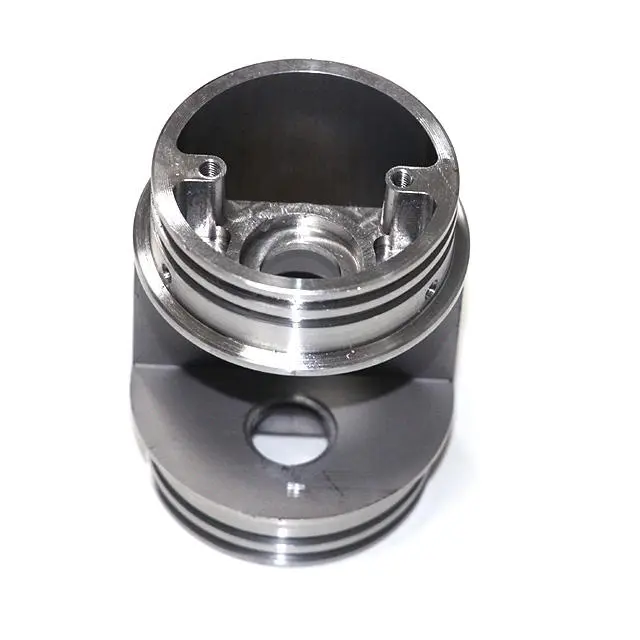
- +8615586668226
- [email protected]
- No. 30, Hongbang Industrial Park, Shenzhen
When we talk about creating precise and durable parts, the choice of material is paramount. Aluminum stands out as a remarkably versatile option for Computer Numerical Control (CNC) machine projects. But what makes it so popular? For starters, aluminum is one of the most abundant metals on Earth, making it readily available. More importantly, it boasts an impressive strength-to-weight ratio, meaning it’s strong without being overly heavy. This is crucial for applications where weight reduction is a key factor, such as in the Aerospace and Automotive industries. Furthermore, aluminum offers excellent corrosion resistance, naturally forming a protective layer of aluminum oxide when exposed to air. This natural defense mechanism makes aluminum parts exceptionally durable, even in harsh environments.
Beyond its inherent properties, the machinability of aluminum is a significant advantage. It’s generally easier to machine compared to many other metals like steel, which translates to faster production times and reduced wear on cutting tool equipment. This ease of processing doesn’t compromise precision; in fact, with the right techniques, aluminum can be machined to incredibly tight tolerances, making it suitable for intricate designs required in Medical Devices and Electronics. As cnc fabrication serive Manufacturing plants for products, we understand the importance of choosing materials that offer both performance and ease of manufacturing, and aluminum consistently delivers on both fronts.
The versatility of aluminum cnc machined parts stems from a combination of its inherent qualities and the adaptability of the CNC machining process itself. Think about the demands placed on components in various industries. In the Aerospace and Aviation sector, lightweight yet robust materials are crucial for fuel efficiency and safety. Aluminum, particularly specific aluminum alloys, meets these needs perfectly. Similarly, the Automotive industry utilizes aluminum components extensively to reduce vehicle weight, improving performance and fuel economy. Even in seemingly disparate fields like Art and Design, the surface finish achievable with aluminum machining allows for aesthetically pleasing and durable creations.
Consider the corrosion resistance again. This property makes aluminum parts ideal for applications exposed to moisture or harsh chemicals, such as equipment used in the Food and Packaging and Pharmaceuticals industries. The fact that aluminum is highly recyclable also aligns with increasing environmental consciousness, making it a sustainable material choice. Moreover, different aluminum grades offer varied properties. For example, aluminum 6061 is a very versatile alloy known for its good strength and machinability, while 7075 aluminum offers even higher strength for more demanding applications. As experts in precision machining, we can help you select the optimal aluminum alloy for your project, ensuring your parts meet the exact performance requirements.
The impact of aluminum cnc machining spans a vast array of industries, each leveraging its unique benefits for specific applications. As mentioned, Aerospace and Aviation rely heavily on aluminum for airframe components, engine parts, and interior elements due to its strength-to-weight ratio. The Automotive sector uses aluminum for engine blocks, wheels, and body panels to enhance vehicle performance and fuel efficiency. In the realm of Medical Devices, the biocompatibility and sterilizability of certain aluminum alloys make them suitable for surgical instruments and equipment housings.
