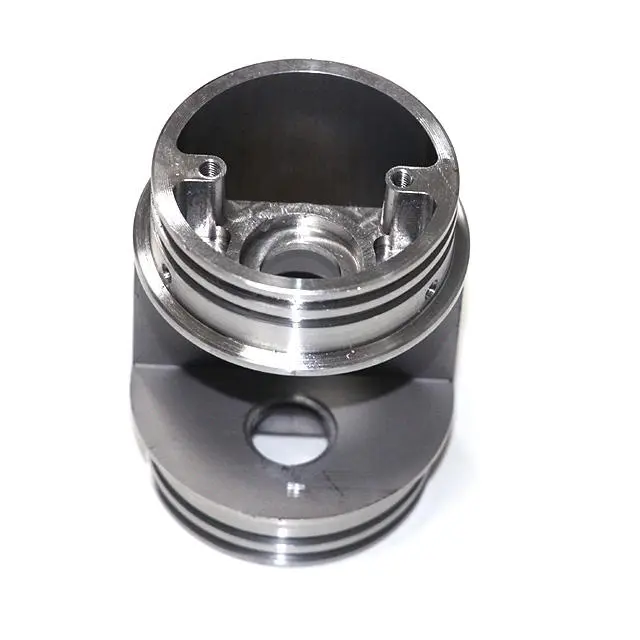
- +8615586668226
- [email protected]
- No. 30, Hongbang Industrial Park, Shenzhen
Wire EDM, also known as wire-cut EDM, is a non-traditional machining method that uses a thin wire electrode to cut through conductive materials via controlled electrical discharges. Imagine a tiny lightning bolt precisely eroding material with each spark. The wire, often made of brass or other specialized metals, never actually touches the workpiece. Instead, it’s guided by a CNC (Computer Numerical Control) machine along a programmed path, creating incredibly accurate and intricate shapes. The process takes place submerged in a dielectric fluid, typically deionized water, which helps control the sparking and flushes away eroded material.
A key aspect of the wire EDM process is the controlled discharge. The electrical potential between the electrode and the workpiece creates an electric spark that vaporizes a small amount of material. This precise material removal allows for incredibly tight tolerances and intricate details. The dielectric fluid also plays a crucial role in maintaining the stability of the electrical discharge machining process and ensuring a smooth surface finish.
One of the most significant advantages of wire EDM is its ability to machine complex parts that would be impossible to create with conventional machining methods. This is because wire EDM can cut extremely hard materials, regardless of their hardness, and it doesn’t require physical contact with the work piece, minimizing stress and distortion.
Furthermore, wire EDM offers exceptional precision. The fine metal wire, controlled by a CNC machine, can achieve incredibly tight tolerances, making it ideal for intricate designs and small features. This precision, combined with the ability to cut virtually any conductive material, makes wire EDM a versatile solution for various industries. 1
Wire EDM excels at machining a wide range of electrically conductive materials. This includes hardened steels, titanium alloys, carbide, and even exotic metals like Inconel. This versatility makes wire EDM an invaluable tool across numerous industries, from aerospace to medical devices.
The ability to machine such a diverse range of materials, coupled with the precision of the wire EDM process, opens up design possibilities not achievable with conventional cutting tools. Whether you’re working with aluminum extrusion or intricate die casting components, wire EDM offers a solution.
Numerous industries rely on wire EDM services for their intricate and precise machining needs. Aerospace and automotive manufacturers utilize wire EDM to create complex engine components and lightweight structural parts. The medical device industry leverages wire EDM to manufacture delicate surgical instruments and implants. Electronics manufacturers use wire EDM for creating intricate circuit boards and connectors.
Wire EDM also finds extensive use in tooling and dies, robotics, and even art and design. Its ability to create precise and complex shapes makes it a valuable asset in these fields. For those exploring rapid prototyping or needing on-demand manufacturing, wire EDM offers a swift and accurate solution. You can explore more about these solutions on our CNC Solutions page.
Unlike conventional machining which relies on mechanical force, wire EDM uses electrical discharges to remove material. This key difference allows wire EDM to easily machine hard and intricate shapes without the limitations of physical cutting tools. Think of laser cutting – it’s another non-contact method that offers precision. We delve into laser cutting on our Laser Cutting page.
