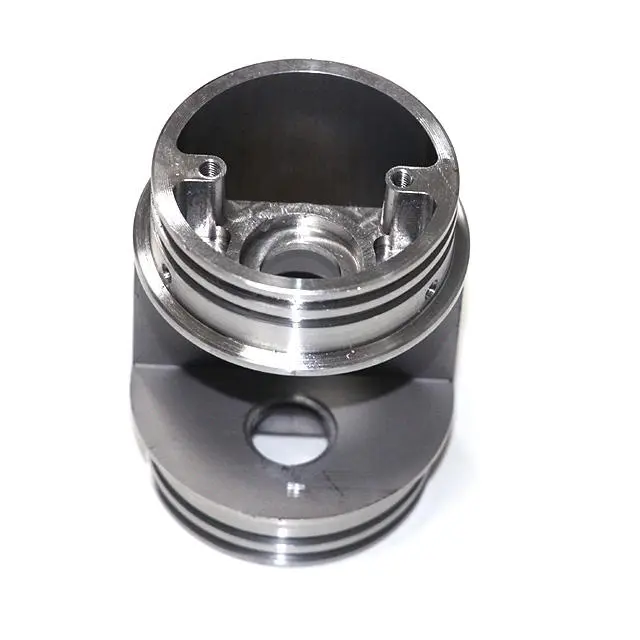
- +8615586668226
- [email protected]
- No. 30, Hongbang Industrial Park, Shenzhen
Wire EDM, or wire electrical discharge machining, is a machining process that uses a thin, single-strand metal wire, typically brass, along with deionized water to cut through conductive material. The wire electrode is continuously fed from a spool and guided along a programmed path. I want to emphasize, as a leading provider of CNC fabrication services, that this process is incredibly precise. The machine generates a series of rapid electrical sparks between the wire and the workpiece. These sparks erode the material, creating a precise cut along the desired path. The deionized water acts as a dielectric, controlling the spark and flushing away the eroded particles.
The wire EDM process is particularly effective for creating complex shapes and intricate designs with extremely tight tolerances. It’s a go-to method for production parts that require high accuracy, and it can even handle hard materials that might be challenging for conventional cutting tools. For instance, our wire EDM services have been crucial in producing components for the aerospace industry, where precision is non-negotiable.
Wire EDM can provide us with many benefits for example:
High Precision: Wire EDM achieves exceptional accuracy, with tolerances as tight as ±0.0001 inches.
Complex Shapes: The process can create intricate and detailed geometries that are difficult or impossible to achieve with traditional machining methods.
Hard Materials: Wire EDM can easily cut through hardened steel, titanium, and other tough materials.
One of the remarkable aspects of wire EDM is its versatility in handling a wide range of conductive materials. As a specialist in this field, I’ve seen firsthand how this technology can effectively machine everything from common metals to exotic alloys.
Here’s a detailed look at some of the materials that can be processed using wire EDM:
Steel: All types of steel, including tool steel, stainless steel, and high-speed steel, are suitable for wire EDM. This makes it ideal for creating tooling, dies, and molds.
Aluminum: While aluminum is softer than steel, it can still be effectively machined with wire EDM, particularly for intricate parts.
Titanium: This lightweight yet strong material, often used in aerospace applications, is a perfect candidate for wire EDM due to its high melting point and hardness.
Copper and Brass: These conductive materials are commonly used in electrical components and are easily machined using wire EDM.
Carbide: Known for its extreme hardness, carbide is often used in cutting tools and wear-resistant parts. Wire EDM is one of the few methods that can efficiently machine this tough material.
Superalloys: Materials like Inconel and Hastelloy, used in high-temperature and corrosive environments, can be precisely cut using wire EDM.
The ability of wire EDM to handle such a diverse range of materials, regardless of their hardness, makes it an invaluable tool in many industries.
Wire EDM offers numerous advantages that make it a preferred choice for many manufacturing applications. From my experience, the benefits of wire EDM extend beyond just precision. This technology offers a unique combination of capabilities that are hard to match with other machining methods.
Wire EDM offers many advantages, below you can find a list of them:
No Cutting Forces: Unlike conventional machining, wire EDM involves no physical contact between the cutting tool and the workpiece, eliminating cutting forces and the risk of distortion, especially crucial for delicate parts. This stress-free machining is ideal for producing delicate or thin-walled parts.
Burr-Free Cuts: The wire EDM process produces clean, burr-free edges, reducing or eliminating the need for secondary finishing operations, which saves us time and money!
Exceptional Surface Finish: With wire EDM, you can achieve a smooth surface finish, often eliminating the need for additional polishing or grinding.
