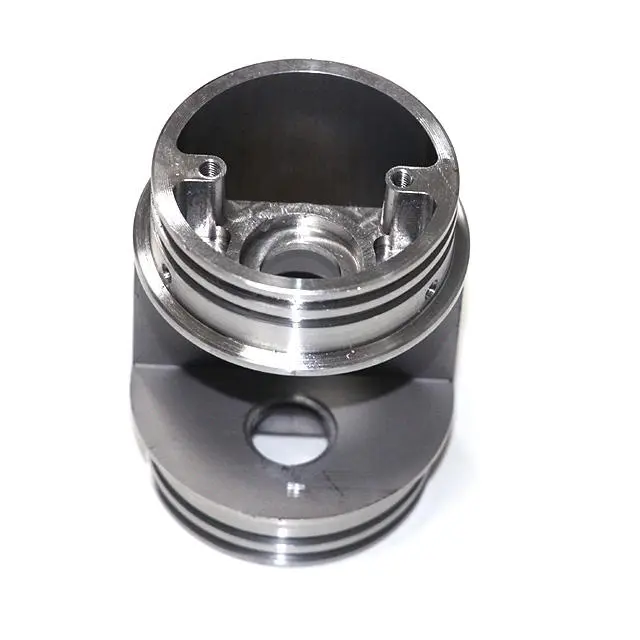
- +8615586668226
- [email protected]
- No. 30, Hongbang Industrial Park, Shenzhen
Wire EDM, or wire electrical discharge machining, is a non-traditional machining process that uses a thin metal wire as an electrode to cut through conductive materials. I’ve seen firsthand how this process can create incredibly intricate and precise parts. The wire, typically made of brass or copper, is fed through the workpiece, and electrical discharges are generated between the wire and the material. These sparks erode the metal, creating the desired shape.
Wire EDM is known for its ability to achieve extremely tight tolerances and excellent surface finish. In my experience, it’s especially useful for creating complex shapes, sharp corners, and delicate features that would be difficult or impossible to achieve with conventional machining methods. It’s a precise process suitable for hard materials like titanium, and Inconel, often used in aerospace and medical industries. Wire EDM services provide intricate part creation with high accuracy.
Conventional CNC machining, on the other hand, is a subtractive machining process that uses rotating cutting tools, such as end mill or drills, to remove material from a solid block of metal or other material. CNC machines are computer-controlled, allowing for precise and repeatable movements. You can think of them like highly advanced milling machines that can follow complex instructions to create intricate parts.
CNC machining is a versatile process that can be used to create a wide range of parts, from simple shapes to complex geometries. It’s widely used in industries like automotive, aerospace, and consumer products. Having worked with CNC machines, I can attest to their ability to produce high-quality parts with good accuracy. They are perfect for machining various metals, plastics, and composites. Precision Machining is one of the great CNC machining services we offer.
When comparing wire EDM vs. CNC, it’s essential to understand their fundamental differences. Wire EDM is a non-contact process, meaning the wire never physically touches the workpiece. This eliminates the risk of mechanical stress and distortion, making it ideal for delicate parts. CNC machining, however, involves direct contact between the cutting tool and the material, which can generate heat and stress.
Feature | Wire EDM | Conventional CNC Machining |
Contact | Non-contact | Contact |
Cutting Mechanism | Electrical discharges | Physical cutting with rotating tools |
Material Removal | Erosion | Cutting/Shearing |
Material Compatibility | Conductive materials only | Wide range of materials, including non-conductive |
Tolerance | Extremely tight (±0.0001 inches) | Tight (±0.001 inches) |
Surface Finish | Excellent, often mirror-like | Good, depends on tooling and parameters |
Corner Radius | Very small, limited by wire diameter | Limited by tool radius |
Cutting Force | Minimal | Significant, can cause deflection |
Heat Affected Zone | Small | Larger, can affect material properties |
Setup Time | Can be longer due to wire threading | Generally shorter |
Tool Wear | Wire is continuously fed, minimal wear | Cutting tools wear and need replacement |
Another key difference is the type of materials they can handle. Wire EDM is limited to conductive materials, while CNC machining can process a wider range of materials, including non-conductive ones like plastics and composites. In my experience, the choice between wire EDM and CNC often comes down to the specific material and the complexity of the part.
