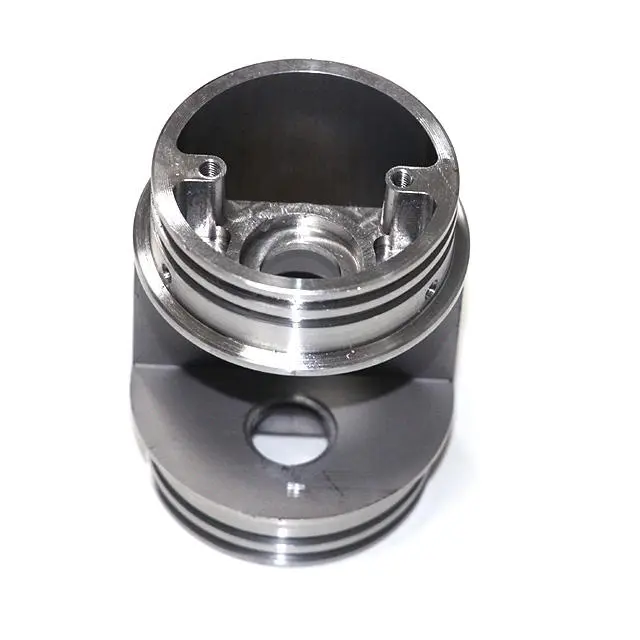
- +8615586668226
- [email protected]
- No. 30, Hongbang Industrial Park, Shenzhen
A 5-axis CNC machine is a precision engineering tool that can move a part or a cutting tool along five different axes simultaneously. Unlike a traditional 3-axis machine that moves along the X, Y, and Z axes, a 5-axis machine adds two rotational axes (typically A and B or A and C), allowing for the creation of incredibly complex shapes and contours. This capability is pivotal in industries like aerospace and medical, where precision is non-negotiable.
The operation of a 5-axis CNC machine involves a sophisticated coordination of movements. The workpiece is secured, and the machine’s computer-controlled system guides the cutting tool along the programmed path. This tool can approach the part from any angle, thanks to the two additional rotational axes. The result is a highly efficient process that can produce complex parts with exceptional accuracy and minimal setup time. The ability to tilt and rotate the tool allows for undercutting and machining of intricate features that would be impossible with 3-axis machines. As a machinist with years of experience at CNC Fabrication Services, I’ve witnessed first-hand how these machines transform raw materials into precision components.
Choosing 5-axis machining services over traditional methods like 3-axis machining offers significant advantages, particularly when dealing with complex parts or components. The main advantage lies in the ability of 5-axis machines to approach the workpiece from multiple angles in a single setup. This means fewer setups, reduced lead time, and lower costs. In contrast, traditional 3-axis machining often requires multiple setups to machine different sides of a part, increasing the risk of errors and inconsistencies.
Another critical reason to opt for 5-axis machining services is the enhanced precision and quality of the surface finish. With its ability to move the cutting tool along five axes, a 5-axis machine can achieve tighter tolerances and smoother finishes. This is particularly beneficial in industries like aerospace, where even the slightest deviation can compromise the integrity of a component. Machine parts produced with 5-axis technology have a superior quality that meets the stringent requirements of demanding applications. From my experience, this level of precision is unmatched by traditional methods.
There are several types of 5-axis CNC machines, each designed to cater to specific machining needs. The most common types include the trunnion style, where the table rotates to provide the two additional axes, and the swivel-rotate style, where the tool head swivels and rotates. Each type has its own set of advantages, depending on the application.
Here’s a table outlining the main types of 5-axis CNC machines and their characteristics:
Type | Description | Advantages | Best For |
Trunnion Style | The table rotates to provide two additional axes (A and B or A and C). | Excellent for heavy parts, provides stability. | Aerospace, heavy industrial components |
Swivel-Rotate | The tool head swivels and rotates to provide the two additional axes. | Greater flexibility, can reach difficult angles. | Medical devices, intricate parts |
Hybrid | Combines features of both trunnion and swivel-rotate styles. | Versatility, can handle a wide range of parts. | Versatile applications, complex shapes, varied industries |
Gantry | The machine structure moves along a fixed bed, with the tool head providing the additional movements. | Large-scale parts, high stability. | Large aerospace parts, automotive frames |
Selecting the right type of 5-axis CNC machine depends on factors such as part size, complexity, material, and required tolerance. At CNC Fabrication Services, we have a range of machines to meet diverse client needs, ensuring optimal results for each project. Each machine is a testament to our commitment to quality.