Versatility: As mentioned earlier, wire EDM can handle a wide range of conductive materials, including hardened steel, exotic alloys, and even stacked materials.
Automation: Modern wire EDM machines are highly automated and can run unattended for extended periods, increasing productivity and reducing labor costs.
Complex Geometries: The process excels at creating intricate shapes, sharp corners, and complex internal features that would be challenging or impossible with conventional methods.
Tight Tolerances: Wire EDM can consistently achieve tolerances as tight as ±0.0001 inches, making it ideal for precision components.
While wire EDM is a form of electrical discharge machining, it differs significantly from conventional EDM (also known as sinker EDM or ram EDM). Understanding these differences, as well as how wire EDM stacks up against other machining techniques like laser cutting, is crucial for selecting the right process for a specific application.
Here’s a comparison table to highlight the key distinctions:
Feature | Wire EDM | Sinker EDM | Laser Cutting |
Cutting Tool | Thin wire electrode | Shaped electrode, typically graphite or copper | Focused laser beam |
Process | Erodes material with sparks between a continuously fed wire and the workpiece | Erodes material with sparks between a shaped electrode and the workpiece | Melts, burns, or vaporizes material using a high-powered laser |
Shapes | Primarily used for 2D and simple 3D shapes, excels at creating intricate contours and profiles, cutting through parts | Creates complex 3D shapes, cavities, and blind features, commonly used for molding and creating complex internal features | Typically used for cutting sheet metal, can create complex 2D shapes |
Material Removal | Slower material removal rate compared to sinker EDM | Faster material removal rate, especially for roughing operations | Can have a high material removal rate for thin materials, but can be slower for thicker sections |
Surface Finish | Typically produces a better surface finish | Can produce a good surface finish, but may require additional finishing steps | Produces a relatively clean cut, but the heat-affected zone may require post-processing in some cases |
Material Range | Conductive materials only | Conductive materials only | Wide range of materials, including non-conductive materials like plastics and wood, but may have limitations with metals |
Tolerance | Extremely tight tolerances, typically ±0.0001 inches | Tight tolerances, but generally not as precise as wire EDM, typically ±0.001 inches | Good tolerances, but may not be as precise as EDM for very fine features |
Tool Wear | Minimal wire wear | Electrode wear can be significant, requiring redressing or replacement | Minimal tool wear |
Applications | Cutting intricate shapes, punches, dies, extrusion dies, aerospace components, medical devices | Creating molds, dies, complex cavities, and features in hardened materials | Sheet metal cutting, engraving, marking, prototyping |
Cost | Generally higher initial investment, but can be cost-effective for complex parts and small to medium production runs | Can be less expensive than wire EDM for simpler shapes, but electrode costs can be significant | Can be cost-effective for high-volume production, but the initial investment can be high |
Automation | Highly automated, can run unattended for extended periods | Can be automated, but may require more operator intervention for electrode changes | Highly automated, suitable for continuous production |
Limitations | Limited to conductive materials, slower material removal rate | Electrode wear and cost, limited to conductive materials, may require secondary finishing | Limited to 2D shapes, heat-affected zone, may have difficulty with reflective or thick materials |
The unique capabilities of wire EDM make it an ideal solution for a variety of applications across numerous industries. In my role, I’ve seen this technology used in everything from creating complex parts for aerospace to producing intricate medical devices.
Here are some of the most common applications of wire EDM:
Tool and Die Making: Wire EDM is extensively used to create precision punches, dies, and molds for various manufacturing processes.
Aerospace Components: The ability to machine hard materials with high precision makes wire EDM perfect for producing intricate parts for aircraft and spacecraft.
Medical Devices: Wire EDM is used to create small, complex components for medical implants, instruments, and diagnostic equipment. At CNC Fabrication, we have been producing medical components, which you can explore more on our Medical Devices page.
Electronics: Wire EDM can produce intricate parts for connectors, heat sinks, and other electronic components.
Prototype Development: Wire EDM is often used to quickly and accurately create prototypes for testing and design validation.
Micro-Machining: The process is capable of creating extremely small features and parts, making it suitable for micro-machining applications.
Gear Cutting: Wire EDM can produce high-precision gears with complex tooth profiles.
The use of deionized water in wire EDM is a critical aspect of the process, and it’s something that often sparks curiosity. I can tell you from experience that the purity of the water plays a vital role in the success of the EDM operation.
Here’s why deionized water is essential:
Dielectric Properties: Deionized water acts as a dielectric fluid, meaning it’s a poor conductor of electricity under normal circumstances. This allows the voltage to build up between the wire and the workpiece until a spark can jump the gap.
Controlled Sparking: The dielectric properties of the water help control the sparking process by providing a consistent breakdown voltage. This ensures that the sparks occur predictably and at the desired intensity.