So, when should you use wire EDM? This is a question I get asked a lot. Wire EDM is the go-to choice when you need extreme precision, intricate details, or when working with hard materials. If your part has sharp internal corners, thin walls, or delicate features, wire EDM is likely the better option. It is especially suited for machining tough metals.
Wire EDM is also ideal for creating prototypes and small-batch production runs. Because it’s a non-contact process, there’s no need for expensive tooling, making it cost-effective for low-volume manufacturing. In my work, I’ve seen wire EDM used to create everything from medical implants to aerospace components, demonstrating its versatility. Also, 5 Axis CNC Machining is a good example of our wire EDM services.
Wire EDM is particularly well-suited for hard materials that are difficult to machine using conventional methods. Materials like hardened tool steels, titanium alloys, Inconel, and carbide are excellent candidates for wire EDM. The wire EDM process can cut these materials with ease, without causing excessive tool wear or heat damage.
Here’s a list of materials commonly used in wire EDM:
Tool Steels (D2, A2, S7, etc.)
Stainless Steels (304, 316, 17-4 PH, etc.)
Titanium Alloys (Grade 2, Grade 5, etc.)
Inconel (625, 718, etc.)
Carbide
Copper
Aluminum (certain grades)
Brass
It’s important to remember that the material must be electrically conductive for wire EDM to work. If you’re unsure whether your material is suitable, it’s always best to consult with a wire EDM specialist. Many wire EDM machines use various types of wire depending on material.
The advantages of using wire EDM are numerous, especially when dealing with complex and precise parts. One of the biggest advantages is the ability to achieve extremely tight tolerances, often as small as ±0.0001 inches. This level of precision is difficult to match with conventional CNC equipment.
Wire EDM also excels at creating intricate shapes and features. The thin wire can navigate tight corners and create small internal radii, making it perfect for complex machining applications. Additionally, the non-contact nature of the process means there’s minimal stress on the workpiece, resulting in parts with excellent dimensional stability and a superior surface finish. Wire EDM makes the best parts with the best surface finish.
Wire EDM can also cut extremely hard materials, providing superior results compared to other machining techniques.
While wire EDM is a powerful machining technique, it’s not the only type of EDM. Sinker EDM, also known as ram EDM, is another popular method. So, how does wire EDM compare to sinker EDM? The main difference lies in the electrode. Sinker EDM uses a custom-shaped electrode, often made of graphite, to “sink” into the workpiece and create the desired shape. Wire EDM machine tools can create custom parts with ease.
Wire EDM is generally better suited for creating through-holes and complex profiles, while sinker EDM is ideal for creating blind cavities and intricate 3D shapes. Sinker EDM uses an electrode to form the part, unlike wire EDM. In my experience, wire EDM offers better surface finish and tighter tolerances than sinker EDM for through-cuts. Wire EDM is also faster for many applications, making it a more efficient choice in those cases. Wire EDM uses a unique cutting process.
Despite its many advantages, wire EDM does have some limitations. One of the main drawbacks is that it can only be used on conductive materials. This means that materials like plastics, ceramics, and composites cannot be processed using wire EDM. Additionally, the wire EDM process can be slower than conventional machining for simple parts.
Another limitation is the size of the workpiece. Wire EDM machines have a limited travel range, so they may not be suitable for very large parts. The wire can also break during the cutting process, which can lead to downtime and increased costs. It’s important to carefully consider these limitations when deciding whether wire EDM is the right choice for your project. CNC wire EDM is a great technology, but it has its limitations.
Choosing between wire EDM and CNC can be a tough decision. In my experience, the best approach is to carefully evaluate the specific requirements of your project. Consider the material, the complexity of the part, the required tolerances, and the desired surface finish. Using wire EDM instead of traditional CNC may be the best option.
If you need to machine a non-conductive material, CNC machining is the only option. If you need to create a simple part with loose tolerances, conventional CNC is likely the more cost-effective choice. However, if you need extreme precision, intricate details, or are working with a hard, conductive material, wire EDM is often the better choice. It’s also worth considering the production volume. Wire EDM is often more cost-effective for low-volume production, while CNC machining may be more economical for high-volume runs. Wire EDM excels in creating small, intricate parts.
