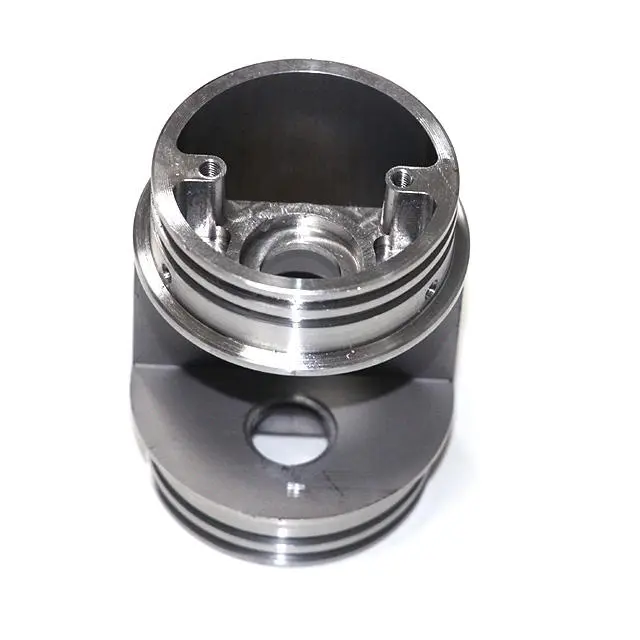
- +8615586668226
- [email protected]
- No. 30, Hongbang Industrial Park, Shenzhen
Welding is a fabrication process that joins materials, usually metals or thermoplastics, by causing fusion. This is often done by melting the workpieces and adding a filler material to form a pool of molten material that cools to become a strong joint. Welding is mainly used when a permanent, high-strength joint is required. The welding process can create joints that are as strong as, or even stronger than the base metal.
There are various types of welding, including arc welding, TIG welding, and resistance welding. Each method has its own set of advantages and is suitable for different applications. For instance, TIG welding is often preferred for precision work, such as in the aerospace industry, due to its ability to produce clean and accurate welds. Welding can be used on a wide range of metals and is a popular choice in industries where structural integrity is paramount, such as in the manufacturing of automotive body panels. When done correctly, welding creates seamless and strong joints, making it suitable for creating airtight or watertight seals.
Riveting is a fastening method that uses a mechanical fastener called a rivet to join two or more workpieces. A rivet is a metal pin or bolt that is inserted through pre-drilled holes in the materials to be joined. The end of the rivet is then deformed, either by hammering or using a specialized tool, to create a new “head” that holds the materials together. This forms a rivet joint that can be very strong and durable, especially when pop rivets or other specialized types of rivets are used.
Riveting is mainly used for joining materials where welding is not feasible or practical. Unlike welding, riveting does not require heat, making it suitable for joining dissimilar materials or materials that are sensitive to high temperatures. Riveting is also a relatively simple and fast process, making it a cost-effective solution for many applications. In applications such as sheet metal fabrication, riveting provides a reliable and efficient way to join metal pieces together, particularly where the sheets of metal are thin. However, even countersunk rivets will protrude slightly, so this may not be a solution where the finish needs to be smooth.
The primary difference between welding and riveting lies in the method of joining. Welding joins materials by melting and fusing them together, often with the addition of a filler material. Riveting, on the other hand, uses a mechanical fastener (rivet) to hold materials together. Welding creates a permanent joint, while riveting creates a semi-permanent joint that can be disassembled if needed, though this is not always advisable.
Feature | Welding | Riveting |
Joining Method | Fusion (melting) | Mechanical Fastening |
Joint Type | Permanent | Semi-Permanent |
Heat Required | Yes | No |
Materials | Similar or Dissimilar (with filler) | Similar or Dissimilar |
Strength | High (often stronger than base metal) | High (depends on rivet type and material) |
Appearance | Seamless (if done correctly) | Visible Fasteners (rivet heads) |
Cost | Can be higher (equipment, skilled labor) | Generally lower (simpler process, less equipment) |
Speed | Can be slower (depending on process) | Often faster |
Skill Level | High (requires training and expertise) | Lower (easier to learn and master) |
Distortion | Possible due to heat | Minimal |
Corrosion Resistance | Can be high, especially with stainless steel welds | Potential for galvanic corrosion if dissimilar metals are used |
Welding is generally stronger and more durable than riveting, as it creates a continuous bond between the materials. However, riveting is often faster and more cost-effective, especially for large-scale projects. For example, the automotive industry often uses a combination of welding and riveting for joining different parts of a vehicle. Welding might be used for the chassis, where strength is critical, while riveting could be used for body panels where speed and ease of assembly are important.
