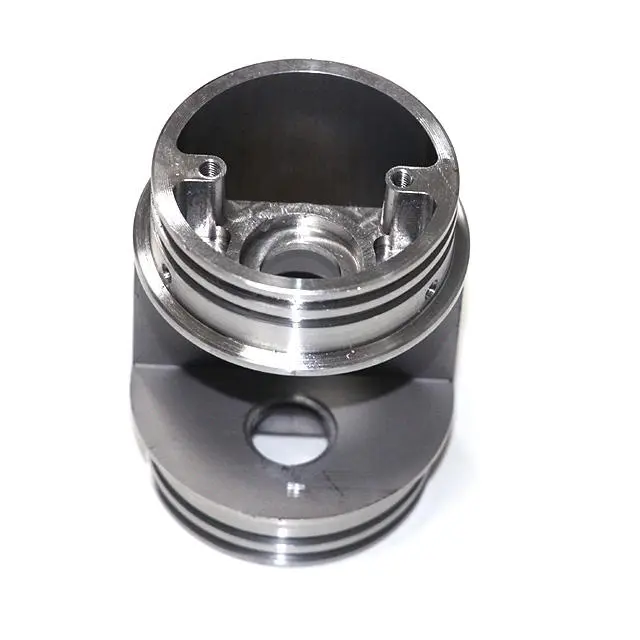
- +8615586668226
- [email protected]
- No. 30, Hongbang Industrial Park, Shenzhen
Alodine, often referred to as chem film or chromate conversion coating, is a chemical conversion coating that protects aluminum and other metals from corrosion. Unlike anodizing, which is an electrolytic process, Alodine creates a protective layer through a chemical reaction with the metal surface. This coating process results in a thin, durable film coating that significantly enhances corrosion resistance while maintaining electrical conductivity. I’ve seen firsthand how Alodine’s unique properties make it a preferred choice for industries where both protection and conductivity are crucial.
The primary difference between Alodine and anodizing becomes clearer when we examine their application methods. Anodizing involves immersing the metal part in an electrolytic bath and passing an electric current, forming a thick oxide layer. In contrast, the Alodine process involves dipping or spraying the part with a solution containing chromates. This simpler process makes Alodine coatings more cost-effective for many applications. While anodizing offers a thicker and harder surface finish, Alodine finish provides excellent corrosion resistance with minimal impact on the part’s dimensions. I often recommend Alodine for parts that require tight tolerances, as the coating thickness is minimal.
The chem film process, also known as the chromate conversion coating process, is a meticulously controlled sequence of steps designed to create a protective film on the surface of metal parts, especially aluminum parts. It begins with thorough cleaning to remove any contaminants. The part then undergoes a deoxidization process to ensure optimal adhesion. Finally, the film is applied by dipping the part into a solution containing the Alodine or by spraying. This chemical bath triggers a reaction that forms the protective chromate conversion coating. Our team has mastered this process, ensuring consistent and high-quality results for every project.
The application of chem film is applied with precision to ensure uniform coverage and optimal performance. The duration of immersion and the chemical composition of the bath are carefully controlled to achieve the desired coating thickness and properties. One of the key advantages of the Alodine process is its ability to coat complex shapes and intricate geometries effectively. This makes Alodine ideal for a wide range of applications, from small electronic components to large aerospace parts. I’ve personally witnessed how our precise application techniques result in superior protection and performance for our clients’ components.
There are primarily two types of chromate conversion coating: Type 1 and Type 2, as defined by the MIL-DTL-5541 standard. Type 1 coatings contain hexavalent chromium and offer superior corrosion resistance, but they are being phased out due to environmental concerns. Type 2, or MIL-DTL-5541 Type 2, coatings are based on trivalent chromium, which is more environmentally friendly while still providing excellent protection. We predominantly use Type 2 coatings in our operations, ensuring compliance with modern environmental standards while still delivering exceptional results.
Beyond the MIL-DTL-5541 standard, different types of Alodine formulations cater to specific needs. For instance, some formulations are designed for enhanced paint adhesion, while others prioritize electrical conductivity. The choice of Alodine coating depends on the specific application and performance requirements. We work closely with our clients to understand their needs and recommend the most suitable type of chromate conversion coating. With decades of experience, we have successfully applied various Alodine coatings to meet the diverse needs of industries such as aerospace, automotive, and medical devices. I’m always amazed by the versatility of Alodine and its ability to adapt to different requirements.
