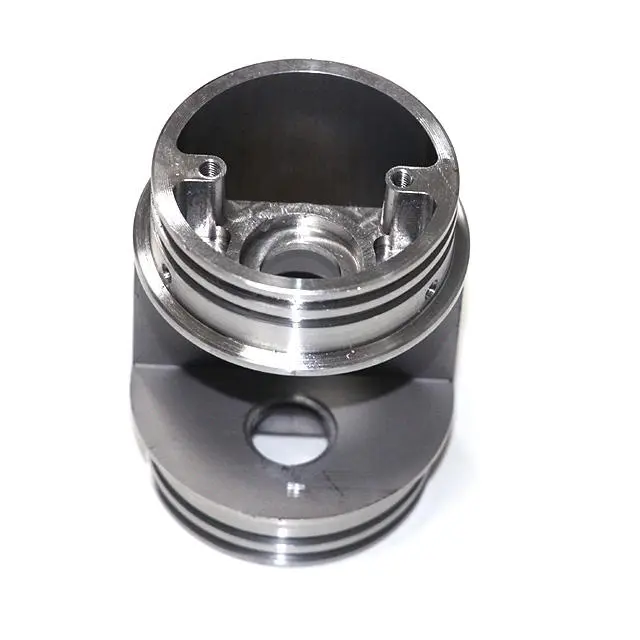
- +8615586668226
- [email protected]
- No. 30, Hongbang Industrial Park, Shenzhen
Welding is a fabrication process that joins metal parts together by using high heat to melt the metal together. As a CNC precision manufacturing company, we often rely on welding for projects that require strong, permanent bonds, especially for load-bearing structures or components that must be airtight. Welding creates a continuous metal seam, known as a welded joint, offering exceptional strength and durability.
There are several types of welding processes, including arc welding, TIG welding, MIG welding, and laser welding. Each method has its specific applications and advantages. For instance, arc welding is commonly used for thicker metal sections, while laser welding is preferred for precision work on thinner sheet metal parts. Choosing the right welding method depends on the specific requirements of the project, including the type of metal, the desired strength of the joint, and the overall design of the sheet metal assembly.
Riveting is a mechanical fastening method that joins two or more metal parts together using metal fasteners called rivets. Rivets are typically cylindrical rods with a head on one end. To create a riveted joint, a rivet is inserted through pre-drilled holes in the metal parts, and the other end is deformed using a rivet gun or other tools, creating a second head that holds the parts together.
Riveting is often used in applications where welding is not feasible or desirable. For example, when joining dissimilar metals or when the heat from welding could damage the metal parts, riveting provides a reliable alternative. Riveting is also a preferred method for joining sheet metal parts in industries such as aerospace, where lightweight and strong joints are crucial. The main advantage of riveting is that riveting involves creating a joint between the material and rivet without the need for heat, which can help preserve the integrity and structural properties of the joined metals.
The choice between welding and riveting often comes down to the specific needs of the project. One of the primary differences between welding vs riveting is that welding is a thermal process that involves melting the base metal to create a joint, while riveting is a mechanical process that uses metal fasteners to hold parts together. This fundamental difference leads to variations in strength, durability, and aesthetic appeal.
Another key difference is the ability to join dissimilar metals. Welding can be challenging when working with different metal types due to variations in melting points and metallurgical properties. On the other hand, riveting excels in this area, allowing for the joining of dissimilar metal components without the issues associated with welding. This is why we use riveting in our manufacturing plant. This is why we use riveting in our manufacturing plant. Riveting and welding are two distinct methods used to join two or more pieces of material together.
Welding offers several advantages, including the creation of strong, permanent, and often seamless joints. Welded joints are typically stronger than the surrounding metal, making welding suitable for applications requiring high strength and durability. Welding is also versatile, allowing for the joining of various metal types and thicknesses.
However, welding has its drawbacks. The welding process requires skilled labor and specialized equipment, which can increase costs. Additionally, the high heat involved in welding can lead to thermal distortion, where the metal parts warp or deform due to the heat. Welding might also require post-weld treatments, such as stress relieving or grinding, to achieve the desired finish and structural integrity.
