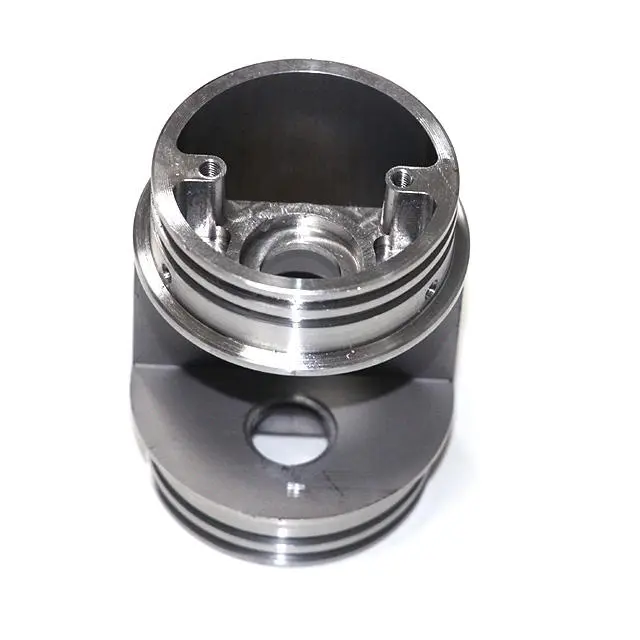
- +8615586668226
- [email protected]
- No. 30, Hongbang Industrial Park, Shenzhen
Electrical Discharge Machining (EDM) is a non-traditional machining method that uses electrical discharges, or sparks, to remove material from a workpiece. It’s a highly accurate machining technique, particularly useful for shaping hard metals and creating complex shapes that are difficult to achieve with traditional machining methods. The EDM process involves a series of rapidly recurring current discharges between two electrodes, separated by a dielectric fluid and subjected to an electric voltage. This machine is used to erode material from the workpiece to create the desired shape.
EDM is particularly useful for machining hard materials like titanium and for creating intricate designs. As a machine shop specializing in CNC machining, we often utilize EDM to complement our services, ensuring we can meet even the most challenging machining needs. The three primary types of EDM are wire, sinker, and drill, each offering unique capabilities for various machining applications.
There are three main types of EDM machines: wire EDM, sinker EDM, and drill EDM. Each type of EDM utilizes a different method to shape the workpiece.
Wire EDM: This machine uses a thin, electrically charged wire as an electrode to cut through the workpiece. It’s ideal for creating intricate shapes and precise cuts. The wire EDM process is akin to using a high-tech band saw, where the wire acts as the blade.
Sinker EDM: Also known as ram EDM, this machine uses a custom-shaped electrode to “sink” into the workpiece, creating a cavity or impression. It’s often used for molding and die-making applications. Sinker discharge machining is particularly useful for creating complex 3D shapes.
Drill EDM: As the name suggests, this machine is used to drill small, deep holes with high precision. It’s often used as a precursor to wire EDM, creating a starting hole for the wire to pass through.
Wire EDM is a fascinating machining process that employs a thin, single-strand metal wire, usually made of brass, as the electrode. This wire electrode is guided along a programmed path to cut through the workpiece, which is submerged in a dielectric fluid. The machine generates electrical discharges between the wire and the workpiece, eroding the material and creating the desired shape.
Wire EDM machines use a continuous stream of deionized water to flush away the eroded particles, ensuring a clean and precise cut. The wire EDM machine is especially adept at creating intricate shapes, sharp corners, and delicate features that are impossible to achieve with conventional machining methods. It is also possible to perform 5-axis CNC machining using this machining method.
The key advantages of wire EDM include:
High Precision: Wire EDM can achieve tolerances as tight as ±0.0001 inches, making it ideal for parts requiring extreme accuracy.
Complex Shapes: The thin wire can navigate intricate paths, allowing for the creation of complex geometries and delicate features.
Burr-Free Cutting: The wire EDM process produces a clean, burr-free edge, eliminating the need for secondary finishing operations.
Hard Materials: Wire EDM can easily cut through hard and conductive materials, such as tool steel, titanium, and Inconel.