5-axis machining significantly improves accuracy and surface finish compared to traditional methods. The ability to move the cutting tool along five axes allows it to maintain optimal cutting conditions throughout the machining process. This minimizes tool deflection and vibration, resulting in tighter tolerances and a smoother surface finish. In 5-axis machining, the tool can be positioned closer to the cutting surface, reducing the need for long, slender tools that are prone to vibration.
Moreover, 5-axis machining allows for the production of complex shapes and contours with high precision. The machine can access hard-to-reach areas and create intricate features that would be challenging or impossible to achieve with 3-axis or even 4 axis machines. This capability is particularly valuable in industries such as medical devices and aerospace, where precision and surface quality are critical. With 5-axis machining, we can achieve exceptional accuracy, ensuring that each part meets the most demanding specifications, including those needed for aerospace applications.
The benefits of 5-axis CNC machining are numerous and impactful. One of the primary advantages is the reduction in setup time. Since the machine can access multiple sides of a part in a single setup, there’s no need to reposition the workpiece, saving valuable time and reducing labor costs. This efficiency translates to faster turnaround times and increased productivity, an advantage highlighted in our CNC Solutions.
Another key benefit is the ability to create complex shapes and geometries. 5-axis machining excels at producing parts with intricate contours, arcs, and angles that are difficult or impossible to achieve with traditional machining methods. This capability opens up new design possibilities and allows for the production of highly customized components. Additionally, 5-axis machining enhances tool life by maintaining optimal cutting conditions and reducing wear and tear. The advantages also extend to improved accuracy, superior surface finish, and the ability to machine hard-to-reach areas, making it an invaluable tool in modern manufacturing.
5-axis machining is compatible with a wide range of materials, including metals, plastics, composites, and even wood. The versatility of 5-axis CNC machines allows them to handle materials with varying degrees of hardness and machinability. Some of the most common materials used in 5-axis machining include aluminum, stainless steel, titanium, and high-performance plastics like PEEK and Ultem.
The choice of material depends on the specific application and the desired properties of the finished part. For example, aerospace applications often require lightweight yet strong materials like titanium or aluminum alloys, while medical devices may use biocompatible materials like surgical-grade stainless steel or PEEK. At CNC Fabrication Services, we have experience machining a wide variety of materials and can provide expert guidance on material selection to ensure optimal results, including specialized materials for aerospace parts. To learn more about compatible materials, visit our detailed guide on Materials.
Several industries benefit significantly from 5-axis CNC machining capabilities. The aerospace industry is one of the primary beneficiaries, as 5-axis machining is ideal for producing complex, lightweight components with high precision and tight tolerances. Parts like turbine blades, engine components, and structural elements for aircraft are commonly manufactured using 5-axis technology, a fact we proudly demonstrate in our work in the Aerospace sector.
The automotive industry also relies on 5-axis machining for producing high-performance engine parts, molds for body panels, and custom components. The medical devices industry uses 5-axis machining to create intricate surgical instruments, implants, and prosthetic components. Other industries that benefit from 5-axis machining include energy, defense, electronics, and any sector requiring complex parts with high precision and quality. The versatility of 5-axis machining makes it an indispensable tool across a wide range of applications, from aerospace applications to consumer products.
One of the most significant advantages of 5-axis machining is the ability to complete a part in a single setup. This capability dramatically reduces lead time compared to traditional machining methods that require multiple setups. In 3-axis machining, the workpiece needs to be repositioned multiple times to access different sides, which is time-consuming and increases the risk of errors.
With 5-axis machining, the machine can access five sides of a part in a single setup, thanks to the two additional rotational axes. This eliminates the need for manual intervention to reposition the part, saving valuable time and reducing labor costs. The reduction in setup time translates to faster turnaround times, increased productivity, and lower overall costs, making it a preferred choice for time-sensitive projects. This efficiency is a core principle of our On Demand Manufacturing services.
This single setup capability significantly improves efficiency and reduces lead time, which is why at CNC Fabrication Services we always suggest our customers to use 5-axis machining for complex projects.
Choosing the right 5-axis CNC machining service provider is crucial for ensuring the success of your project. Several factors should be considered, including the provider’s experience, capabilities, equipment, quality control processes, and customer service. It’s important to select a provider with a proven track record of delivering high-quality parts on time and within budget.
