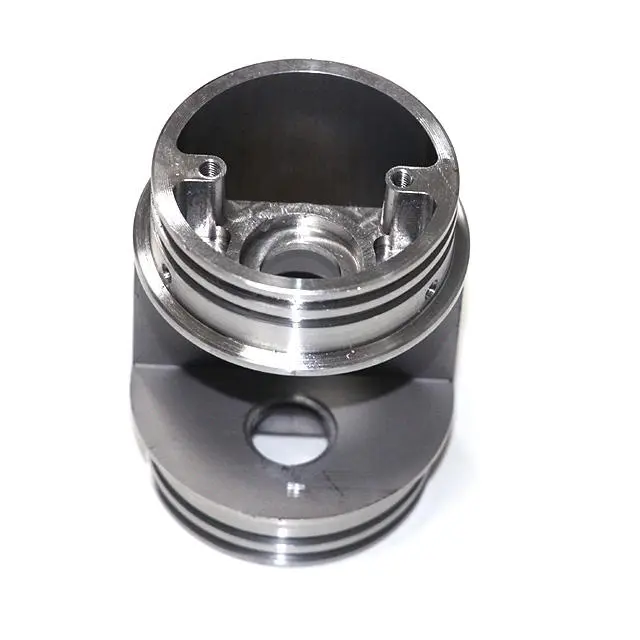
- +8615586668226
- [email protected]
- No. 30, Hongbang Industrial Park, Shenzhen
A CNC machine is a machine tool automated and controlled by a computer. Unlike manual machines, where an operator manually controls the machining process, CNC machines execute pre-programmed sequences defined by G-code, a specialized programming language. This code directs the machine’s movements, controlling the cutting tool‘s position, speed, and feed rate as it interacts with the workpiece. This precise control allows for accuracy and consistency in producing complex parts, impossible to achieve with manual machining.
CNC machines have revolutionized manufacturing, offering unprecedented precision, repeatability, and efficiency. They have become indispensable across various industries, from aerospace to automotive, medical devices to consumer products. The ability of a single CNC machine to perform multiple machining operations significantly reduces production time and cost.
Several types of CNC machines cater to various manufacturing needs. Common examples include CNC mills, lathes, routers, laser cutters, plasma cutters, waterjet cutters, and electrical discharge machining (EDM) machines. Each type of CNC machine specializes in specific machining processes, offering unique capabilities for different materials and applications.
CNC mills: These machines use rotating cutting tools to remove material from a workpiece, ideal for creating complex 3D shapes.
Lathes: CNC lathes rotate the workpiece against a stationary cutting tool, primarily used for cylindrical or symmetrical parts.
Routers: Similar to mills, CNC routers are often used for larger workpieces and materials like wood and plastics.
Understanding the distinctions between these types of CNC machines is crucial for selecting the right tool for a specific manufacturing task. This knowledge allows businesses to optimize their manufacturing process and achieve the desired results efficiently.
The history of CNC traces back to the mid-20th century, evolving from early numerical control systems to the sophisticated computer numerical control technology we know today. Initially, punched tapes were used to control machine tools, later replaced by computers, ushering in the era of modern CNC. This transition marked a significant leap in automation, enabling greater precision, flexibility, and efficiency in manufacturing.
The development of CNC systems revolutionized manufacturing, allowing for complex parts to be produced with unprecedented accuracy and repeatability. This breakthrough paved the way for advancements in various industries, including aerospace, automotive, and medical devices. CNC technologies continue to evolve, with ongoing innovations driving further improvements in speed, precision, and capabilities.
CNC machines operate based on a set of instructions written in G-code. This specialized programming language tells the machine how to move, what speed to use, and which cutting tool to employ. The G-code is loaded into the CNC machine, which then interprets these instructions to control the machining operation. This precise machine control is the foundation of CNC machining’s accuracy and repeatability.
The process begins with a CAD (Computer-Aided Design) model, which is then translated into G-code using CAM (Computer-Aided Manufacturing) software. This G-code provides the instructions that the CNC machine follows to create the physical part. Understanding how G-code and machine control work is essential for anyone involved in CNC programming or operation. It allows for fine-tuning the machining process to achieve optimal results.
CNC machining processes encompass a wide range of techniques, including milling, turning, drilling, laser cutting, plasma cutting, and waterjet cutting. Each process utilizes specific CNC tools and techniques to achieve different results. Milling, for instance, uses rotating cutters to remove material, while turning shapes the workpiece by rotating it against a stationary tool. CNC turning is especially useful for creating cylindrical parts.