Sinker EDM, also known as ram EDM or die-sinking EDM, is a machining method that uses a custom-shaped electrode to erode material from the workpiece. The electrode, typically made of graphite or copper, is machined into the desired shape, and then “sunk” into the workpiece while submerged in a dielectric fluid. The machine generates electrical discharges between the electrode and the workpiece, gradually eroding the material to create the desired cavity or form.
Sinker EDM is particularly well-suited for:
Creating Molds and Dies: The ability to create complex 3D shapes makes sinker EDM ideal for manufacturing molds, dies, and other tooling components.
Blind Cavities: Sinker EDM can create cavities that do not go all the way through the workpiece, which is impossible with wire EDM.
Sharp Internal Corners: While wire EDM can struggle with sharp internal corners, sinker EDM can produce them with ease.
Surface Finishes: Sinker EDM can achieve a variety of surface finishes, from rough to highly polished, by adjusting the machining parameters.
Drill EDM, also known as hole drilling EDM or hole-drilling EDM, is a specialized type of EDM used to create small, deep holes with high precision. This machine uses a tubular electrode that rotates while electrical discharges erode the material, creating a hole. The dielectric fluid is flushed through the electrode to remove debris and cool the workpiece.
EDM drilling plays a crucial role in the machining process, especially in conjunction with wire EDM. Often, a starting hole is required for the wire to pass through before the wire EDM process can begin. Drill EDM provides a fast and accurate way to create these starting holes, even in hard materials. It is also the EDM technique that is perfect for producing small deep holes that are beyond the capabilities of conventional machining.
One of the key advantages of EDM is its ability to machine a wide range of conductive materials, regardless of their hardness. This makes it an ideal solution for working with materials that are difficult or impossible to machine using traditional machining methods. Some of the materials commonly used with EDM include:
Tool Steels: High-speed steel, D2, A2, and other tool steels are easily machined using EDM.
Stainless Steels: Various grades of stainless steel, including 304, 316, and 17-4 PH, can be processed with EDM.
Titanium: EDM is a preferred method for machining titanium alloys, which are known for their strength and lightweight properties.
Inconel: This nickel-based superalloy, often used in aerospace applications, is well-suited for EDM.
Carbide: Tungsten carbide, a very hard and wear-resistant material, can be effectively shaped using EDM.
Copper and Brass: These conductive materials are often used for electrodes in sinker EDM, but they can also be machined using EDM.
EDM offers several advantages over conventional machining methods like milling, turning, and grinding, particularly when dealing with hard materials and complex shapes. Here’s a comparison table:
Feature | EDM | Conventional Machining |
Material Hardness | Can machine any conductive material | Limited by tool hardness |
Shape Complexity | Can create intricate shapes and features | Limited by tool geometry and accessibility |
Burr Formation | Burr-free cutting | Burrs often require removal |
Tool Wear | Minimal electrode wear | Significant tool wear |
Cutting Forces | No cutting forces, reducing stress | Cutting forces can deform workpiece |
Surface Finish | Controllable surface finish | Dependent on tool and cutting parameters |
However, EDM is generally slower than conventional machining methods, and it is limited to conductive materials. The choice between EDM and conventional machining depends on the specific machining requirements of the project.
EDM machining finds applications in a wide range of industries, including:
Aerospace: EDM is used to create precise components for aircraft engines, fuel systems, and other critical parts. You can learn more about how we serve the aerospace industry here.
Automotive: EDM is employed in the production of molds for plastic parts, as well as for machining complex engine components. Check out our automotive industry solutions here.
Medical Devices: EDM’s precision makes it ideal for manufacturing intricate medical implants, surgical instruments, and diagnostic equipment. Discover how we cater to the medical devices industry here.
Electronics: EDM is used to create micro-components for electronic devices, such as connectors, contacts, and heat sinks. Learn more about our work in the electronics industry here.
Tool and Die Making: EDM is a cornerstone of the tool and die industry, enabling the creation of complex molds, dies, and other tooling components.
Defense and Military: EDM plays a vital role in manufacturing precision parts for weapons systems, communication devices, and other defense applications.
Energy and Renewable Energy: EDM is used in the production of components for power generation equipment, including turbines, generators, and solar panels.
