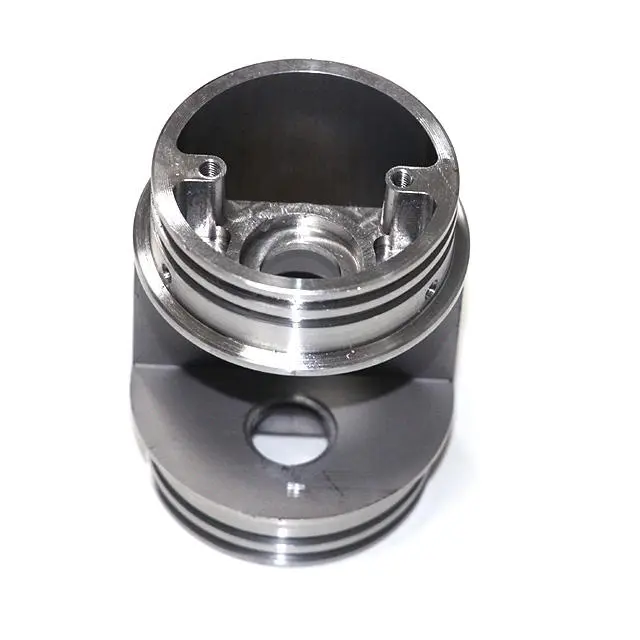
- +8615586668226
- [email protected]
- No. 30, Hongbang Industrial Park, Shenzhen
Selective laser sintering (SLS) is an additive manufacturing technique that uses a laser to fuse together small particles of powder to create a solid, three-dimensional object. Unlike other 3D printing technologies that rely on support structures, SLS 3D printing doesn’t require them because the unsintered powder surrounding the part provides the necessary support during the printing process. This allows for creating incredibly intricate and complex geometries.
In an SLS 3D printing process, a thin layer of powder is spread onto a build platform. Then, a laser scans the cross-section of the part on the powder bed, selectively sintering (fusing) the powder particles together. Once the layer is complete, the build platform lowers, a new layer of powder is applied, and the process repeats. This continues until the entire part is formed within the powder bed. The final step involves carefully removing the 3D printed parts from the unsintered powder. The magic of selective laser sintering lies in the precision and control of the laser, enabling the creation of strong, durable parts.
While all 3D printers create objects layer by layer, the way they do it varies significantly. Unlike fused deposition modeling (FDM), which extrudes molten plastic, or stereolithography (SLA), which cures liquid resin, SLS printers use a laser to fuse powder particles together. This difference has huge implications. SLS 3D printing allows for building more intricate parts without support structure, and the mechanical properties of the parts are often superior, especially when compared to FDM.
The use of powder as the raw material in sls printing also gives it unique advantages when considering material properties. The selective laser sintering printer uses a high-power laser to raise the temperature of the powder bed, allowing it to fuse together with the prior layer. While FDM and SLA printers might require the addition of support material which must be removed after printing, the unsintered powder in sls acts as its own support material. This means that SLS is well suited for complex designs and shapes. In addition, SLS printers often have a bigger build volume, enabling users to print larger parts or multiple smaller 3d printed parts in a single run.
The laser is the heart of selective laser sintering. The laser is used to laser selectively fuse the powder particles together. It’s a carbon dioxide laser, and it’s designed to precisely control the amount of heat applied, fusing the powder particles together without melting them entirely. This precise control over the laser beam allows for the creation of parts with excellent mechanical properties and intricate details.
The laser scanning system guides the laser across the powder bed, following the design contours of each layer of the 3D model. This accuracy is paramount in ensuring the final part matches the cad file exactly. The type of laser used and the parameters of its operation, such as power and scanning speed, are crucial factors in the sintering process. The use of a laser to sinter small particles makes the process remarkably efficient. Because the laser only interacts with the powder at the exact places the part will occupy, sls makes for minimal waste. The laser to fuse together successive layers is what gives sls 3d printing’s objects their strength and durability.
SLS 3D printing offers a wide range of materials, though it’s most commonly used with polymers, including nylon, as well as thermoplastics and composite materials. Nylon is particularly favored for sls parts due to its strength, flexibility, and resistance to chemicals and heat. Different types of nylon materials and other options offer a variety of mechanical properties, allowing for diverse applications. This capability gives designers a lot more flexibility than other 3d printing technologies.
The properties of the materials used in sls play a critical role in the performance of the final 3d printed parts. The mechanical properties, including tensile strength, impact resistance, and flexibility, can be tailored to meet specific application requirements. Other materials available for sls include composite materials which are commonly used where specific properties such as stiffness or heat resistance is required, expanding the usefulness of the process and technology. The fact that sls can use so many different materials, and easily change to new ones, adds to its overall versatility of sls.
One of the most significant advantages of SLS is its ability to produce parts with high accuracy, intricate details, and excellent mechanical properties without using support structure. This freedom from supports not only simplifies the printing process but also allows for the design and fabrication of geometries that are practically impossible to produce with traditional manufacturing process. This capability makes sls ideal for complex designs.
The unsintered powder in the sls printer provides natural support during the 3d printing process, reducing the need for post-processing to remove supports and improving overall efficiency. Additionally, SLS is known for its excellent build consistency and repeatability, which makes it a favored choice for industrial-scale manufacturing. This means sls parts have good dimensional accuracy and high-quality surface finishes. When compared to other 3d printing technologies for professionals, the speed, precision, and strength of sls are unmatched.