The benefits of chem film are numerous, making it a popular choice for protecting metal parts in various industries. One of the primary advantages is its exceptional ability to protect aluminum from corrosion. The thin film coating acts as a barrier, preventing moisture and other corrosive elements from reaching the underlying metal. This is particularly important in harsh environments or applications where the metal is exposed to the elements. In my experience, chem film coating has proven to be an extremely effective solution for extending the lifespan of aluminum components.
Another significant benefit of chem film is its ability to maintain electrical conductivity. Unlike some other coating processes that can create an insulating layer, Alodine allows for the flow of electricity. This makes it an excellent choice for applications where electrical grounding or conductivity is critical, such as in electronic enclosures or connectors. Additionally, Alodine coatings offer excellent paint adhesion, making them an ideal base for further surface finish treatments. These combined benefits make chem film or chromate conversion a versatile and reliable solution for a wide range of applications. From my perspective, the ability of Alodine to provide both protection and conductivity is a game-changer in many industries.
Alodine coating finds widespread use across numerous industries, each benefiting from its unique properties. In the aerospace industry, where lightweight yet durable materials are crucial, Alodine protects aluminum components from corrosion while maintaining their structural integrity. I’ve seen it applied to aircraft fuselages, wings, and other critical parts, ensuring their longevity and safety. Similarly, the automotive industry utilizes Alodine coatings on various components, including body panels, engine parts, and electrical connectors, to enhance their resistance to corrosion and wear.
The medical device industry also relies heavily on Alodine’s protective qualities. Medical equipment and instruments often require sterilization, and Alodine coating provides a durable barrier against the harsh chemicals and processes involved. Moreover, its ability to maintain electrical conductivity makes it suitable for electronic medical devices. The versatility of Alodine finishing extends to other sectors such as electronics, telecommunications, and consumer products, where it safeguards sensitive components from environmental damage while ensuring optimal performance. We proudly serve clients across these diverse industries, providing tailored solutions to meet their unique needs.
One of the standout features of Alodine coating is its ability to enhance or maintain electrical conductivity in metal parts, particularly aluminum. Unlike other types of coatings that may act as insulators, Alodine forms a thin, conductive layer that allows for the seamless flow of electricity. This characteristic is particularly crucial in applications where electrical grounding, shielding, or signal transmission is required. We often recommend Alodine for projects involving electronic enclosures, connectors, and other components where maintaining conductivity is paramount.
The conductive nature of Alodine coatings stems from the chemical reaction that occurs during the coating process. The resulting chromate conversion coating contains metallic chromium, which facilitates the transfer of electrons. This ensures that the coated parts can effectively conduct electricity, making them suitable for use in a wide range of electronic and electrical applications. In my years of experience, I’ve witnessed how crucial this property is in industries like aerospace and telecommunications, where reliable electrical connections are non-negotiable.
The MIL-DTL-5541 standard is a crucial military specification that governs the application and performance of chemical conversion coatings, including Alodine, on aluminum and aluminum alloys. This standard sets forth the requirements for two main types of chromate conversion coating: Type 1, which contains hexavalent chromium, and Type 2, which is based on trivalent chromium. Adherence to MIL-DTL-5541 ensures that the coating meets stringent quality and performance criteria, making it suitable for demanding military and aerospace applications.
At our facility, we strictly adhere to the MIL-DTL-5541 standard when applying Alodine coatings. This commitment to quality ensures that our clients receive coatings that meet the highest industry standards for corrosion resistance, adhesion, and overall performance. Type 2 coatings, which comply with the latest environmental regulations, are our primary focus. By following these guidelines, we deliver reliable and consistent results that our clients can depend on. I’ve always believed that adhering to industry standards is essential for building trust and ensuring customer satisfaction.
While Alodine is highly effective on a wide range of aluminum alloys, its performance can vary depending on the specific alloy composition. Common alloys like 6061 and 7075 respond exceptionally well to the Alodine process, forming a robust and uniform coating that provides excellent corrosion protection. However, some alloys may require specific pre-treatments or adjustments to the coating process to achieve optimal results. Our extensive experience with various aluminum alloys allows us to tailor our processes to ensure the best possible outcome for each material.
It’s important to note that the effectiveness of Alodine coating can also be influenced by the presence of other elements in the alloy, such as copper or magnesium. These elements can affect the chemical reaction during the coating process, potentially impacting the final coating thickness and properties. We carefully analyze the composition of each alloy before applying Alodine, making any necessary adjustments to ensure a consistent and high-quality finish. This attention to detail is what sets us apart and allows us to deliver superior results for our clients.