Flushing: As the sparks erode the material, the deionized water acts as a flushing agent, carrying away the microscopic particles of debris created during the cutting process. This keeps the cutting zone clean and prevents the debris from interfering with the sparking process.
Cooling: The water also serves as a coolant, dissipating the heat generated by the sparks and preventing thermal damage to the workpiece and the wire.
The purity of the water is crucial because any impurities or dissolved minerals can alter its dielectric properties, leading to inconsistent sparking and potentially affecting the quality of the cut. That’s why wire EDM machines typically have sophisticated water filtration and deionization systems to maintain the required water purity.
A wire EDM machine is a complex piece of equipment with numerous components working together to achieve precise cuts. I can confidently say that understanding these components is essential for anyone operating or maintaining a wire EDM machine.
Here are the key components:
Wire Feed System: This system stores and continuously feeds the wire electrode from a spool through the machine.
Wire Guides: These precision guides ensure that the wire is accurately positioned and maintains the correct tension as it moves through the workpiece.
Power Supply: The power supply generates the high-voltage electrical pulses that create the sparks between the wire and the workpiece.
Dielectric System: This system filters, deionizes, and circulates the deionized water used in the cutting process.
Work Table: The workpiece is mounted on the work table, which can be moved in multiple axes to create the desired cut path.
CNC Control Unit: The brain of the machine, the CNC control unit, reads the programmed instructions and controls all aspects of the machining process, including wire movement, spark generation, and water flow.
Automatic Wire Threading (AWT): Many modern wire EDM machines feature AWT, which automatically threads the wire through the workpiece, reducing setup time and increasing efficiency.
CNC (Computer Numerical Control) plays a pivotal role in modern wire EDM operations. In fact, I’d say that CNC technology has revolutionized wire EDM, transforming it from a manual process into a highly automated and precise machining method.
Here’s how CNC is integrated into wire EDM:
Path Programming: CNC allows operators to program complex cutting paths using CAD/CAM software. These programs define the precise movements of the wire and the workpiece, enabling the creation of intricate shapes and features.
Motion Control: The CNC control unit precisely controls the movement of the work table and the wire feed system, ensuring that the wire follows the programmed path with extreme accuracy.
Spark Control: CNC also controls the power supply, adjusting the voltage, current, and pulse duration to optimize the sparking process for different materials and cutting conditions.
Automation: CNC enables a high degree of automation in wire EDM. Once the program is loaded and the workpiece is set up, the machine can run unattended for extended periods, significantly increasing productivity.
Adaptive Control: Some advanced CNC wire EDM machines feature adaptive control, which automatically adjusts the cutting parameters in real-time based on the conditions in the cutting zone. This helps to optimize cutting speed, accuracy, and wire life.
The integration of CNC technology has made wire EDM a more efficient, precise, and reliable process, capable of producing highly complex parts with minimal operator intervention.
Selecting the appropriate wire electrode is a critical decision in wire EDM, and it’s one that I always advise clients to consider carefully. The choice of wire can significantly impact cutting speed, accuracy, surface finish, and overall cost.
Here are some factors to consider when choosing a wire electrode:
Material: Brass is the most common wire material due to its good balance of conductivity, tensile strength, and cost. However, other materials like coated wires (e.g., zinc-coated, diffusion-annealed) are used for specific applications. Coated wires can offer faster cutting speeds and improved surface finish.
Diameter: The wire diameter typically ranges from 0.004 to 0.012 inches. Smaller diameter wires allow for finer cuts and tighter corners but may have slower cutting speeds.
Tensile Strength: Higher tensile strength wires are more resistant to breakage, especially when cutting thick materials or using aggressive cutting parameters.
Conductivity: The conductivity of the wire affects the efficiency of the sparking process. Higher conductivity generally leads to faster cutting speeds.
Application: The specific application and the material being cut will also influence the choice of wire. For example, hard materials may require a wire with higher tensile strength, while cutting thick sections may benefit from a coated wire for faster cutting.
Choosing the right wire often involves balancing various factors, and it may require some experimentation to find the optimal wire for a particular application.
Wire EDM technology continues to evolve, driven by the demand for ever-increasing precision, efficiency, and automation. As someone deeply involved in this field, I’m excited about the advancements that are shaping the future of wire EDM.
Here are some key trends to watch:
Increased Automation: We can expect to see even greater levels of automation in wire EDM, with features like automatic wire changing, advanced process monitoring, and integration with robotic systems.
Improved Cutting Speeds: Ongoing research into new wire materials, coatings, and power supply technologies is leading to faster cutting speeds without compromising accuracy.
Enhanced Precision: The push for even tighter tolerances and finer features is driving improvements in machine design, motion control, and spark generation.
