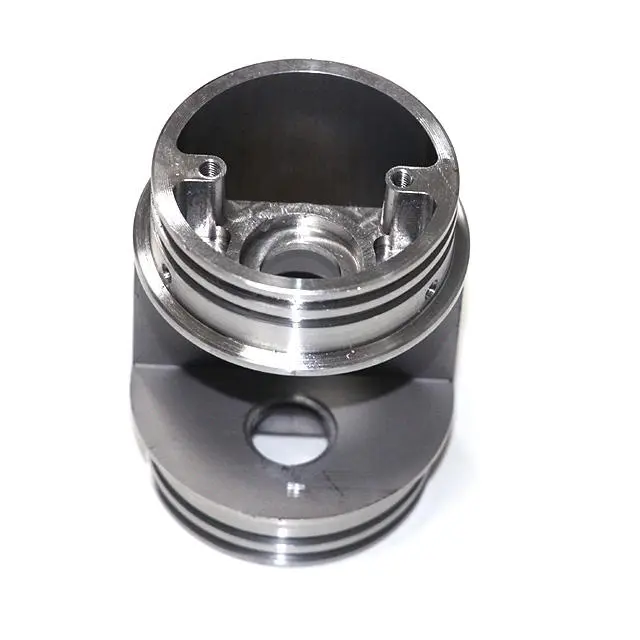
- +8615586668226
- [email protected]
- No. 30, Hongbang Industrial Park, Shenzhen
5-axis CNC machining is an advanced machining technology that offers unparalleled precision and versatility compared to traditional 3-axis machining. But what exactly sets it apart? Unlike 3-axis machines that move along the X, Y, and Z axes, a 5-axis machine has two additional rotational axes, allowing the cutting tool to approach the workpiece from any direction. This capability opens up a new realm of possibilities, enabling the creation of highly complex parts with intricate geometry and superior surface finish. I’ve seen firsthand how this technology can transform manufacturing processes, particularly in industries like aerospace and medical devices, where precision and reliability are paramount.
The decision between 3-axis and 5-axis CNC machining often comes down to the complexity of the part and the required tolerances. While 3-axis CNC is suitable for simpler designs, 5-axis machining provides unmatched capabilities for intricate parts. In my experience, opting for a 5-axis machine eliminates the need for multiple setups, which is a common requirement with 3-axis CNC machines. This not only speeds up production but also significantly reduces the chances of error, ensuring a higher level of precision and consistency. 5-axis machining capabilities allow for machining complex shapes and achieving tight tolerances that would be impossible or highly inefficient with a 3-axis setup.
Feature | 3-Axis CNC Machine | 5-Axis CNC Machine |
Axes of Movement | X, Y, Z (Linear) | X, Y, Z (Linear) + A, B or A, C or B, C (Rotational) |
Part Complexity | Simple to Moderate | Complex, Intricate |
Setups Required | Multiple for complex parts | Single or fewer setups for complex parts |
Precision | High, but limited by the number of setups | Superior, due to continuous machining and fewer setups |
Surface Finish | Good, may require secondary finishing for complex curves | Excellent, especially on contoured surfaces |
Production Time | Longer for complex parts due to multiple setups | Shorter due to reduced setup times |
Tool Wear | Higher due to potential misalignment between setups | Lower due to continuous and optimal tool orientation |
Cost | Lower initial investment | Higher initial investment, but potential savings in the long run |
Industries Commonly Used | General manufacturing, simple part production | Aerospace, Medical, Automotive, Defense, complex and intricate parts |
Precision and accuracy are the cornerstones of high-quality manufacturing, and 5-axis CNC machining excels in both. The 5-axis machining process allows the machine to approach the workpiece from virtually any angle, enabling the cutting tool to maintain an optimal position relative to the surface being machined. This capability is crucial for achieving high precision and a better surface finish, particularly on parts with complex geometry. In my work, I’ve observed that 5-axis machines deliver exceptional accuracy, consistently meeting the most demanding specifications.
The 5-axis CNC machining process reduces errors that can occur during repositioning in multiple setups.
Enhanced tool orientation ensures consistent cutting forces, contributing to tighter dimensional control.
The ability to machine closer to the cutting tool with shorter tools minimizes vibrations and improves accuracy.
A superior surface finish is not just about aesthetics; it also plays a critical role in the functionality and longevity of a part. 5-axis machining allows for a better surface quality compared to traditional 3-axis methods. Because the cutting tool can be positioned optimally relative to the workpiece, it produces smoother, more consistent cuts. This is particularly beneficial when machining curved or contoured surfaces, where maintaining a uniform surface finish can be challenging. 5-axis machining eliminates the need for manual finishing in many cases, saving both time and resources.
Absolutely! Productivity is a key consideration in any manufacturing operation, and 5-axis CNC machining offers significant advantages in this area. By minimizing the number of setups required to machine a complex part, 5-axis machines significantly reduce production time. This not only speeds up the overall manufacturing process but also reduces labor costs and machine downtime. In our plant, we’ve seen a substantial increase in throughput since implementing 5-axis technology. This reduction in cycle times allows us to take on more projects and meet tighter deadlines, ultimately boosting our overall productivity.
