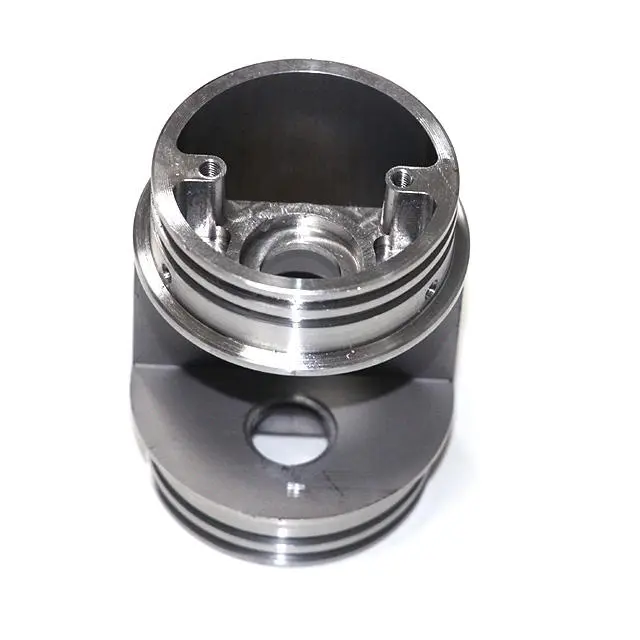
- +8615586668226
- [email protected]
- No. 30, Hongbang Industrial Park, Shenzhen
Galvanize, in the simplest terms, means to coat a metal with a protective layer of zinc. This process is primarily used to prevent corrosion and extend the lifespan of metal components. The term “galvanize” has its roots in the name of Luigi Galvani, an Italian scientist who made significant discoveries in the field of electricity, although the process itself does not directly involve electrical currents. While the term is commonly associated with steel, other metals can also be galvanized. The galvanization process essentially creates a barrier between the base metal, such as steel or iron, and the environment, preventing rust and other forms of corrosion. This makes galvanized steel a popular choice in various industries.
The need for galvanize arises because, over time, most metals including steel, are prone to rust and deterioration when exposed to moisture and air. Galvanized metal addresses this by adding a zinc coating, which acts as a sacrificial anode. This means that when exposed to corrosive elements, the zinc coating corrodes first, protecting the underlying metal. This zinc coating is typically applied by dipping the steel into a bath of molten zinc, leading to a strong and durable bond that greatly increases corrosion resistance.
While the most commonly galvanized metal is steel, especially steel sheet, other metals can also be galvanized using various methods. Iron or steel, due to their strength and cost-effectiveness, are ideal base metals for this process. However, metals such as stainless steel, aluminum, and even some copper alloys can also undergo forms of galvanization or similar coating processes. It’s important to understand that the specific method used to galvanize might vary based on the type of metal used, and some metals require different surface preparation to ensure proper adhesion of the zinc coating.
It’s a common misconception that galvanize is exclusive to steel, but any metal that requires corrosion resistance or a better surface finish might be a candidate for such a process. In metal fabrication, understanding what metals can be galvanized enables engineers to select the right materials for specific applications, maximizing the longevity and durability of metal parts and metal products. The process creates a layer of zinc that protects the metal from elements, extending its useful life in a variety of settings.
The galvanization process is the application of a zinc coating to steel or iron to protect the metal from corrosion. The most common method is hot-dip galvanized, where the steel is dipped in a bath of molten zinc. Before this process involves dipping, the steel is thoroughly cleaned to ensure proper adhesion of the zinc coating. This cleaning involves removing any dirt, grease, or rust from the surface of the steel.
After cleaning, the steel is immersed into the molten zinc bath. The molten zinc chemically reacts with the steel and forms a layer of zinc that bonds with the steel. This creates a tough and durable galvanized coating. The thickness of the zinc coating depends on factors like dipping time and the composition of the steel. Once the steel has been coated, it is removed from the molten zinc and air-cooled, finalizing the galvanization process. This process ensures that the steel provides excellent protection against corrosion. There is also electro-galvanizing which is used in certain applications and provides a thinner coat of zinc over the surface.