When evaluating potential providers, consider their experience in your specific industry and with similar projects. Look for a provider with state-of-the-art 5-axis CNC machines and a team of skilled machinists and engineers. Additionally, ensure that the provider has robust quality control processes in place to guarantee the accuracy and consistency of the parts. Customer service is another important factor, as you want a provider who is responsive, communicative, and committed to meeting your needs. At CNC Fabrication Services, we pride ourselves on our expertise, cutting-edge technology, stringent quality control, and exceptional customer service.
5-axis machining excels at handling complex shapes and geometries that are difficult or impossible to achieve with traditional machining methods. The ability to move the cutting tool along five axes simultaneously allows the machine to create intricate contours, undercuts, and other complex features with high precision. 5-axis machining is particularly well-suited for parts with complex geometries, such as those found in aerospace, medical, and automotive applications.
The two additional rotational axes in a 5-axis machine enable the tool to access hard-to-reach areas and create features that would require multiple setups or specialized tooling in 3-axis machining. This capability opens up new design possibilities and allows for the production of highly customized and intricate components. 5-axis machining can also create smooth, flowing curves and surfaces, enhancing the aesthetics and functionality of the part. Whether it’s a complex turbine blade for an aircraft engine or a custom medical implant, 5-axis machining provides the precision and flexibility needed to bring even the most challenging designs to life, fulfilling diverse machining needs.
What is the main difference between 3-axis and 5-axis machining?
The main difference is that 3-axis machining moves the tool along the X, Y, and Z linear axes, while 5-axis machining adds two rotational axes (A and B or A and C), allowing the tool or part to rotate. This enables 5-axis machines to create more complex shapes and access hard-to-reach areas.
Can 5-axis machining produce any shape?
While 5-axis machining is incredibly versatile, it does have limitations. Extremely complex or intricate internal features may still require specialized techniques like EDM. However, for most external complex geometries, 5-axis machining is highly capable.
What tolerances can 5-axis machining achieve?
5-axis machining can achieve very tight tolerances, often in the range of +/- 0.005 mm or better, depending on the machine, material, and part geometry. This makes it suitable for high-precision applications in industries like aerospace and medical devices.
Is 5-axis machining more expensive than 3-axis machining?
Initially, 5-axis machining may have higher setup costs due to the complexity of the machines and programming. However, the reduced setup time, increased efficiency, and ability to produce complex parts in a single setup often result in lower overall costs, especially for complex or high-volume production runs.
How does 5-axis machining benefit the aerospace industry?
5-axis machining is crucial in the aerospace industry for producing lightweight, high-strength components with complex geometries. It allows for the creation of intricate parts like turbine blades, engine components, and structural elements with exceptional accuracy and surface finish, meeting the industry’s stringent quality standards.
What is simultaneous 5-axis machining?
Simultaneous 5-axis machining refers to the ability of a 5-axis CNC machine to move all five axes simultaneously in a coordinated manner. This allows for the creation of very complex shapes and contours that would be impossible to achieve with indexed or positional 5-axis machining, where the rotational axes are moved one at a time.
5-axis CNC machining offers unparalleled precision, efficiency, and versatility.
It enables the creation of complex shapes and geometries that are difficult or impossible to achieve with traditional methods.
5-axis machining reduces setup time, increases productivity, and enhances tool life.
Industries like aerospace, automotive, and medical devices benefit significantly from 5-axis machining capabilities.
Choosing the right 5-axis CNC machining service provider is crucial for project success.
5-axis machining is a powerful tool for innovation and pushing the boundaries of manufacturing.
By understanding the capabilities and benefits of 5-axis CNC machining, you can make informed decisions about your manufacturing processes and leverage this advanced technology to achieve superior results. At CNC Fabrication Services, we are committed to providing our clients with the highest quality 5-axis machining services to meet their unique needs and drive their success. Our expertise in Precision Machining ensures that every project is executed with the utmost care and precision.
Get the latest trends and facts about CNC fabrication from our blog.
Shenzhen Runkey Precision Technology Co. Ltd, a subsidiary of the Tensun Group, is your trusted one-stop solution for custom manufacturing from prototyping to production.Transforming your idea into reality with digital manufacturing resources,streamlined processes, expert guidance,accelerated timelines, and uncompromising quality.
©2024. CNC Fabrication All Rights Reserved.