Choose welding when you need a permanent, high-strength joint that is as strong or stronger than the surrounding metal. Welding is ideal for applications where the joint will be subjected to high stress or vibration. As a method of joining metals, welding can be the best option where structural integrity is of utmost importance, such as in the construction of bridges, buildings, and pressure vessels.
Welding is also the preferred method when joining thick metal pieces or when creating airtight or watertight seals. Welding can create seamless joints that are less prone to leakage than rivet joints. However, welding requires skilled labor and specialized equipment, which can increase the overall cost of the project. We, as expert CNC fabricators, use welding extensively in projects requiring the joining of two pieces of metal together where a strong, permanent bond is essential.
Choose riveting when you need a fast, cost-effective, and reliable method for joining sheet metal parts. Riveting is an excellent choice when working with thin materials that could be damaged by the heat of welding. It is also the preferred method when joining dissimilar materials or when working with materials that have pre-applied finishes. Riveting is much faster than welding, especially when using automated or semi-automated riveting tools.
Riveting is a great option for projects where disassembly might be required in the future. While riveted parts are generally secure, the rivets can be drilled out to separate the joined components. This makes riveting a popular choice in industries like aerospace, where components may need to be replaced or repaired over time. It’s also worth noting that rivets are easy to install, and riveting is often the go-to choice for quick and efficient assembly in the production of consumer products.
Advantages of welding:
High Strength: Welding creates extremely strong joints that are often stronger than the parent metal.
Permanent: Welded joints are permanent and cannot be easily disassembled.
Seamless: When done correctly, welding can produce seamless joints with no visible fasteners.
Airtight/Watertight: Welding is ideal for creating airtight or watertight seals.
Versatile: Welding can be used on a wide range of metals and alloys.
Disadvantages of welding:
Heat Distortion: The heat involved in welding can cause distortion or warping of the materials, especially thin sheet metal.
Skill Required: Welding requires skilled labor and specialized training.
Cost: Welding equipment and consumables can be expensive.
Safety: Welding can be hazardous, requiring proper safety precautions and personal protective equipment.
Time-Consuming: Compared to riveting, some welding processes can be time-consuming.
Advantages of riveting:
Speed: Riveting is a fast fastening method, especially when using automated tools.
Cost-Effective: Riveting is generally less expensive than welding, as it requires less equipment and specialized labor.
No Heat: Riveting does not require heat, making it suitable for heat-sensitive materials.
Dissimilar Materials: Riveting can be used to join dissimilar materials.
Ease of Use: Rivets are relatively easy to install, even for unskilled workers.
Disadvantages of riveting:
Visible Fasteners: Rivet heads are visible on the surface of the joined materials.
Potential for Leakage: Rivet joints may not be completely airtight or watertight.
Stress Concentration: Holes drilled for rivets can create stress concentration points in the material.
Corrosion: Riveted joints can be susceptible to corrosion, especially if dissimilar metals are used.
Limited Strength: While riveted joints are strong, they may not be as strong as welded joints in some applications.
In general, riveting is often more cost-effective than welding, especially for high-volume production. Riveting equipment is typically less expensive than welding equipment, and the riveting process is faster, which reduces labor costs. Additionally, riveting does not require the same level of skill and training as welding, further reducing labor costs.
However, the cost difference between welding and riveting can vary depending on the specific application and the materials being joined. For example, welding may be more cost-effective for joining thick metal sections or for creating complex joints. Welding also may be the only option for certain materials or applications where high strength and durability are critical.
Welding generally offers better structural integrity than riveting. Welding creates a continuous bond between the materials, resulting in a joint that is as strong or stronger than the surrounding metal. Welded joints are also less prone to fatigue and failure under stress than rivet joints.
However, riveting can provide sufficient structural integrity for many applications. When properly designed and installed, riveted joints can be very strong and durable. Riveting is often used in applications where high strength is required, such as in aircraft construction. In such cases, the use of high-strength rivets and careful design of the rivet joint can ensure that the joint meets the required structural standards.
Choosing between welding and riveting depends on the specific requirements of your project. Consider the following factors:
Material Thickness: Welding is generally preferred for thicker materials, while riveting is better suited for thin sheet metal.
