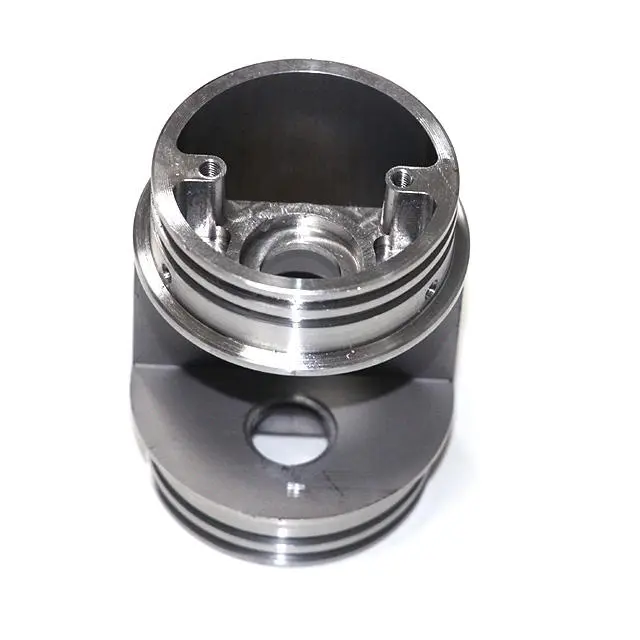
- +8615586668226
- [email protected]
- No. 30, Hongbang Industrial Park, Shenzhen
Electrical discharge machining (EDM) is a non-traditional, controlled metal-removal process that uses electrical discharges (sparks) to create a desired shape or finish. I’ve seen firsthand how this method excels in shaping hard metals and intricate designs that are challenging for conventional machining methods. EDM is a metalworking technology that is particularly useful for parts resistant to conventional machining processes. Unlike traditional methods that rely on mechanical force, EDM uses an electrically conductive material to cut through the workpiece with precision.
EDM is a versatile process used across industries to cut a variety of hard metals. My experience with EDM has shown me its ability to achieve tight tolerances and smooth surface finishes. It’s particularly useful in industries such as aerospace, automotive, and medical device manufacturing, where precision is paramount. EDM allows for complex shapes and designs that would be difficult or impossible to achieve with other methods.
A wire EDM machine operates on the principle of controlled erosion through rapid electrical discharges between a thin wire electrode and the workpiece, submerged in a dielectric fluid. Wire EDM uses a thin heated wire to cut the metal. As the wire electrode approaches the workpiece, the voltage difference causes a spark to jump across the gap, vaporizing a small amount of material.
I find the wire EDM process fascinating because the wire electrode itself doesn’t touch the workpiece. Instead, the spark does the cutting, creating a precise kerf. The dielectric fluid plays a crucial role by flushing away debris, cooling the wire electrode and workpiece, and controlling the spark. It’s an incredibly precise process. The wire EDM process involves a continuous feed of the wire electrode, ensuring a fresh cutting surface for consistent results.
There are primarily two types of EDM: sinker EDM (also known as ram EDM or conventional EDM) and wire EDM. Sinker EDM uses an electrode shaped like the desired cavity, while wire EDM, as we’ve discussed, employs a thin wire electrode. I’ve worked with both, and each has its strengths. EDM comes in two main forms: sinker EDM and wire EDM.
Sinker EDM is ideal for creating blind cavities, intricate details, and complex three-dimensional shapes. Wire EDM, on the other hand, excels at cutting through materials to create profiles and contours. Wire EDM uses a wire as the electrode, while sinker EDM uses an electrode shaped like the desired cavity. Choosing between sinker EDM and wire EDM depends on the specific application and desired outcome.
The main difference between sinker EDM and wire EDM lies in the type of electrode used and the resulting cut. As a manufacturing professional, I can tell you that sinker EDM creates a cavity by “sinking” a shaped electrode into the workpiece, whereas wire EDM cuts through the material like a high-tech saw. A difference between sinker EDM and wire EDM is that sinker EDM cannot produce narrower angles.
Sinker EDM is a better choice for complex 3D shapes, while wire EDM is preferred for intricate 2D profiles. Sinker EDM uses an electrode shaped like the desired cavity, while wire EDM uses a thin metal wire. Sinker EDM process is ideal for creating molds and dies, while wire EDM excels at creating punches and other intricate parts.
The advantages of wire EDM are numerous, especially in today’s precision-driven manufacturing landscape. I’ve personally witnessed how wire EDM can produce parts with exceptional accuracy and surface finish, often eliminating the need for secondary finishing operations. Wire EDM uses machining to create an electrode.
Wire EDM can handle a wide range of conductive materials, including hardened steels and exotic alloys. It’s also ideal for creating delicate and intricate features without exerting mechanical stress on the workpiece. Wire EDM allows manufacturers to produce parts with tight tolerances and excellent surface finishes.
Wire EDM finds applications in a diverse array of industries. From my experience, aerospace companies use it to create precise components for engines and airframes, while medical device manufacturers rely on it for intricate surgical instruments. This makes wire EDM particularly useful in industries that require high precision and intricate designs.
The automotive industry utilizes wire EDM for tooling, prototyping, and even production parts. I’ve also seen it used in the electronics industry to create connectors and other small, precise components. It is used to cut through a variety of materials. Wire EDM is used in various industries to cut a variety of hard metals. These include aerospace, automotive, medical devices, and electronics, among others.