Conventional machining struggles with very hard materials and intricate details. Wire EDM, on the other hand, excels in these areas. Its precision and ability to cut intricate shapes make it the preferred choice for complex components.
The precision of wire EDM stems from the fine wire electrode, typically a thin wire ranging from 0.002″ to 0.012″ in diameter. This thin wire, combined with the controlled electrical discharges, allows for extremely precise cuts. The CNC machine controls the movement of the wire, ensuring accurate positioning and consistent results.
The dielectric fluid also plays a role in achieving high precision. It helps control the sparking process and flushes away eroded material, ensuring a clean and accurate cut. This precision makes wire EDM ideal for creating complex shapes and meeting tight tolerances.
There are primarily two types of EDM machines: wire EDM and sinker EDM (also known as ram EDM or plunge EDM). Wire EDM, as discussed extensively, uses a thin wire to cut through conductive material. Sinker EDM, on the other hand, uses a shaped electrode that is plunged into the work piece to create a cavity.
While both methods utilize the principle of electrical discharge machining, they serve different purposes. Wire EDM is ideal for cutting complex two-dimensional shapes, while sinker EDM is better suited for creating three-dimensional cavities and molds.
Wire EDM finds application in a wide range of manufacturing processes. It’s crucial for creating intricate dies and molds used in industries like plastic injection molding and die casting. The process is also essential in the production of medical implants, aerospace components, and intricate tooling.
For instance, wire EDM is used to manufacture delicate surgical tools, turbine blades for aircraft engines, and complex gears for robotics. Its ability to cut hard materials with high precision makes it indispensable in these applications. We cover more about our work in the aerospace sector on our Aerospace page.
Choosing the right wire EDM machine depends on several factors, including the complexity of the parts you need to produce, the materials you’ll be working with, and the required tolerances. Consider the machine’s capabilities, such as its maximum cutting speed, wire diameter range, and available features.
Consulting with an experienced wire EDM specialist can help you determine the best machine for your specific needs. They can assess your requirements and recommend a machine that meets your production goals and budget.
The future of wire EDM is bright, with ongoing advancements pushing the boundaries of precision and efficiency. Researchers are exploring new dielectric fluids and electrode materials to improve cutting speed and surface finish. Integration with advanced automation and artificial intelligence is also on the horizon, promising greater automation and optimization of the wire EDM process.
These advancements will further enhance the capabilities of wire EDM, making it an even more powerful tool for manufacturing complex and precise components across various industries.
What is the typical cost of wire EDM services? The cost varies depending on the complexity of the part, material, and required tolerances. Contact us for a personalized quote.
What are the limitations of wire EDM? While incredibly versatile, wire EDM is limited to electrically conductive materials and can be slower than some conventional machining methods for simpler parts.
Is wire EDM environmentally friendly? Yes, the process uses deionized water as a dielectric fluid, minimizing environmental impact.
How long does the wire EDM process take? The duration varies depending on the complexity and size of the part being machined.
Can wire EDM create internal threads? No, wire EDM primarily creates through-features.
Wire EDM is a non-traditional machining process using electrical discharges to cut conductive materials.
It offers unparalleled precision and can create complex shapes impossible for conventional methods.
Wire EDM is used in a variety of industries, from aerospace to medical devices.
Choosing the right wire EDM machine depends on your specific needs and requirements.
The future of wire EDM is focused on enhancing speed, precision, and automation.
Our Fabrication Services page provides further information on our comprehensive capabilities. Contact us today to discuss your specific project requirements and how our expertise in wire EDM can help you achieve your manufacturing goals.
More details on CNC Machining can be found on our CNC Machining page.
Get the latest trends and facts about CNC fabrication from our blog.
Shenzhen Runkey Precision Technology Co. Ltd, a subsidiary of the Tensun Group, is your trusted one-stop solution for custom manufacturing from prototyping to production.Transforming your idea into reality with digital manufacturing resources,streamlined processes, expert guidance,accelerated timelines, and uncompromising quality.
©2024. CNC Fabrication All Rights Reserved.