength.
The bevel angle is not just about aesthetic purposes; it plays a crucial role in the structural integrity of a component. The angle of a bevel can influence how stresses are distributed within a material. A poorly designed bevel or bevel angle can actually increase stress concentrations instead of reducing them. This means that when two pieces are joined using a weld, a proper bevel will ensure that the weld is strong and long lasting.
By creating an appropriately angled bevel, we can reduce stress concentrations, thereby minimizing the likelihood of failure under load. The bevel angle affects the surface area of a weld and thus its strength. For instance, a bevel angle that is too shallow might not allow for proper weld penetration, leading to a weaker connection. Bevels in engineering design are therefore a balancing act, between achieving maximum strength while keeping cost of manufacturing down.
Bevels have a wide range of engineering applications, ranging from simple joining of materials to preparing parts for complex processes. Some common applications include:
These varied applications demonstrate how versatile a bevel is within engineering and manufacturing. We can see that it’s not just about function, but sometimes it’s about how things look, and feel too.
Using bevels in manufacturing and engineering offers multiple advantages:
These functional and aesthetic benefits make beveling a common practice across many industries. The advantages of using bevels are very clear, they are not just there for looks. They add strength, ease of use, and make things safe.
Pipe beveling is a critical step in the process of joining pipes for various industrial applications. A pipe often needs to be beveled for welding to ensure a strong and complete weld. The beveling process provides the necessary gap for proper weld penetration.
Pipe beveling typically requires dedicated beveling machines that can precisely cut the required bevel angle on the pipe ends. The bevel ensures a strong weld by creating a larger surface area for welding. The proper bevel edge preparation for a pipe is a vital step that leads to a robust and reliable pipeline.
CNC (Computer Numerical Control) machines play an important role in the beveling process, as they are very precise. CNC machines are used for creating precise and consistent bevels on metal parts. Using cnc, engineers can create complex bevel designs with very tight tolerances that would be impossible to achieve manually.
CNC beveling ensures accuracy and repeatability and makes the manufacturing process more efficient. CNC machines can be programmed to make different bevels, including plain bevel, compound bevel, and j-prep bevel. These machines provide the versatility needed to meet the requirements of different types of bevels. When you need very high quality and exact bevel quality, CNC is the only way to go. We at CNC Fabrication pride ourselves on using the very latest cnc machines for our projects.
Selecting the appropriate beveling method depends on the specific requirements of your project. Factors to consider include:
Choosing the right beveling method is vital to ensure the success and longevity of your projects. It’s important to select an appropriate bevel that matches all requirements, but also consider cost and time. Often, this means evaluating different bevel techniques. Sometimes, you may require something that isn’t a common bevel, so be sure to partner with an expert.
Want to ensure your parts are beveled with precision and quality? Contact us at CNC Fabrication for expert guidance and solutions tailored to your needs. We pride ourselves on being the guide to bevel.
We offer a wide variety of services, including CNC Machining, Precision Machining, Sheet Metal Fabrication, and Rapid Prototyping.
Our advanced equipment and experienced team are here to ensure your project is a success.
What is the main purpose of a bevel?
A bevel’s main purpose is to prepare a surface or edge for a specific function, like welding, reducing stress, or making it safer and more visually appealing.
What types of bevels are most commonly used in welding?
The most common types used in welding include the V bevel, j-prep bevel, and plain bevel, each designed for specific welding needs.
How do bevels and chamfers differ?
While both involve angling an edge, a chamfer is an angled cut at 45 degrees primarily used for finishing, while a bevel is any angled edge with functional applications.
What are the benefits of using CNC machining for beveling?
CNC machining offers high precision, repeatability, and the ability to produce complex bevel designs, which are difficult to create manually.
Why is the bevel angle so important?
The bevel angle is very important because it has a direct impact on structural integrity, weld strength, and stress distribution.
How can I measure the bevel angle on a part?
You can measure bevel angles using tools such as a universal vernier bevel protractor.
Get the latest trends and facts about CNC fabrication from our blog.
Shenzhen Runkey Precision Technology Co. Ltd, a subsidiary of the Tensun Group, is your trusted one-stop solution for custom manufacturing from prototyping to production.Transforming your idea into reality with digital manufacturing resources,streamlined processes, expert guidance,accelerated timelines, and uncompromising quality.
©2024. CNC Fabrication All Rights Reserved.