Micro-EDM: The miniaturization trend is fueling the development of micro-EDM machines capable of creating incredibly small features and parts.
Hybrid Machining: Combining wire EDM with other processes, such as milling or grinding, in a single machine is becoming more common, offering greater flexibility and efficiency.
Artificial Intelligence (AI): AI and machine learning are starting to be used in wire EDM for process optimization, predictive maintenance, and adaptive control.
Industry 4.0 Integration: Wire EDM machines are increasingly being integrated into smart factories, with data connectivity and real-time monitoring capabilities.
These advancements promise to make wire EDM an even more powerful and versatile machining method, capable of meeting the evolving needs of industries that demand the highest levels of precision and quality. For example, we are exploring the integration of 5-axis wire EDM to further expand our capabilities in producing complex geometries. You can learn more about this advanced technique on our 5 Axis CNC Machining page.
What is the smallest hole that can be drilled using wire EDM?
With specialized hole drilling EDM or small hole EDM techniques, holes as small as 0.004 inches (0.1 mm) in diameter can be achieved. This capability is particularly useful in micro-machining applications and for creating intricate features in small parts.
Can wire EDM cut non-conductive materials?
No, wire EDM is specifically designed for conductive materials. The process relies on the electrical conductivity of the workpiece to complete the electrical circuit and generate the sparks necessary for material removal. For non-conductive materials, other methods like laser cutting might be more suitable.
How long does a wire EDM process typically take?
The duration of a wire EDM process varies greatly depending on factors such as the material being cut, the thickness of the workpiece, the complexity of the shape, and the desired accuracy. Simple cuts in thin materials can take minutes, while complex parts in thick, hard materials can take several hours or even days. We recently completed a project involving intricate components for the aerospace industry, which took several days of continuous wire EDM operation to ensure the highest level of precision.
Is wire EDM an expensive process?
The cost of wire EDM can be higher than some conventional machining methods, especially for simple parts. However, for complex shapes, hard materials, and high-precision requirements, wire EDM can be very cost-effective. The ability to create intricate features without the need for expensive tooling, combined with the high level of automation, often results in lower overall costs compared to alternative methods.
How does wire EDM affect the material properties of the workpiece?
Wire EDM is a thermal process, so it does create a heat-affected zone (HAZ) near the cut surface. However, the HAZ in wire EDM is typically very small compared to other thermal cutting processes like laser or plasma cutting. The use of deionized water as a coolant helps to minimize the HAZ. In most cases, the effect on material properties is negligible, but for some critical applications, post-processing or heat treatment may be necessary. As experts in CNC fabrication, we can advise on the best approach for your specific material and application.
What kind of maintenance does a wire EDM machine require?
Wire EDM machines require regular maintenance to ensure optimal performance and longevity. This includes cleaning the machine, replacing filters, checking and adjusting wire tension, and monitoring the quality of the deionized water. The CNC control unit and other electronic components may also require periodic checks and updates. Proper maintenance is crucial for achieving consistent results and preventing costly downtime.
Wire EDM is a highly precise machining process that uses a thin wire and electrical sparks to cut conductive materials.
It excels at creating complex shapes, intricate features, and tight tolerances in a wide range of materials, including hardened steel and exotic alloys.
Wire EDM offers numerous advantages over conventional machining methods, including no cutting forces, burr-free cuts, and exceptional surface finish.
CNC technology plays a crucial role in wire EDM, enabling automation, precise motion control, and complex path programming.
The use of deionized water is essential for controlling the sparking process, flushing away debris, and cooling the workpiece.
Wire EDM is widely used in industries such as aerospace, medical devices, tool and die making, and electronics. Check out how we use wire EDM in the automotive industry.
Ongoing advancements in wire EDM technology, including increased automation, improved cutting speeds, and enhanced precision, are expanding its capabilities and applications.
I hope this comprehensive guide has provided you with valuable insights into the fascinating world of wire EDM. As a leading provider of CNC fabrication services, including sheet metal fabrication, precision machining, and CNC machining, we are committed to leveraging the latest technologies to deliver exceptional results for our clients. If you have any further questions or would like to discuss how wire EDM can benefit your next project, please don’t hesitate to contact us. We are always eager to share our expertise and help you achieve your manufacturing goals.
Get the latest trends and facts about CNC fabrication from our blog.
Shenzhen Runkey Precision Technology Co. Ltd, a subsidiary of the Tensun Group, is your trusted one-stop solution for custom manufacturing from prototyping to production.Transforming your idea into reality with digital manufacturing resources,streamlined processes, expert guidance,accelerated timelines, and uncompromising quality.
©2024. CNC Fabrication All Rights Reserved.