Robotics: EDM’s ability to create intricate shapes makes it valuable in the development of robotic components and systems.
Precision is paramount in EDM machining for several reasons:
Tight Tolerances: Many EDM applications, particularly in industries like aerospace and medical devices, require extremely tight tolerances, often measured in microns.
Complex Geometries: EDM is often used to create intricate shapes and features that demand high accuracy to function correctly.
Material Integrity: The EDM process must be carefully controlled to avoid damaging the workpiece or altering its material properties.
Repeatability: EDM is often used for production runs, where each part must be identical to the others. Precision ensures consistency across all parts.
Minimizing Waste: Precision machining reduces material waste, which is particularly important when working with expensive materials like titanium or Inconel.
As a leading provider of CNC fabrication services, we offer a comprehensive range of machining solutions, including wire EDM, sinker EDM, and drill EDM. Our team of experienced machinists and engineers can help you optimize your designs for EDM, ensuring that your parts are manufactured to the highest standards of precision and quality.
We utilize state-of-the-art EDM machines and employ advanced machining techniques to deliver exceptional results. Our machining capabilities extend beyond EDM, encompassing CNC machining, milling, turning, and other precision machining processes. We also offer rapid prototyping services to help you quickly iterate and validate your designs.
By partnering with us, you gain access to:
Expertise: Our team has extensive experience in EDM and other machining technologies.
Advanced Equipment: We invest in the latest EDM machines to ensure optimal performance and precision.
Quality Assurance: We have rigorous quality control processes in place to guarantee that your parts meet your exact specifications.
Customer Service: We are committed to providing exceptional customer service and support throughout your project.
What is the difference between wire EDM and sinker EDM?
Wire EDM uses a thin wire electrode to cut through the workpiece, while sinker EDM uses a custom-shaped electrode to create a cavity or form.
What are the advantages of EDM over conventional machining?
EDM can machine hard materials, create complex shapes, and produce burr-free cuts.
What materials can be machined with EDM?
EDM can machine any conductive material, including tool steels, stainless steels, titanium, Inconel, carbide, copper, and brass.
What industries use EDM machining?
EDM is used in aerospace, automotive, medical devices, electronics, tool and die making, defense, energy, and robotics.
What is the purpose of dielectric fluid in EDM?
The dielectric fluid acts as an insulator, controls the spark gap, flushes away debris, and cools the workpiece and electrode.
Is EDM a fast machining process?
EDM is generally slower than conventional machining methods, but its precision and ability to machine hard materials make it a valuable process for specific applications.
In summary, here are the key takeaways about EDM machining:
Electrical Discharge Machining (EDM) is a versatile and precise machining method that utilizes electrical sparks to shape conductive materials.
There are three main types of EDM: wire EDM, sinker EDM, and drill EDM, each with unique capabilities.
Wire EDM is ideal for creating intricate shapes and precise cuts using a thin wire electrode.
Sinker EDM uses a custom-shaped electrode to create cavities and forms, making it suitable for mold and die making.
Drill EDM is used to create small, deep holes with high precision, often as a precursor to wire EDM.
EDM can machine a wide range of conductive materials, including tool steels, stainless steels, titanium, Inconel, carbide, copper, and brass.
EDM offers advantages over conventional machining in terms of material hardness, shape complexity, and burr formation.
Precision is crucial in EDM machining to achieve tight tolerances, complex geometries, and material integrity.
CNC fabrication services, like ours, can enhance your EDM projects by providing expertise, advanced equipment, and rigorous quality control.
We can also offer surface finishing solutions if you require it.
Partnering with a reliable CNC fabrication provider ensures that your parts are manufactured to the highest standards, meeting your specific requirements and exceeding your expectations.
By understanding the capabilities and advantages of EDM machining, you can leverage this powerful technology to bring your most challenging designs to life.
Get the latest trends and facts about CNC fabrication from our blog.
Shenzhen Runkey Precision Technology Co. Ltd, a subsidiary of the Tensun Group, is your trusted one-stop solution for custom manufacturing from prototyping to production.Transforming your idea into reality with digital manufacturing resources,streamlined processes, expert guidance,accelerated timelines, and uncompromising quality.
©2024. CNC Fabrication All Rights Reserved.