Advantages of Welding | Disadvantages of Welding |
Creates strong, permanent joints | Requires skilled labor and specialized equipment |
Offers high strength and durability | Can cause thermal distortion |
Versatile, can join various metal types and sizes | May require post-weld treatments |
Produces seamless joints | Potential for defects like porosity and cracking |
Suitable for airtight and watertight applications | Higher initial setup cost compared to riveting |
Can be automated for high-volume production | Heat-affected zone may weaken the surrounding material |
Riveting offers several advantages, particularly for joining sheet metal parts. One of the main benefits of riveting is its ability to join dissimilar metals without the complications associated with welding. Riveting also creates a strong mechanical joint without the need for heat, preserving the integrity of the metal parts. We have seen firsthand the effectiveness of riveting in applications where maintaining material properties is paramount.
However, riveting has limitations. Riveted joints might not be as strong as welded joints, especially in high-stress applications. Additionally, rivets can add weight to the assembly, which can be a concern in industries like aerospace where weight reduction is critical. Riveting also requires access to both sides of the joint, which can be challenging in certain designs.
The cost of welding versus riveting can vary depending on several factors, including the complexity of the joint, the type of metal, and the required labor and equipment. Generally, welding can have higher initial costs due to the need for skilled welders and specialized welding equipment. However, welding can be more cost-effective for high-volume production where automation can be implemented.
Riveting, on the other hand, can have lower initial costs, especially for smaller projects. Rivet guns and other riveting tools are generally less expensive than welding equipment. However, the cost of rivets themselves and the labor involved in the riveting process can add up, particularly for complex assemblies. In our experience, we’ve found that for certain projects, the simplicity and speed of riveting can lead to overall cost savings.
When it comes to strength and durability, welding generally outperforms riveting. Welded joints are typically stronger than the surrounding metal, creating a seamless and continuous bond. This makes welding the preferred method for applications requiring high strength and structural integrity, such as in the construction of bridges, buildings, and heavy machinery.
While riveting creates strong mechanical joints, they might not match the strength of welded joints, particularly under extreme loads or stress. Riveted joints rely on the strength of the rivets themselves and the friction between the joined metal parts. However, riveting can still provide adequate strength for many applications, especially in industries like aerospace where lightweight and reliable joints are crucial.
The aesthetic appeal of a joint can be an important factor, particularly in consumer products or architectural applications. Welding offers the advantage of creating seamless joints that can be nearly invisible, especially when using techniques like TIG welding. This can result in a clean and visually appealing finish.
Riveting, on the other hand, creates visible joints with protruding rivet heads. While some might find the industrial look of riveted joints appealing, others might prefer the seamless appearance of welded joints. In our experience, we’ve seen that the choice between welding and riveting based on aesthetics often depends on the specific design and the desired look of the final product.
Safety is a critical consideration in any manufacturing process. Welding involves working with high heat, intense light, and potentially hazardous fumes. Welders must wear appropriate protective gear, including welding helmets, gloves, and flame-resistant clothing. Proper ventilation is also essential to prevent the inhalation of fumes.
Riveting is generally considered safer than welding, as it does not involve high heat or intense light. However, riveting still requires safety precautions, such as wearing eye protection to prevent injury from flying debris. Additionally, the use of rivet guns can lead to repetitive strain injuries if proper ergonomic practices are not followed.
Choosing between welding or riveting depends on a variety of factors, including the specific requirements of your project, the type of metal being used, and the desired strength, durability, and aesthetic appeal of the joint.
Here are some key considerations to help you make the right choice:
Strength Requirements: If your project requires maximum strength and durability, welding is likely the better option.
Material Type: If you’re working with dissimilar metals or heat-sensitive materials, riveting might be more suitable.
Aesthetic Appeal: If a seamless, invisible joint is desired, welding is the way to go. If visible joints are acceptable or even preferred, riveting can be used.
Cost: Consider the initial setup costs, labor costs, and material costs for each method. Welding can be more expensive upfront but may offer long-term cost savings for high-volume production.