Joint Strength: If you need a joint with maximum strength and durability, welding is the better choice.
Cost: Riveting is generally more cost-effective, especially for high-volume production.
Speed: Riveting is a faster process than welding.
Appearance: If a seamless appearance is important, welding is preferred.
Disassembly: If you need the ability to disassemble the joint in the future, riveting is the better option.
Welding and riveting are two methods for joining metal pieces, each with its own respective advantages. Welding joins metals by melting them together, while riveting uses a metal pin or bolt to create a mechanical joint. Whether welding or riveting is better depends on the specific application. For example, welding can be used to create strong, permanent joints, while riveting is faster and more cost-effective for joining thin sheets of metal. By understanding the differences between welding and riveting, you can make an informed decision that will ensure the success of your project.
By carefully considering these factors and understanding the advantages and disadvantages of each method, you can make an informed decision about whether to use welding or riveting for your project. If you’re still unsure, don’t hesitate to reach out to our team of experts at CNC Fabrication Services. We have years of experience in both welding and riveting and can help you choose the best method for your specific needs. We are committed to providing our clients with the highest quality CNC machining services and fabrication solutions, and we are always happy to answer any questions you may have.
What are the most common types of rivets used in sheet metal fabrication?
The most commonly used types of rivets in sheet metal fabrication include solid rivets, blind rivets (also known as pop rivets), tubular rivets, and drive rivets. Each type has its own specific applications and advantages.
Can riveting be used for joining dissimilar metals?
Yes, riveting can be used to join dissimilar metals. However, it’s important to consider the potential for galvanic corrosion when joining different types of metal. Using a non-conductive material between the metals or selecting rivets made of a compatible material can help mitigate this risk.
Is welding always stronger than riveting?
While welding generally creates stronger joints than riveting, the strength of a riveted joint depends on factors such as the type of rivet used, the material being joined, and the design of the joint. In some applications, a properly designed rivet joint can be just as strong as a welded joint.
What are the safety precautions for welding and riveting?
Safety precautions for welding include wearing appropriate personal protective equipment (PPE), such as a welding helmet, gloves, and flame-resistant clothing, ensuring proper ventilation, and being aware of fire hazards. For riveting, safety glasses should be worn to protect the eyes from flying debris, and hearing protection may be necessary when using pneumatic riveting tools.
What is the difference between arc welding and TIG welding?
Arc welding is a general term for welding processes that use an electric arc to create heat. TIG welding (Gas Tungsten Arc Welding) is a specific type of arc welding that uses a non-consumable tungsten electrode to create the arc and an inert gas (such as argon) to shield the weld area from contamination.
Why would someone choose riveting instead of welding?
Someone might choose riveting instead of welding for a variety of reasons. These could be cost related, as riveting is generally less expensive and quicker than welding. The materials themselves may dictate the need for one solution over the other – welding may damage the materials if they’re too thin or heat sensitive, so riveting may be chosen. Finally, if disassembly is a possibility, riveting will be the preferred solution.
Here are the key takeaways to remember when considering welding vs riveting for your next project:
Welding creates strong, permanent joints by fusing metals together.
Riveting uses mechanical fasteners to join materials quickly and cost-effectively.
Welding is ideal for thick materials and applications requiring maximum strength.
Riveting is well-suited for thin sheet metal and joining dissimilar materials.
Welding can cause heat distortion, while riveting does not.
Welding requires skilled labor, while riveting is easier to learn.
Riveting is generally faster and less expensive than welding.
Welding offers better structural integrity in most cases, but well-designed rivet joints can be very strong.
Carefully consider the specific requirements of your project to determine whether welding or riveting is the best choice.
By understanding the nuances of each method, you can make an informed decision that will ensure the success of your project. Remember, we at CNC Fabrication Services are here to help you navigate these choices and provide you with the best possible fabrication solutions. Our expertise in CNC solutions, including on-demand manufacturing and rapid prototyping, ensures that we can meet your specific needs with precision and efficiency. Contact us today to discuss your project and let us help you bring your ideas to life.
Get the latest trends and facts about CNC fabrication from our blog.
Shenzhen Runkey Precision Technology Co. Ltd, a subsidiary of the Tensun Group, is your trusted one-stop solution for custom manufacturing from prototyping to production.Transforming your idea into reality with digital manufacturing resources,streamlined processes, expert guidance,accelerated timelines, and uncompromising quality.
©2024. CNC Fabrication All Rights Reserved.