The advantages of galvanized steel are significant, making it a preferred material in many industries. Primarily, galvanized steel provides exceptional corrosion resistance, a key benefit that extends the lifespan of steel structures and steel products. This means reduced maintenance and replacement costs, offering long-term value and a good return on investment. The zinc coating acts as a sacrificial barrier; if the galvanized coating is scratched, the zinc will still protect the steel substrate from corrosion.
In addition to corrosion resistance, galvanized steel has high durability and strength. The galvanizing process creates a metallurgically bonded layer of zinc that is incredibly resistant to abrasion and impact, ensuring that the steel will stand up to harsh conditions. Furthermore, the process of galvanization is relatively cost-effective when compared to other metal coating methods. The availability of galvanized steel also means it is easier to procure and can be used across a wide range of applications, from construction to manufacturing. All these benefits of galvanized materials contribute to its wide acceptance.
The benefits of galvanized materials are numerous. Firstly, the main reason for galvanizing metal is corrosion resistance. A zinc coating significantly slows down the corrosion process. For example, if you left a piece of steel outdoors, it would rust quickly, but a similar piece of galvanized steel would remain protected. The layer of zinc not only provides a physical barrier to moisture, but also creates an electrochemical one. The zinc corrodes preferentially before the steel, thereby protecting the steel from rust and degradation.
Another key benefit is the extended lifespan of the galvanized products. The zinc coating provides long-term protection to the metal, reducing the need for frequent repairs or replacements. This is especially valuable for applications where maintenance is difficult or costly. Additionally, galvanized material often enhances the aesthetics of a metal product. The finish is smooth and uniform, lending itself to many uses in applications. When you want galvanized, you’re choosing a material that is both functional and durable. These benefits of galvanized contribute to its wide usage across several industries.
There are several types of galvanized steel, each suited to different applications. Hot-dip galvanized steel is the most common, where the steel is dipped into a bath of molten zinc. This process creates a robust and thick galvanized coating, ideal for outdoor and industrial applications. The hot-dip galvanized steel offers excellent corrosion protection in harsh environments. For example, in the automotive sector, hot-dip galvanized steel can be used in frames and body panels.
Another type is electro-galvanized steel, where a thin zinc coating is applied using an electrical current. This method provides a smoother, more uniform coating but is generally thinner than hot-dip galvanized steel, making it suitable for indoor and less aggressive environments. Galvannealed steel, a variation of electro-galvanized steel, undergoes an annealing process after the zinc coating is applied, which enhances its properties, such as paint adhesion. Selecting the correct type of galvanized steel is crucial for ensuring optimal performance and longevity. The manufacturing process may vary depending on the desired outcome.
While galvanized metal has numerous advantages, there are some disadvantages of galvanized to consider. One major concern is that the galvanized coating can be damaged or scratched, potentially exposing the underlying metal to corrosion. While zinc provides a good initial layer of protection to the metal, heavy impact or abrasive actions may chip the zinc coating, accelerating the rust process if left untreated. It’s important to note that once the zinc coating is compromised, the steel will be vulnerable to the elements.
Another downside is the potential for ‘white rust,’ a form of corrosion that can occur on the surface of galvanized steel when exposed to moisture and limited airflow. This appears as a white powdery deposit and can degrade the zinc coating over time, diminishing its corrosion resistance. Additionally, while the galvanizing process is cost-effective, it may not be as aesthetically appealing as other finishes for some applications. The coating can sometimes be uneven or have a spangled appearance. In certain niche fields, specialized coatings might be necessary to avoid these disadvantages of galvanized products.
Galvanized sheet metal is widely used across numerous industries due to its strength, durability, and excellent corrosion resistance. In the construction industry, galvanized steel sheet is frequently used for roofing, wall panels, and structural components where resistance to corrosion is essential. The steel sheet benefits from being protected by the zinc coating, increasing its lifespan and reducing the need for constant maintenance. In the automotive industry, galvanized sheet metal can be found in car body panels and chassis components, where rust and corrosion are significant concerns.
