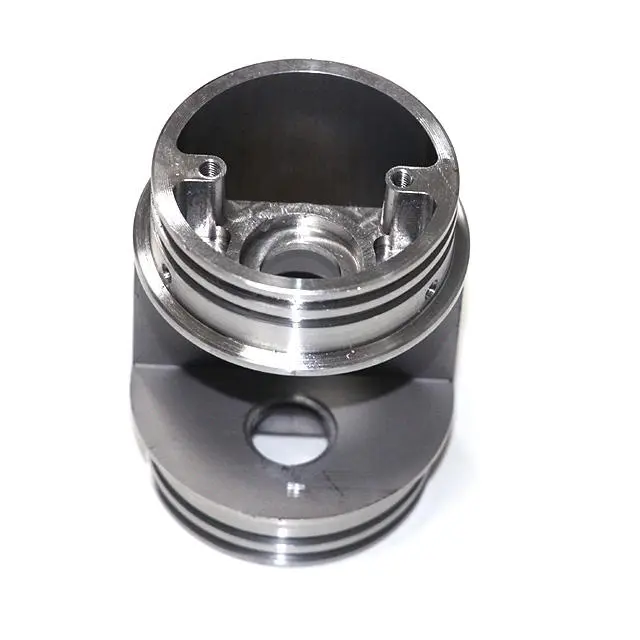
- +8615586668226
- [email protected]
- No. 30, Hongbang Industrial Park, Shenzhen
Stiffness is a measure of a material’s resistance to deformation under load. A stiff material requires a greater force to deform a given amount than a material with low stiffness. Think of a thick steel beam – it’s very stiff and requires a substantial force to bend, unlike a thin plastic ruler. The stiffness of material is quantified by the modulus of elasticity, also known as Young’s modulus.
Stiffness is crucial in CNC Machining processes, ensuring precision and preventing unwanted distortions during operations like CNC Milling and CNC Turning. A higher modulus of elasticity indicates greater stiffness. For instance, steel has a much higher modulus than rubber, meaning it’s much stiffer.
Hardness measures a material’s resistance to localized plastic deformation, typically caused by indentation or scratching. Hardness testing often involves pressing an indenter into the material surface and measuring the size or depth of the resulting indentation. High hardness materials resist scratching and indentation better than softer materials. Diamond, for example, possesses exceptional hardness.
Different scales quantify hardness, including Rockwell, Brinell, and Vickers. While related to strength, hardness focuses specifically on surface resistance to deformation, unlike stiffness, which considers the overall deformation of the material. It’s a vital consideration for Surface Finishing during CNC Solutions.
Strength describes a material’s ability to withstand an applied load without fracturing or yielding. Several types of strength exist, including tensile strength, compressive strength, and yield strength. Tensile strength is the highest stress a material can withstand before it begins to permanently deform or fracture. Yield strength signifies the stress at which a material begins to deform plastically, permanently altering its original shape.
Strength is paramount in structural applications, ensuring components can withstand the forces they’ll experience. In Fabrication Services, selecting materials with appropriate strength is critical for component longevity and safety. Consider the strength requirements for a bridge – it must bear substantial weight without collapsing.
While sometimes used interchangeably, stiffness and hardness represent distinct material properties. Stiffness focuses on a material’s resistance to elastic deformation – how much it resists bending or stretching under stress and strain. Hardness, on the other hand, quantifies its resistance to localized plastic deformation – how much it resists indentation or scratching.
Imagine a spring. It can be relatively soft (low hardness), easily scratched, but very stiff, requiring significant force to compress. Conversely, a ceramic material can be very hard (scratch-resistant) but brittle and easily fractured, indicating lower strength and potentially lower stiffness.
Although related, stiffness and strength are not directly proportional. A stiff material isn’t necessarily strong, and a strong material isn’t always stiff. For instance, glass is stiff but brittle (low strength), while some plastics can be relatively strong but flexible (low stiffness).
The relationship between stiffness and strength depends on the material’s microstructure and bonding characteristics. Generally, materials with strong interatomic bonds tend to be both stiff and strong, like metal. However, factors like defects and grain boundaries can influence strength independently of stiffness.
The stress-strain curve graphically depicts a material’s behavior under tensile loading, revealing both stiffness and strength characteristics. The slope of the elastic region of the curve represents the modulus of elasticity (stiffness), while the ultimate strength is the highest point on the curve. The yield strength is the point at which the curve deviates from linearity, indicating the onset of plastic deformation.
In Material Selection, engineers consider the interplay of stiffness, hardness, and strength, choosing the best material for a given application. For instance, aerospace components might require high stiffness and strength to withstand flight loads, while cutting tools need high hardness to resist wear. Understanding the Difference Between Strength and Stiffness is paramount.
From automotive chassis to medical implants, stiffness and strength play vital roles across diverse industries. Aerospace engineers prioritize high stiffness and strength materials like titanium alloys for aircraft structures, while automotive manufacturers might choose high-strength steel for car bodies.
Stiffness can be calculated using the modulus of elasticity and the component’s geometry. Strength is typically determined through standardized testing methods like tensile testing. Specialized software and engineering handbooks provide detailed procedures and formulas for calculating these properties.
A common misconception is that hardness directly equates to strength. While related, hardness primarily assesses surface resistance, while strength considers overall material failure. Another misconception is that all stiff materials are also strong, which is not always the case, as demonstrated by brittle materials like glass.
How can I improve a material’s stiffness? Stiffness can be increased through alloying, heat treatments, and composite reinforcement.
What is the difference between axial stiffness, bending stiffness, shear stiffness, and torsional stiffness? These terms describe stiffness under different loading conditions – axial (tension/compression), bending, shear, and torsion (twisting).
Is there a relationship between tensile strength and hardness? Generally, there’s a positive correlation, but it’s not a direct relationship.
How do I choose the right material for my application based on stiffness and strength? Consider the specific loading conditions, required performance, and environmental factors to select a material with the appropriate balance of stiffness, hardness, and strength.
Stiffness measures resistance to elastic deformation.
Hardness measures resistance to localized plastic deformation.
Strength represents the ability to withstand loads without failure.
These properties are interconnected but distinct.
Material selection involves balancing stiffness, hardness, and strength based on application requirements. Choosing the right material is essential for ensuring product performance, reliability, and safety. Consider Machining Services for precise component fabrication.
Remember these points when selecting materials for your next CNC fabrication project!
Get the latest trends and facts about CNC fabrication from our blog.
Shenzhen Runkey Precision Technology Co. Ltd, a subsidiary of the Tensun Group, is your trusted one-stop solution for custom manufacturing from prototyping to production.Transforming your idea into reality with digital manufacturing resources,streamlined processes, expert guidance,accelerated timelines, and uncompromising quality.
©2024. CNC Fabrication All Rights Reserved.