Alodine coating is renowned for its thinness, typically ranging from 0.0001 to 0.0005 inches in thickness. This minimal thickness is one of its key advantages, as it provides excellent corrosion protection without significantly altering the dimensions of the coated part. This makes Alodine ideal for applications where tight tolerances are crucial, such as in precision machinery or electronic components. We understand the importance of maintaining precise dimensions, and our meticulous application process ensures consistent coating thickness across all parts.
The thinness of Alodine coating does not compromise its effectiveness. Despite its minimal thickness, the coating forms a robust barrier against corrosion, effectively protecting the underlying metal from environmental damage. The performance of the coating is influenced by factors such as the specific Alodine formulation, the duration of the coating process, and the condition of the metal surface. We carefully control these variables to achieve the desired level of protection and performance for each project.
As a leading CNC precision manufacturing company, we offer comprehensive machining services and fabrication services, including expert application of Alodine coating. Our state-of-the-art facility is equipped with advanced machinery and technology, enabling us to deliver high-quality, precision-crafted components to a wide range of industries. We pride ourselves on our ability to provide tailored solutions that meet the unique needs of each client. Whether you require CNC machining, CNC milling, CNC turning, sheet metal fabrication, or rapid prototyping, we have the expertise and resources to exceed your expectations.
Our team of skilled engineers and technicians has extensive experience in applying Alodine and other surface finishes. We work closely with our clients to understand their specific requirements and recommend the most suitable coating solutions. Our commitment to quality, precision, and customer satisfaction sets us apart in the industry. We are dedicated to providing exceptional service and delivering results that enhance the performance and longevity of your products. When you choose us for your Alodine coating needs, you’re partnering with a company that values quality and customer satisfaction above all else.
How does Alodine differ from anodizing?
Alodine is a chemical conversion coating that creates a protective layer through a chemical reaction, while anodizing is an electrolytic process that forms a thicker oxide layer. Alodine maintains electrical conductivity and has minimal impact on part dimensions, making it suitable for applications requiring tight tolerances.
What types of metals can be treated with Alodine?
Alodine is primarily used for aluminum and its alloys, but it can also be applied to other metals like magnesium and zinc under specific conditions.
Is Alodine environmentally friendly?
Type 2 Alodine coatings, which use trivalent chromium, are more environmentally friendly than Type 1 coatings that contain hexavalent chromium. Type 2 coatings comply with modern environmental regulations while providing excellent corrosion protection.
Can Alodine be used as a primer for paint?
Yes, Alodine coatings offer excellent paint adhesion, making them an ideal base for further surface treatments like painting or powder coating.
How does Alodine affect the dimensions of a part?
Alodine coatings are very thin, typically ranging from 0.0001 to 0.0005 inches, so they have minimal impact on the dimensions of the coated part.
What industries commonly use Alodine coating?
Alodine coating is widely used in industries such as aerospace, automotive, medical devices, electronics, telecommunications, and consumer products, where corrosion protection and maintaining electrical conductivity are crucial.
Alodine, also known as chem film or chromate conversion coating, is a highly effective method for protecting aluminum and other metals from corrosion.
The Alodine process creates a thin, durable coating through a chemical reaction, offering excellent corrosion resistance while maintaining electrical conductivity.
There are different types of Alodine coatings, with Type 2 coatings (trivalent chromium) being more environmentally friendly and compliant with modern regulations.
Alodine coatings are widely used in various industries, including aerospace, automotive, medical devices, and electronics, due to their unique properties.
The MIL-DTL-5541 standard governs the application and performance of Alodine coatings, ensuring high quality and reliability.
Choosing a reputable CNC precision manufacturing company like ours ensures expert application of Alodine coating and superior results for your projects.
By understanding the intricacies of Alodine coating and its benefits, you can make informed decisions about protecting and enhancing your metal components. Our team is ready to assist you with your next project, providing expert guidance and top-tier manufacturing services. Contact us today to learn more about how we can help you achieve your goals.
Get the latest trends and facts about CNC fabrication from our blog.
Shenzhen Runkey Precision Technology Co. Ltd, a subsidiary of the Tensun Group, is your trusted one-stop solution for custom manufacturing from prototyping to production.Transforming your idea into reality with digital manufacturing resources,streamlined processes, expert guidance,accelerated timelines, and uncompromising quality.
©2024. CNC Fabrication All Rights Reserved.