Wire EDM can make many precise parts that many CNC machines cannot make.
With its ability to create incredibly precise and complex parts, wire EDM is undoubtedly playing an increasingly important role in the future of manufacturing. As industries like aerospace, medical devices, and electronics continue to demand smaller, more intricate components, the demand for wire EDM is likely to grow. It is a complex machining process that many manufacturers are using.
In my opinion, wire EDM is not going to replace conventional CNC machining entirely. Instead, I see the two technologies as complementary. Wire EDM will continue to excel in niche applications where extreme precision and intricate details are required, while CNC machining will remain the workhorse for a wide range of general machining tasks. Wire EDM is becoming more popular in EDM manufacturing.
What is the typical tolerance achievable with wire EDM?
Wire EDM can achieve extremely tight tolerances, typically in the range of ±0.0001 to ±0.0005 inches. The exact tolerance depends on factors like the machine, the wire type, the material being cut, and the machining conditions.
What is the maximum thickness that wire EDM can cut?
The maximum cutting thickness in wire EDM depends on the specific machine and its power capabilities. Generally, wire EDM machines can cut thicknesses up to 12 inches or more. However, cutting thicker materials may require multiple passes and can be slower.
Can wire EDM create sharp internal corners?
Yes, one of the key advantages of wire EDM is its ability to create very sharp internal corners. The minimum achievable internal radius is limited by the diameter of the wire being used, typically ranging from 0.004 to 0.012 inches. Wire EDM can achieve very small radii.
Is wire EDM suitable for high-volume production?
Wire EDM is generally more suitable for low to medium-volume production runs or for creating prototypes. While it can be used for high-volume production in certain cases, it may not be as cost-effective as conventional machining methods like CNC milling or turning for simple parts.
How much does wire EDM cost?
The cost of wire EDM can vary depending on factors such as the complexity of the part, the material being cut, the required tolerances, the machine time, and the setup time. Generally, wire EDM tends to be more expensive than conventional machining for simple parts but can be more cost-effective for complex parts or hard materials.
Can wire EDM cut any conductive material?
Wire EDM can cut any electrically conductive material. This includes most metals, such as steel, aluminum, copper, brass, titanium, and various alloys. The material’s hardness and thickness can affect the cutting speed and wire wear.
Wire EDM is a specialized machining process that offers unparalleled precision and the ability to create intricate shapes in conductive materials.
Conventional CNC machining is a versatile process that can handle a wider range of materials and is generally more cost-effective for simpler parts.
The choice between wire EDM and CNC depends on factors like material, part complexity, tolerances, surface finish requirements, and production volume.
Wire EDM excels in applications requiring extreme precision, sharp corners, thin walls, and the machining of hard materials.
Wire EDM is likely to play an increasingly important role in the future of manufacturing, particularly in industries that demand miniaturization and high precision.
Consider consulting with a machining expert to determine the best approach for your specific project.
As a cnc fabrication services provider, we understand the intricacies of both wire EDM and CNC machining. Our state-of-the-art manufacturing plants are equipped to handle a wide range of projects, from aerospace and automotive components to medical devices and consumer products. We cater to diverse industries, including Aerospace and Aviation, Automotive, Medical Devices, Electronics, Defense and Military, Industrial Equipment, Consumer Products, Energy and Renewable Energy, Robotics, Construction and Architecture, Tooling and Dies, Food and Packaging, Pharmaceuticals, Heavy Equipment, Custom Projects/Prototyping, Art and Design, Telecommunications, and Packaging. Let us help you bring your designs to life with unmatched precision and quality. Contact us today to discuss your project and experience the difference that our expertise can make! CNC Solutions can make the difference for you. Our expertise in Surface Finishing and Rapid Prototyping can make your product stand out.
Get the latest trends and facts about CNC fabrication from our blog.
Shenzhen Runkey Precision Technology Co. Ltd, a subsidiary of the Tensun Group, is your trusted one-stop solution for custom manufacturing from prototyping to production.Transforming your idea into reality with digital manufacturing resources,streamlined processes, expert guidance,accelerated timelines, and uncompromising quality.
©2024. CNC Fabrication All Rights Reserved.