The Electronics industry benefits from aluminum’s excellent thermal conductivity, using it for heat sinks and enclosures to manage heat dissipation in electronic devices. Industrial Equipment manufacturers utilize aluminum for machine components and structural elements where durability and lightweighting are important. Even the Consumer Products market sees aluminum in everything from gadget housings to sporting goods. The Energy and Renewable Energy sector utilizes aluminum in solar panel frames and wind turbine components due to its corrosion resistance and lightweight nature. The emerging field of Robotics benefits from the ability to create complex and lightweight robotic arms and chassis using aluminum cnc machining. The precision and versatility of the process also make it invaluable for Custom Projects/Prototyping, allowing for rapid iteration and the creation of bespoke components. Our experience as a cnc machine shop allows us to serve these diverse needs effectively.
Choosing aluminum for cnc machining brings a multitude of advantages to the manufacturing process. Firstly, its inherent machinability translates to faster production cycles. Aluminum is easier to machine than many other machining materials, meaning cutting tool wear is reduced, and higher cutting speeds can be employed. This directly impacts production costs and lead times, making it a cost-effective option for many projects. The excellent surface finish achievable with aluminum machining is another significant benefit. Parts can be produced with smooth, aesthetically pleasing surfaces, often reducing the need for additional finishing processes.
The corrosion resistance of aluminum is a key advantage, ensuring the longevity and reliability of the final machined part. This is especially crucial for components operating in harsh environments. Furthermore, the strength-to-weight ratio of aluminum allows for the creation of strong yet lightweight parts, which is vital in industries where weight reduction is a priority. The recyclability of aluminum also makes it an environmentally responsible material choice, aligning with sustainability goals. Compared to machining steels, aluminum often requires less energy to process, contributing to a smaller environmental footprint. These benefits of aluminum cnc machining make it a compelling choice for a wide range of manufacturing applications.
While pure aluminum is relatively soft and less suitable for many structural applications, aluminum alloys, which combine aluminum with other elements, offer enhanced properties. Several common aluminum alloys are particularly well-suited for cnc machining. Aluminum 6061 is perhaps the most versatile and widely used alloy. It boasts good strength, excellent corrosion resistance, and is relatively easy to machine. This makes it a go-to choice for a broad range of applications.
Another popular option is aluminum 7075. This alloy offers significantly higher strength than 6061, making it suitable for demanding applications where structural integrity is paramount, such as in Aerospace components. However, it’s generally considered more difficult to machine than 6061. Aluminum 2024 is another high-strength alloy, often used in aerospace applications, but it has lower corrosion resistance compared to 6061 and 7075. Aluminum 5083 is known for its excellent corrosion resistance, particularly in marine environments, and good weldability. When selecting aluminum grades for cnc machining, factors like required strength, corrosion resistance, weldability, and machinability must be considered. Our machining expertise allows us to guide you in choosing the best aluminum for your specific needs.
The superior machinability of aluminum is a game-changer in the manufacturing process. It means that cutting tools can remove material more quickly and efficiently compared to harder metals. This results in faster cycle times, allowing for a higher volume of aluminum parts to be produced in a given timeframe. Furthermore, the lower cutting forces required when machine aluminum reduce wear and tear on cnc machine tools, extending their lifespan and reducing maintenance costs. This efficiency also translates to lower energy consumption per machined part.
Because aluminum is easier to machine, achieving tight tolerances and intricate geometries is often more straightforward. This reduces the likelihood of errors and the need for secondary machining operations. The excellent chip formation characteristics of most aluminum alloys also contribute to smoother machining and easier chip removal, further enhancing efficiency. Compared to materials that are difficult to machine, like some stainless steels or titanium alloys, aluminum offers a significant advantage in terms of processing speed and cost-effectiveness. This streamlined machining process allows us to deliver high-quality cnc machined parts efficiently to our clients.
Aluminum CNC machining is renowned for its ability to achieve incredibly high levels of precision. Using sophisticated cnc machine tools and skilled operators, we can consistently produce aluminum parts that meet very tight tolerances, often measured in thousandths of an inch. This precision machining is crucial for applications where parts must fit together perfectly and function flawlessly, such as in Medical Devices, Electronics, and Aerospace components. The stability of modern cnc machines, combined with the predictable nature of aluminum’s behavior under machining conditions, allows for repeatable accuracy.
Whether it’s intricate internal features, precise hole locations, or critical surface finishes, cnc milling and cnc turning involves carefully controlled material removal to create the desired shape and dimensions. The digital nature of the CNC process ensures that each machined part conforms to the design specifications with minimal variation. This level of precision is not easily achievable with traditional machining methods. The ability to consistently produce aluminum parts with such accuracy is a key reason why cnc machining is the preferred method for many demanding applications.