Rapid prototyping is a core application for selective laser sintering, and this is because its high accuracy, design freedom, and ability to produce functional parts quickly. Designers can rapidly create and test physical models of their designs. Furthermore, the excellent mechanical properties of sls parts makes them well suited for functional tests under real-world conditions. This makes the entire process of designing and improving much faster and more effective.
Beyond rapid prototyping, sls is also increasingly being used for the production of end-use parts. The durability, strength, and chemical resistance of materials like nylon make sls 3d printing suitable for creating final components that are used in a variety of industries. The ability of sls to create very complex geometries also expands its applications into other industries, making it ideal for very specialized or hard-to-make products. This means that, unlike other 3d printing technologies, sls can be used for more than simply testing designs or mockups.
SLS 3D printing is exceptionally well suited for handling complex geometries because it doesn’t require support structure. The powder bed itself acts as the support, allowing for the fabrication of highly intricate designs with ease. Parts with internal voids, thin walls, and lattice structures, which are difficult or impossible to achieve with other manufacturing methods, are easily produced using selective laser sintering.
This capability of sls is a real game changer for designers, enabling them to bring even their most ambitious visions to life. The process of selective laser sintering 3d printing uses the power of the laser to fuse powder into exactly the shape needed, while the unused powder provides support during the build. This makes it easier for the laser to create very complex shapes, because there’s no need to add any support material that has to be removed later. The ease of creating intricate designs makes sls ideal for complex geometries.
While sls 3d printing eliminates the need for support structures, it still requires some degree of sls post-processing. After the printing process, the finished part needs to be removed from the unsintered powder. This typically involves carefully separating the sls parts from the powder bed and then removing any remaining loose powder from the part’s surfaces.
Additional sls post-processing steps can include cleaning, surface finishing, and sometimes, dyeing or painting to achieve the desired aesthetics or functional properties. These processes might involve mechanical methods like sandblasting to remove remaining powder residue or chemical treatments to smooth surfaces. The level of sls post-processing is much simpler compared to other 3d printing processes due to the lack of support material which must be cut off, sanded, and cleaned.
Selective laser sintering has found widespread application across diverse industries due to its versatility and production capabilities. The industrial sls sector benefits from the ability to produce 3d printed parts with high precision and excellent mechanical properties, which means it’s used in industries such as aerospace, automotive, and medical equipment. In these sectors, sls printing can be used for anything from rapid prototyping to end-use part manufacturing.
The flexibility and accuracy of sls also makes it popular for consumer goods, electronics, and robotics, where intricate and durable components are essential. The use of industrial sls systems for manufacturing also cuts down on production time and wastage. With new technological advancements, the range of materials available for industrial sls 3d printers is constantly increasing, further expanding the reach of the process into other industries. The capability of sls 3d printing accelerates the time to market in many industries.
If you’re looking for a 3d printing solution that offers high precision, intricate detail, and durability, then sls 3d printing might be the right fit for you. A variety of 3d printing service providers offer selective laser sintering, allowing both small businesses and large enterprises to make use of sls technology without investing in the equipment themselves. If you’re curious about how sls 3d printing works, these bureaus will often offer sample parts for inspection and testing.
When selecting a sls 3d printing service, consider factors such as the materials they offer, the size of their build volume, the quality of their machinery and expertise of their team, and the post-processing services they provide. It’s also important to inquire about the lead time for projects, and of course, the cost. With so many 3d printing solutions on the market, you’ll want to pick the service that best matches your needs. And if you need a service that’s flexible and can produce a large number of high-quality parts, sls is one of the best 3d printing options available.
How does selective laser sintering compare to fused deposition modeling (FDM) and stereolithography (SLA)?
Selective laser sintering (SLS) uses a laser to fuse powder particles, offering higher accuracy, no support structure, and superior mechanical properties, unlike FDM (which extrudes molten plastic) or SLA (which cures liquid resin).
What are the typical materials used in SLS printing?
Nylon is the most common, but many types of plastics and composites are also used, each providing different mechanical properties suitable for a variety of applications.
Is SLS 3D printing suitable for rapid prototyping?
Yes, SLS is excellent for rapid prototyping because of its high speed and precision, enabling designers to quickly iterate and test their designs with functional parts.
Can SLS parts be used as end-use parts?
Absolutely. The strength, durability, and chemical resistance of SLS parts, particularly those made of nylon, make them suitable for many end-use part applications.
Is post-processing required after SLS printing?
Yes, some post-processing is needed to remove the unsintered powder and to improve surface finish or add color, but it is typically less extensive than other 3D printing methods.
Is SLS technology makes sls parts expensive?
The cost of sls has decreased in recent years but still remains higher than FDM or SLA for entry level parts, however due to its superior performance and its ability to create highly complex and durable sls parts, it continues to remain the standard for specialized manufacturing requirements. Since sls produces very high-quality objects, it’s become more common in many industries.
Ready to leverage the power of selective laser sintering for your projects? Contact us today to explore how our CNC Fabrication services can bring your ideas to life. Explore our other services such as CNC Machining, CNC Milling, and Precision Machining, to see the full range of our offerings. We also offer a number of Fabrication Services and CNC Solutions. If you’re working with specific materials you can see more about our Materials services.
Get the latest trends and facts about CNC fabrication from our blog.
Shenzhen Runkey Precision Technology Co. Ltd, a subsidiary of the Tensun Group, is your trusted one-stop solution for custom manufacturing from prototyping to production.Transforming your idea into reality with digital manufacturing resources,streamlined processes, expert guidance,accelerated timelines, and uncompromising quality.
©2024. CNC Fabrication All Rights Reserved.