Industry | Application |
Aerospace | Engine components, airframe parts |
Automotive | Tooling, prototypes, production parts |
Medical Devices | Surgical instruments, implants |
Electronics | Connectors, contacts |
Tooling and Dies | Mold and die components |
Robotics | Components for robotic systems |
Consumer Products | Parts for various consumer goods |
Energy and Renewable Energy | Components for energy generation and storage |
One of the great things about wire EDM is its versatility in handling various materials. I’ve worked with everything from hardened tool steels to exotic alloys like Inconel and titanium, all with excellent results. Wire EDM uses an electrically conductive material. The ability of wire EDM to handle difficult-to-machine materials makes it invaluable in many applications.
However, it’s important to remember that wire EDM is only suitable for conductive materials. Materials such as plastics and ceramics are not compatible with this process. As long as the material conducts electricity, wire EDM can likely handle it.
The dielectric fluid is a critical component of the wire EDM process. It serves multiple functions, including flushing away debris, cooling the wire electrode and workpiece, and controlling the spark. I always emphasize the importance of using the correct dielectric fluid and maintaining its quality for optimal results.
The dielectric fluid creates an optimal environment for the electrical discharges to occur. It also helps prevent premature wire breakage and ensures a smooth surface finish. Without it, the wire EDM process simply wouldn’t work. The dielectric fluid helps to control the wire and workpiece temperature.
Choosing between CNC machining and wire EDM depends on various factors, including the material, part geometry, and desired tolerances. In my experience, CNC machining is generally faster and more cost-effective for simpler shapes and softer materials. CNC machining can be used for simpler shapes. Wire EDM is preferred for complex shapes and hard materials. It is also a good choice when tight tolerances and a fine surface finish are required.
However, wire EDM shines when dealing with hard materials, intricate details, and tight tolerances. The precision of the machining process is also an important factor. Wire EDM is more precise than CNC machining.
Here is a comparison table for better understanding:
Feature | CNC Machining | Wire EDM |
Material | Wide range, including non-conductive | Conductive materials only |
Complexity | Moderate | High, especially for intricate 2D profiles |
Speed | Generally faster | Slower |
Cost | Lower for simple shapes and softer materials | Higher, but justified for complex shapes and hard materials |
Tolerance | Good | Excellent |
Surface Finish | Good, may require secondary finishing | Excellent, often no secondary finishing needed |
Cutting Tool | Solid tools (mills, drills, etc.) | Thin wire electrode |
Applications | General machining, prototyping, large parts | Intricate parts, hard materials, tight tolerances |
Process | Mechanical cutting with rotating tools | Electrical discharge erosion |
Limitations | Difficulty with very hard or brittle materials | Slower cutting speed, limited to conductive materials |
Advantages | Versatility, speed for simple parts, cost-effective | High precision, excellent surface finish, handles hard materials |
If you need help deciding, don’t hesitate to reach out. We can discuss your machining needs and determine the best approach for your project.
EDM technology is constantly evolving. I’m excited about advancements in automation, multi-axis machining, and improved wire electrode materials. These innovations promise even greater precision, efficiency, and versatility in the years to come.
One area to watch is the development of new dielectric fluids that offer improved performance and environmental friendliness. Another is the integration of artificial intelligence for process optimization and predictive maintenance. The future of EDM is bright.
What is the difference between EDM and wire EDM?
The main difference between EDM and wire EDM is the type of electrode used. EDM generally refers to sinker EDM, which uses a shaped electrode, while wire EDM uses a thin wire electrode to cut through the workpiece like a saw.
What are the advantages of wire EDM?
The advantages of wire EDM include high precision, the ability to cut hard and exotic materials, excellent surface finish, the ability to create intricate shapes, and minimal stress on the workpiece.
What materials can be used in wire EDM?
Wire EDM can be used on any conductive material, including steel, aluminum, copper, brass, titanium, and Inconel. The material must be able to conduct electricity for the process to work.
What industries use wire EDM?
Wire EDM is used in a wide range of industries, including aerospace, automotive, medical devices, electronics, tooling and dies, and any sector requiring high precision and intricate parts.
Here are the most important things to remember about wire EDM:
Wire EDM is a highly precise machining process that uses electrical discharges to cut conductive materials.
It excels at creating intricate shapes and working with hard materials.
Wire EDM offers advantages in terms of accuracy, surface finish, and the ability to handle delicate parts.
The dielectric fluid plays a crucial role in the wire EDM process.
Choosing between CNC machining and wire EDM depends on the specific application requirements.
EDM technology continues to advance, promising even greater capabilities in the future.
As a leading provider of CNC fabrication services, we at cnc-fabrication.com leverage the latest in wire EDM and other advanced manufacturing techniques to deliver exceptional results for our clients. Whether you need precision machining, sheet metal fabrication, or rapid prototyping, our team of experts is here to help. We also offer CNC solutions and assembly services.
Get the latest trends and facts about CNC fabrication from our blog.
Shenzhen Runkey Precision Technology Co. Ltd, a subsidiary of the Tensun Group, is your trusted one-stop solution for custom manufacturing from prototyping to production.Transforming your idea into reality with digital manufacturing resources,streamlined processes, expert guidance,accelerated timelines, and uncompromising quality.
©2024. CNC Fabrication All Rights Reserved.