Beyond construction and automotive, galvanized sheet metal is essential for making HVAC systems, appliance housings, and agricultural equipment. Its versatility in sheet metal fabrication allows for complex designs. In these applications, the ease of forming and joining galvanized sheet metal contributes to efficient production. The benefits and applications are varied, which makes it a popular choice. Given these wide-ranging applications, galvanized sheet metal provides a combination of strength, formability, and corrosion protection, making it an indispensable material for many industries. Rolling the sheet metal also ensures uniformity in the final product.
The process and benefits of galvanizing are inextricably linked. The galvanization process involves coating steel or iron with a zinc coating, primarily to provide corrosion resistance. The steel process starts by thoroughly cleaning the steel, usually by removing any rust or scale, ensuring that the zinc adheres effectively. This ensures that the process creates the best results. The steel is then dipped into a bath of molten zinc, resulting in the zinc coating to bond with the steel. The key is the chemical reaction between the zinc and steel, creating a bond and a protective layer.
The main benefit of galvanized is the corrosion protection it provides. The zinc coating acts as a sacrificial anode; if it’s scratched or damaged, the zinc will corrode first, protecting the steel underneath. This electrochemical protection significantly extends the lifespan of steel components, especially in harsh environments. The process provides a long-lasting and cost-effective method to protect the metal. This process greatly reduces the need for frequent maintenance or replacements.
The applications of galvanized materials are extensive. Due to its exceptional corrosion resistance, galvanized steel is used widely in the construction sector for everything from roofing and wall panels to structural beams and guardrails. Galvanized steel can be used because it can withstand diverse weather conditions and provides long-term structural integrity. The automotive sector also relies heavily on galvanized steel, using it for vehicle frames, body panels, and components that need protection to the metal from rust and other forms of corrosion.
Another area that employs galvanized steel is in industrial equipment and machinery. The strength and durability of galvanized metal make it suitable for use in agricultural, marine, and manufacturing equipment. Even everyday items such as fences, nails, and screws are often made of galvanized steel due to their exposure to elements. From small metal parts to large steel structures, the range of applications is diverse. The versatility and reliability of galvanized steel is a popular choice across many fields.
How long does a galvanized coating typically last?
The lifespan of a galvanized coating can vary, but typically, it can last from 20 to 70 years, depending on the environmental conditions and the thickness of the zinc coating.
Is galvanized steel safe for use in drinking water applications?
Yes, galvanized steel is generally safe for drinking water applications provided that the materials conform to the right safety standards.
Can galvanized steel be welded?
Yes, but it requires specific welding techniques to avoid damaging the zinc coating and to ensure the weld has a good level of corrosion resistance.
Is galvanized steel environmentally friendly?
The zinc coating is recyclable, and while the galvanizing process itself can have environmental impacts, the long lifespan of galvanized steel reduces the overall use of resources by reducing the need for replacement.
What is the difference between hot-dip galvanizing and electro-galvanizing?
Hot-dip galvanizing uses a bath of molten zinc, creating a thick, robust coating, while electro-galvanizing uses an electrical current to apply a thinner, more uniform layer of zinc.
Can I paint over galvanized steel?
Yes, but the surface of a metal must be correctly prepared to ensure the paint adheres well to the galvanized surface.
Interested in learning more about our metal fabrication capabilities? Contact us today to discuss your project needs. We also offer a range of services, including CNC Machining, Sheet Metal Fabrication, and Rapid Prototyping. For industries such as Aerospace and Automotive, we provide top quality metal solutions. Discover how our expertise in On Demand Manufacturing can assist you with metal products and metal parts today.
Get the latest trends and facts about CNC fabrication from our blog.
Shenzhen Runkey Precision Technology Co. Ltd, a subsidiary of the Tensun Group, is your trusted one-stop solution for custom manufacturing from prototyping to production.Transforming your idea into reality with digital manufacturing resources,streamlined processes, expert guidance,accelerated timelines, and uncompromising quality.
©2024. CNC Fabrication All Rights Reserved.