The ability to machine complex shapes is where 5-axis CNC machining truly shines. Traditional 3-axis machining requires multiple setups and repositioning to machine parts with intricate features, such as undercuts or complex curves. 5-axis machines provide a level of flexibility and agility that makes machining these features straightforward. The two additional axes allow the cutting tool to reach areas that would be inaccessible with a 3-axis machine. For instance, 5-axis machining enables the efficient production of aerospace components like turbine blades, which have highly complex geometry.
Tolerance is a critical factor in manufacturing, especially in industries like aerospace, medical, and defense where precision is non-negotiable. 5-axis CNC machining offers the capability to achieve extremely tight tolerances that are often impossible with traditional 3-axis CNC. The ability to machine a part in a single setup minimizes the accumulation of errors that can occur with multiple setups. Additionally, the enhanced tool orientation and stability provided by the additional axes contribute to greater dimensional accuracy. Our experience shows that 5-axis machines consistently deliver parts that meet or exceed the most stringent tolerance requirements.
The versatility of 5-axis CNC machining makes it a valuable asset across a wide range of industries. In the aerospace sector, it’s used to create complex components with stringent requirements for weight, strength, and precision. The medical device industry relies on 5-axis machining for producing intricate implants and surgical instruments. Similarly, the automotive, defense, and energy sectors all benefit from the ability to machine complex parts with high precision and efficiency. As a machining service provider, we’ve had the privilege of working with clients from all these industries, delivering customized solutions that meet their unique needs.
The world of CNC machining encompasses various types of CNC machines, each designed for specific applications. The most common distinction is based on the number of axes. 3-axis machines are the most basic, moving along the X, Y, and Z axes. 5-axis machines, as we’ve discussed, add two rotational axes, offering greater flexibility. Other variations include 4-axis machines, which have one rotational axis in addition to the three linear axes, and multi-axis machines that can have six or more axes. Choosing the right type of machine depends on the specific requirements of the project. For more info about materials used in the process, check materials.
While the initial investment in a 5-axis machine may be higher compared to a 3-axis machine, it often proves to be more cost-effective in the long run. The reduced need for multiple setups saves time and labor costs. Additionally, the ability to machine complex parts in a single setup minimizes the risk of errors, reducing scrap and rework. The superior surface finish achieved with 5-axis machining can also eliminate the need for secondary finishing operations, further reducing costs. Our experience in precision manufacturing has shown that the long-term benefits of 5-axis machining far outweigh the initial investment, making it a smart choice for businesses looking to optimize their operations. For more info about our fabrication services.
The primary advantage is the ability to machine complex geometries and achieve higher precision and better surface finishes in a single setup, reducing production time and costs.
Yes, 5-axis machining eliminates the need for multiple setups in most cases, as the cutting tool can access the workpiece from various angles.
Industries such as aerospace, medical devices, automotive, and defense benefit significantly from 5-axis machining due to its ability to produce complex and high-precision parts.
5-axis machining enables optimal tool orientation, resulting in smoother and more consistent cuts, especially on curved or contoured surfaces, compared to traditional 3-axis machining.
While the initial investment is higher, 5-axis machining can be more cost-effective in the long run due to reduced setup times, lower labor costs, and less material waste.
3-axis CNC machining is limited in its ability to machine complex geometries, often requiring multiple setups and potentially compromising precision and surface finish on intricate parts.
5-axis CNC machining offers unparalleled precision, efficiency, and versatility compared to traditional 3-axis methods.
The ability to machine complex parts in a single setup reduces production time, labor costs, and the risk of errors.
5-axis machining delivers superior surface finish, especially on contoured surfaces.
Industries like aerospace, medical, automotive, and defense greatly benefit from 5-axis machining capabilities.
While the initial investment may be higher, 5-axis machining often proves more cost-effective in the long run.
Understanding the advantages of 5-axis CNC machining is crucial for optimizing manufacturing processes and achieving superior results.
Ready to experience the transformative power of 5-axis CNC machining for your next project? Whether you’re in the aerospace, automotive, medical, or any other industry that demands high precision and complex parts, our team at CNC Fabrication Service is here to help. With our state-of-the-art 5-axis machines and extensive experience in precision manufacturing, we’re equipped to handle even the most challenging projects. Contact us today to discuss your specific needs and discover how our CNC machining services can elevate your products to new heights of quality and performance. From rapid prototyping to on-demand manufacturing, or even CNC turning, we have you covered. Let us be your trusted partner in achieving manufacturing excellence.
Get the latest trends and facts about CNC fabrication from our blog.
Shenzhen Runkey Precision Technology Co. Ltd, a subsidiary of the Tensun Group, is your trusted one-stop solution for custom manufacturing from prototyping to production.Transforming your idea into reality with digital manufacturing resources,streamlined processes, expert guidance,accelerated timelines, and uncompromising quality.
©2024. CNC Fabrication All Rights Reserved.