Safety: Evaluate the safety requirements and ensure that appropriate precautions are in place for either welding or riveting.
What are the different types of welding used in sheet metal fabrication?
There are several types of welding used in sheet metal fabrication, including arc welding, TIG welding, MIG welding, and laser welding. Each method has its own advantages and is suitable for different applications. For instance, TIG welding offers precision and a clean finish, making it ideal for thin sheet metal parts, while arc welding is commonly used for thicker materials. Other welding methods used for joining sheet metal include spot welding and resistance welding.
Can riveting be used to join thick metal parts?
While riveting is commonly used for joining sheet metal parts, it can also be used for thicker metal parts. However, the effectiveness of riveting in thicker materials depends on the size and strength of the rivets used. For very thick metal parts, welding might be a more suitable option.
Is welding stronger than riveting?
Generally, welding creates stronger joints compared to riveting. Welded joints are typically stronger than the surrounding metal, offering a seamless and continuous bond. Riveted joints, while strong, rely on the strength of the rivets and the friction between the joined metal parts. In high-stress applications, welding is often the preferred method for its superior strength. The answer is yes, welding is stronger than riveting. Welding produces a permanent bond between the metal, which makes the welded joint stronger and more durable than a riveted joint.
What are the advantages of automated riveting?
Automated riveting offers several benefits, including increased speed and efficiency, improved consistency and accuracy, and reduced labor costs. Automated riveting systems can perform riveting operations much faster than manual riveting, making them ideal for high-volume production. Additionally, automation ensures that each rivet is installed with the same precision, resulting in consistent and reliable joints.
What materials are commonly used for riveting?
Rivets can be made from various materials, including aluminum, steel, stainless steel, copper, and brass. The choice of rivet material depends on the specific application and the type of metal being joined. For instance, aluminum rivets are often used in aerospace applications due to their lightweight and corrosion-resistant properties, while steel rivets are preferred for their strength and durability.
What are some common applications for sheet metal joining?
Sheet metal joining is used in a wide range of industries and applications. Some common examples include the manufacturing of automotive body panels, aircraft fuselages, electronic enclosures, appliances, and HVAC systems. Sheet metal joining techniques, such as welding and riveting, are essential for creating strong, durable, and reliable assemblies in these and many other applications.
In summary, the choice between welding and riveting is a crucial decision in sheet metal fabrication. Each method offers unique advantages and is suitable for different applications. Here are the key takeaways to remember:
Welding creates strong, permanent, and often seamless joints, making it ideal for applications requiring high strength and durability.
Riveting is a versatile method that can join dissimilar metals without heat, preserving material properties.
Welding generally offers superior strength, while riveting can be more cost-effective for certain projects.
The aesthetic appeal of welded joints is often preferred for consumer products, while riveted joints can offer an industrial look.
Safety considerations are important for both methods, with welding requiring more stringent precautions due to the high heat and potential fumes.
The best choice between welding and riveting depends on the specific requirements of your project, including strength, material type, cost, and desired aesthetics.
As a leading CNC precision manufacturing company specializing in sheet metal fabrication, we are committed to helping our clients make the best decisions for their projects. Whether you need the strength of welding or the versatility of riveting, we have the expertise and experience to deliver exceptional results. Contact us today to discuss your sheet metal needs and discover how we can help you achieve your manufacturing goals.
Internal Links:
Learn more about our sheet metal fabrication services.
Explore our expertise in laser cutting.
Discover the benefits of 5 axis CNC machining.
Read about our precision machining.
Find out more about aluminum extrusion.
Check out our surface finishing solutions.
Get the latest trends and facts about CNC fabrication from our blog.
Shenzhen Runkey Precision Technology Co. Ltd, a subsidiary of the Tensun Group, is your trusted one-stop solution for custom manufacturing from prototyping to production.Transforming your idea into reality with digital manufacturing resources,streamlined processes, expert guidance,accelerated timelines, and uncompromising quality.
©2024. CNC Fabrication All Rights Reserved.