Laser cutting uses a high-powered laser to cut through materials, offering high precision and speed. Plasma cutting uses a plasma torch to cut through electrically conductive materials. Waterjet cutting uses a high-pressure jet of water mixed with abrasive particles to cut various materials. Understanding these CNC machining processes is vital for choosing the right method for a specific manufacturing task.
CNC machines are used across a vast range of industries, including Aerospace, Automotive, Medical Devices, Electronics, Consumer Products, and Robotics. In aerospace, CNC machines are crucial for producing precise components for aircraft and spacecraft. The automotive industry uses CNC machines to manufacture engine parts, body panels, and other critical components.
The medical device industry relies on CNC machining for creating implants, surgical instruments, and other intricate devices. The versatility of CNC machines allows them to be used in various applications, making them an essential tool in modern manufacturing.
Benefits of computer numerical control machining include increased precision, improved efficiency, reduced labor costs, enhanced repeatability, and the ability to create complex parts. CNC machines produce parts with exceptional accuracy, minimizing errors and ensuring consistent quality. They also automate many manufacturing processes, reducing the need for manual labor and increasing production speed. The high repeatability of CNC machining ensures that every part produced meets the same precise specifications.
Modern CNC systems incorporate advanced software and hardware components to enhance precision, speed, and automation. These systems often include CAD/CAM software, advanced controllers, and high-performance machine tools. CAD/CAM software allows for the design and programming of complex parts, while advanced controllers provide precise control over the machining operation. High-performance machine tools ensure the efficient and accurate execution of the machining process. CNC Solutions are continuously evolving, with new technologies and innovations pushing the boundaries of manufacturing capabilities.
Selecting the appropriate CNC machine depends on various factors, such as the type of materials being machined, the complexity of the parts, and the production volume. Different types of CNC machines are suited for different applications. For example, a CNC milling machine is ideal for creating complex 3D shapes, while a CNC lathe is better suited for cylindrical parts. Considering these factors is crucial for choosing a machine that meets specific manufacturing requirements. Machining Services and Fabrication Services cater to various needs and applications, providing specialized expertise for different manufacturing processes.
The future of CNC machining looks bright, with ongoing advancements in areas like 5 Axis CNC Machining and Precision Machining. These advancements promise to further enhance precision, speed, and automation in manufacturing. Five-axis machining allows for complex parts to be machined in a single setup, reducing production time and improving accuracy. Precision machining focuses on achieving extremely tight tolerances, pushing the boundaries of what’s possible in manufacturing.
A career as a CNC machinist offers exciting opportunities in a rapidly evolving industry. CNC machinists are skilled professionals who operate and program CNC machines, playing a crucial role in the manufacturing process. This career requires a strong understanding of CNC programming, machine operation, and manufacturing processes. With the increasing demand for skilled machinists, a career as a CNC machinist can be a rewarding path for those interested in a hands-on role in advanced manufacturing.
What is the difference between CNC milling and CNC turning? CNC milling uses rotating cutters to remove material from a stationary workpiece, while CNC turning rotates the workpiece against a stationary cutting tool.
What is G-code, and why is it important in CNC machining? G-code is a programming language that controls the movements of a CNC machine. It is essential for defining the machining operations and ensuring the accurate production of parts.
What are the key benefits of using CNC machines in manufacturing? CNC machines offer increased precision, improved efficiency, reduced labor costs, enhanced repeatability, and the ability to create complex parts.
What are some common applications of CNC machining in different industries? CNC machining is used in aerospace, automotive, medical devices, electronics, consumer products, and various other industries.
What skills are required to become a CNC machinist? CNC machinists need a strong understanding of CNC programming, machine operation, and manufacturing processes.
How is CNC machining different from 3D printing? CNC machining is a subtractive process where material is removed from a workpiece, while 3D printing is an additive process where material is added layer by layer to build a part.
CNC machining uses computer control to automate machine tools, offering high precision and efficiency.
Different types of CNC machines exist, each specializing in specific machining processes.
G-code is the programming language used to control CNC machines.
CNC machining is used across various industries for diverse applications.
CNC machining offers numerous benefits, including increased precision, improved efficiency, and reduced labor costs.
A career as a CNC machinist can be a rewarding path in advanced manufacturing.
Get the latest trends and facts about CNC fabrication from our blog.
Shenzhen Runkey Precision Technology Co. Ltd, a subsidiary of the Tensun Group, is your trusted one-stop solution for custom manufacturing from prototyping to production.Transforming your idea into reality with digital manufacturing resources,streamlined processes, expert guidance,accelerated timelines, and uncompromising quality.
©2024. CNC Fabrication All Rights Reserved.