When it comes to shaping aluminum into a desired form, several cnc machining processes come into play. CNC milling is a versatile process that uses rotating cutting tools to remove material from a block of material. It’s ideal for creating complex shapes, pockets, and contours. CNC turning involves rotating the aluminum material while a stationary cutting tool removes material, perfect for creating cylindrical and conical shapes. CNC drilling is used to create precise holes.
Beyond these fundamental processes, there are more specialized techniques like 5-axis cnc machineing, which allows for even more complex geometries to be created by moving the cutting tool and the workpiece simultaneously. Wire EDM (Electrical Discharge Machining) can be used for creating intricate shapes and features in aluminum using electrical discharges. Surface finishing services, such as anodizing or powder coating, can be applied to aluminum cnc machined parts to enhance their corrosion resistance, durability, and aesthetics. Our comprehensive range of machining services ensures we can meet the diverse needs of your cnc machining project.
Choosing the right machining service provider is critical for the success of your project. Experienced manufacturing plants bring a wealth of knowledge and expertise to the table. We understand the nuances of machining aluminum parts, including selecting the appropriate aluminum alloy, optimizing cutting parameters, and ensuring the desired surface finish. Our investment in advanced cnc machine technology and skilled machinists ensures high-quality results and consistent precision.
Partnering with us means you benefit from our experience in handling diverse projects across various industries, from Aerospace to Medical Devices. We can offer valuable insights into design for manufacturability, helping to optimize your designs for efficient and cost-effective production. Furthermore, established manufacturing plants have robust quality control processes in place to ensure that your aluminum cnc machined parts meet the required specifications and standards. We can handle projects from initial prototyping to full-scale production, providing a seamless and reliable manufacturing solution. As your trusted partner, we are committed to delivering aluminum parts that meet your exact needs and exceed your expectations.
The advantages of aluminum cnc machining are clear. From its impressive strength-to-weight ratio and excellent corrosion resistance to its superior machinability and the high levels of precision achievable, aluminum stands out as an exceptional material for a wide range of applications. Whether you’re in the Aerospace, Automotive, Medical Devices, Electronics, or any other industry requiring precise and durable components, aluminum cnc machining offers a compelling solution.
As a leading cnc fabrication serive Manufacturing plants for products, we are ready to help you leverage the power of aluminum cnc machining to bring your product ideas to life. Our expertise, advanced technology, and commitment to quality ensure that you receive top-notch aluminum cnc parts that meet your exact specifications. Don’t hesitate to explore how our machining services can benefit your next project. Contact us today to discuss your specific needs and discover how we can help you achieve manufacturing excellence.
How does the cost of aluminum CNC machining compare to other materials?
Generally, aluminum is a cost-effective material for cnc machining due to its availability and machinability. While the cost of the raw aluminum material itself might fluctuate, the faster machining times and reduced tool wear often lead to overall cost savings compared to machining materials like stainless steel or titanium.
What are the typical lead times for aluminum CNC machined parts?
Lead times can vary depending on the complexity of the part, the quantity ordered, and our current workload. However, the inherent machinability of aluminum often allows for faster turnaround times compared to projects involving more difficult-to-machine materials. We strive to provide efficient and timely delivery for all our clients.
Can aluminum CNC machining be used for prototyping?
Absolutely! Aluminum is an excellent material for prototyping due to its ease of machining and relatively lower cost. Rapid Prototyping using aluminum cnc machining allows for quick iterations and design adjustments, making it ideal for testing and refining product designs before moving to full-scale production.
What design considerations are important for aluminum CNC machined parts?
When designing parts for aluminum cnc machining, it’s important to consider factors like wall thickness, internal radii, and feature complexity. Consulting with our experienced engineers early in the design process can help optimize your design for manufacturability and ensure the most cost-effective and efficient production.
Is aluminum CNC machining suitable for high-volume production?
Yes, aluminum cnc machining is well-suited for both low-volume and high-volume production runs. The automation and precision of the CNC process allow for consistent quality and efficient production, regardless of the quantity required.
What kind of surface finishes can be achieved on aluminum CNC machined parts?
A wide range of surface finishes can be achieved on aluminum cnc machined parts, including smooth, as-machined finishes, as well as various post-processing options like anodizing, powder coating, and painting, which can enhance both the aesthetic appeal and the corrosion resistance of the parts.
Get the latest trends and facts about CNC fabrication from our blog.
Shenzhen Runkey Precision Technology Co. Ltd, a subsidiary of the Tensun Group, is your trusted one-stop solution for custom manufacturing from prototyping to production.Transforming your idea into reality with digital manufacturing resources,streamlined processes, expert guidance,accelerated timelines, and uncompromising quality.
©2024. CNC Fabrication All Rights Reserved.